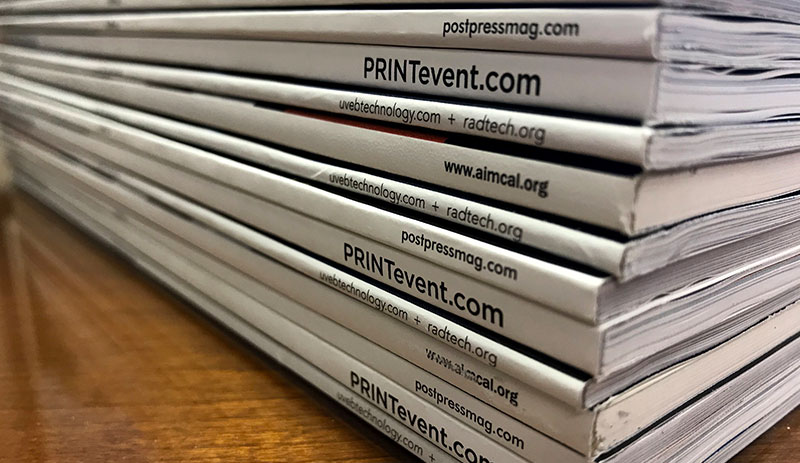
by Jeff Peterson, editor-in-chief
PostPress
Perfect binding is an economic, attractive way to present information in a bound format for both short and long runs. Once viewed as a binding method for thick books or publications, perfect binders today are designed for quick turnarounds and much shorter runs, especially for the ever-growing digital world. And, it now is feasible to perfect bind page counts as low as 32 – or even less.
With the increased flexibility of perfect binding, it does provide additional challenges for the bindery and operator. Working through these challenges early in the design and set-up of the job can save time and money before the job hits the binder.
Q. What challenges occur during the layout stage of a perfect binding job? How are these challenges overcome?
Communication is key in the layout stage. Making sure the customer understands what is required early in the process can help decrease the chance of any unwanted challenges on the perfect binder. These may seem obvious, but a few simple things should be communicated early in the process to help decrease potential problems. First, page counts must be divisible by two. Also, printing and binding with the grain parallel to the spine on the paper stock will help decrease the chances of waves or cracking at the spine and help open the book with less resistance.
Another common challenge with layout comes when there are readacross sections or cross-overs (where the image or text must align across two consecutive pages). This becomes more of a challenge when the read-across sections are on two separate signatures. It always is best to keep this type of design within the same signature if possible and try to avoid this in the design all together if the two pages are on separate signatures.
When cross-overs do occur in the layout, they must be adjusted at the spine to compensate for the fact that a perfect-bound book does not lay completely flat. This can result in elements inside the gutter becoming lost within the center of the publication. When working with cross-overs, it is recommended to move the text or image approximately 1/16″ from the spine grind allowance over the normal 1/8″ (for a total of 3/16″) to help decrease the chance that the text or image will be “lost” within the glues used in the perfect binding process.
Another important item to communicate early in the layout stage is the impact of the use of glue traps. Glue traps are necessary to keep the glue from escaping when it is applied to the spine and side hinges of the book. It is recommended that the cover signature include at least an 1/8″ overhang over the inside pages. When the cover is attached to the book block, the glue will “squish out” from the head and the foot. If the cover overhangs the other pages, the glue will be trapped within the area needed to stick the insides to the cover. Diagram 1 demonstrates a common layout with appropriate margins for a perfect binding application.
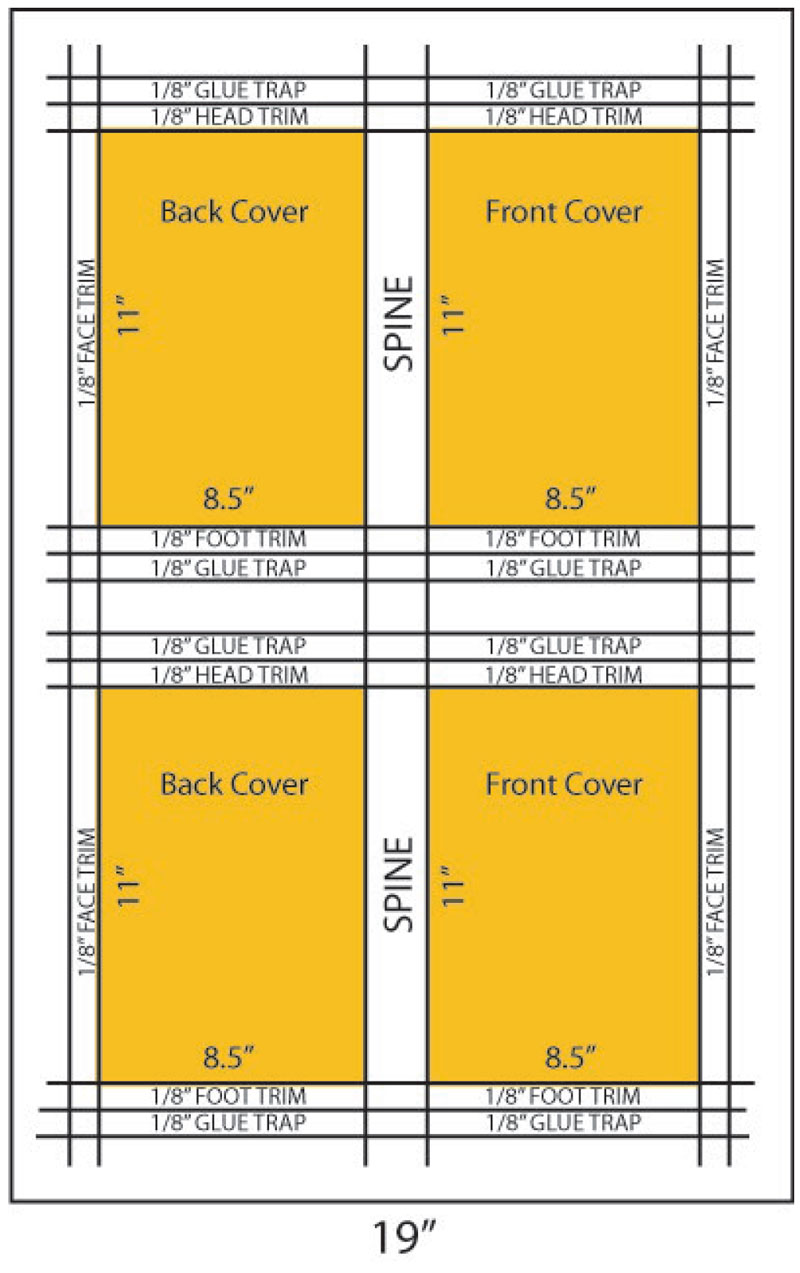
Q. How does stock thickness and/or spine thickness affect perfect bound jobs?
The thickness of the stock for the cover and inside pages can affect the speed of the perfect binder. Thicker books require slower speeds and greater accuracy in setting up the trimmer. However, thicker stocks many times will run more smoothly through the machine. It is important to know what thickness and specific type of stock that is being used to prepare for the job. Whenever possible, avoid printed 2-page sheets (2pp) on the perfect binder as they are thinner than folded signatures and can force the operator to slow down the binder speed in order to have the sheets jog-up properly with the other forms. Thinner signatures should bind between larger forms, ie: a 4pp form should bind between 16pp forms, rather than inside front or inside back cover.
Q. When are glue issues most likely to occur? How can adhesion issues be avoided?
Glue adhesion issues can occur whenever non-absorbent coatings and/or inks are used in the adhesion area. This is relevant in both the spine and side glue areas. As discussed earlier and shown in Diagram 1, knocking out these areas from inks and coatings can help eliminate glue adhesion challenges. PUR adhesives may be necessary for difficult inks/coatings and difficult stocks (see PostPress “PUR or EVA – What is the Best Adhesive Option?” November/December 2018). However, PUR adhesives are more expensive than conventional EVA adhesives.
Q. What improvements in machinery and adhesive have occurred in the last few years that decrease challenges with perfect binding?
Automation in perfect binding equipment is driven by a decline in run lengths, quicker turnaround requirements and the decreasing need for training and sophistication when running the machine. As run lengths continue to be shorter, quicker set-up and makeready times are a must.
Today’s machines have a higher degree of automation than ever before, with many different options for nozzle systems for glues; inline trimming of books with flush gatefold covers; barcode recognition for signatures and covers to prevent misfeeds; and book-block feeders. New and improved software also has an impact. Touchscreen technology today guides operators though each step of the set-up process, reducing the time required for setup and the likelihood of waste due to errors.
As stated earlier, PUR glues are versatile across a wide range of substrates and are good “go-to” adhesives for difficult jobs to avoid binding strength issues. EVA glues also have improved – with high-strength versions available for even smaller perfect binders. This type of EVA glue was developed with digitally printed work in mind, providing better pulls and reacting well to the paper being used with digital print.
PostPress would like to thank Larry Worfolk and Richard Sussey of Pacific Bindery Services Ltd. (PBS) for their assistance with this article. Located in Vancouver, Canada, PBS is the largest binder on the northwest coast, offering an array of binding and finishing solutions. Visit www.pacificbindery.com for more information.