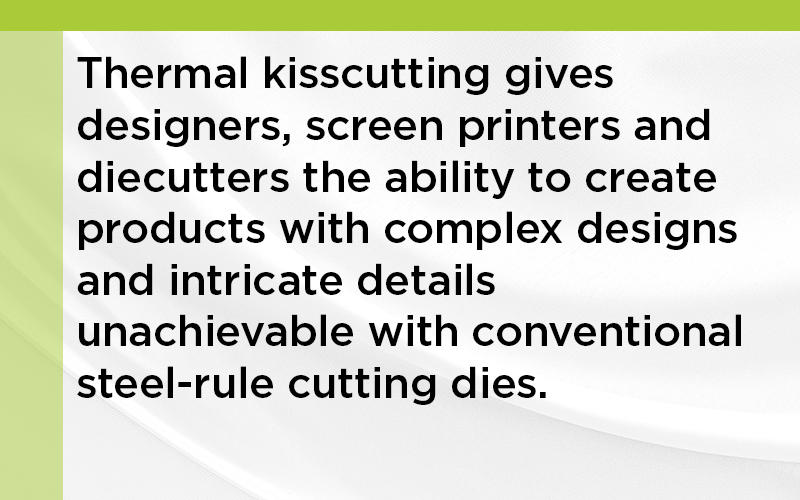
by Doug Pendergast, Owosso Graphic Arts, Inc.
Also known as thermal diecutting, thermal kisscutting gives designers, screen printers and diecutters the ability to create products with complex designs and intricate details unachievable with conventional steel-rule cutting dies. Any platen press with heat, dwell and pressure can thermal kisscut, including clamshell and four-post presses. The market for thermal dies continues to grow because they are easy to use and the vinyls that thermal dies can cut have a wide range of uses.
What is thermal kisscutting used for?
Fleet markings to self-adhesive alphabets, from delicate pin stripings to splattered-effect decals, from kid’s stickers to safety signage, thermal kisscutting offers a world of possibilities for the graphic arts industry. New pressure-sensitive vinyls are available for a broad spectrum of applications, including indoors, outdoors, underwater, low-temperature and reflective, just to name a few.
How does it work?
“Cutting” might be a misleading word. Melting is actually more accurate. In order to melt the face of pressure-sensitive vinyls, thermal dies use a combination of three factors: heat, dwell time and pressure. However, thermal dies just “kiss” the vinyl, leaving the paper liner, or carrier, intact. Of course, different combinations of heat, dwell and pressure are necessary for crisp, sharp “cutting” of the various types of vinyls. Keeping these three factors in check will reduce the build-up of melted vinyl on the shoulders of the die.
What type of makeready is needed when using thermal cutting dies?
Properly mounted dies on a well-maintained press hardly require makeready since the surface of the die is of even height. An even counter board underlay, such as poster board, chip board or polyurethane, will help in cutting. It also will protect the edges of the die from dulling or smashing.
How do you keep the vinyl from sticking to the die?
A Teflon-like coating can be applied to the die prior to thermal cutting. This allows the material to slide off the die without sticking. Release coatings are most helpful on fine detail and difficult jobs. Even with the newer release agents, remember to keep heat settings in check. Too much heat will result in burned material, raised ridges on part edges and, in some cases, cut parts that get heat-welded to the backing sheets.
Whats the largest die that I can use for thermal kisscutting, and how do I prevent the overexpansion of the die?
The largest single piece die that can be chemically etched for thermal kisscutting is 120×30″, with an image area of 119.5×29.5″. Using the Magnesium Die Thermal Expansion Formula, you can precisely calculate the amount of expansion the die will have. This is mainly needed when matching to a pre-printed area.
Are there special instructions for ordering thermal cutting dies?
When ordering, information such as pressure-sensitive vinyl thickness, image size, image right/wrong reading and other general information are required.
Are there special instructions for storing thermal cutting dies?
When finished cutting, it is best to remove the die from the press while it is still hot, gently prying it off (the hotter the die is, the easier it will come off). Take care not to let it fall face down. Before the die cools, use a natural-fiber brush to scrub off any residues. Dies are easier to clean while still at cutting temperature. To avoid magnesium corrosion, coat the die with something like Pam™ cooking spray. Of course, this prevention is not necessary if the dies are already coated with a Teflon-like release coating. In addition, dies will last longer when stored in a low-moisture, chemical-free atmosphere.
Doug Pendergast is national account director for Owosso Graphic Arts, Inc., Owosso, MI. Since 1949, Owosso has been creating dies for letterpress, halftones, embossing, debossing and foil stamping in addition to thermal kisscutting, membrane switch overlay embossing, fabric embossing, soap stamps and heat sealing dies. For more information, visit www.owosso.com.