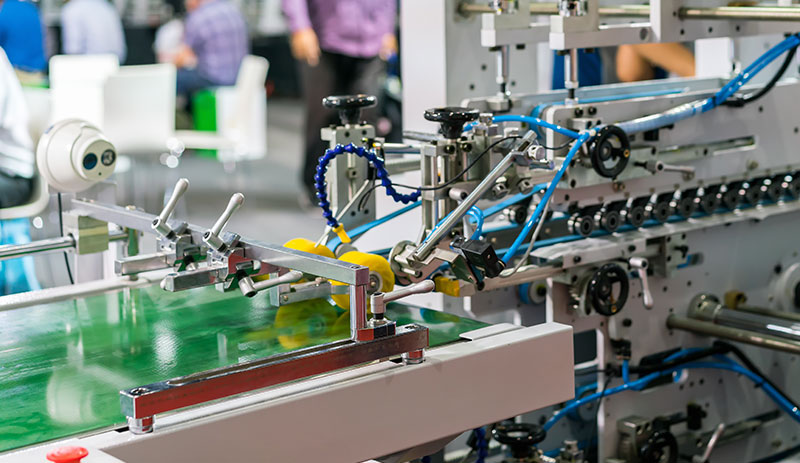
by Brad Emerson
www.fixyourownbindery.com
While bindery managers currently are inundated with an unlimited supply of “do-or-die” automation upgrades, ultimately the production and operation needs of each facility will determine which upgrades will keep the operation alive, which will put it ahead of the pack and which will constitute a significant investment with limited value added. A review of bindery automation in 2019 allows bindery managers and others in the field to consider the progress of automation on different fronts and to frame these improvements in terms of the problems they were designed to address and the tradeoffs they may require, beyond the generic “cost-saving,” “quality-enhancing” and “production-maximizing” selling points. This review presents an occasion to take inventory of utilization and return on investment of automation on the floor today and to identify opportunities for improvement.
Existing peripheral equipment
Equipment such as automatic-feed paper drills and automatic-feed poly wrapping lines present popular alternatives to more compact, manually-fed equipment. For binderies that have made or are considering these investments, it is important to keep in mind that as product mixes change over time, so will the “realized benefit” of this automated equipment.
Are we still setting up an automatic drill or wrapper – which typically requires two people to run, with longer makeready and two to three times the floorspace – for a decreasing quantity? Did we bring in extra staff for an eight-hour shift to run the automatically fed equipment for a partial shift to replace one associate on a manually fed machine? By the same token, are we slowing down a perfect binder or saddlestitcher by handfeeding when a bookblock feeder, stream feeder or additional folder feeder could allow the line to run significantly faster with the same or fewer associates?
Of course, binderies producing the highest unit cost (e.g. hardcover, personalized) pieces have the lowest fruit to grab with automated peripheral upgrades such as bundle stream feeders, bookblock feeders, cover feeders, mailtables, stackers, semi-automatic and fully-automatic carton equipment, etc. For managers considering these potential investments, it is best to go see the equipment in action, if possible, to create the best “net results” factored into the justification.
PUR (Polyurethane Reactive) adhesive upgrade
While changing adhesives may not seem like a potential automation investment – or profit center – on the surface, how we invest to apply and handle the PUR adhesive will significantly impact the long-term cost of ownership. After the numbers have been crunched for a handfed perfect binder vs. a complete inline automated perfect binder with gatherer and trimmer, there are two major choices for applying the PUR adhesive: traditional roller pot (which can make the strongest book) or a nozzle system (which sprays the PUR adhesive on the spine with minimal changeover time and material waste).
Other PUR adhesive cost and quality concerns if upgrading an existing line with PUR adhesive would be the mechanical condition of the line, the number of spine preparation tools and the precision of the clamp guidance. In addition, because PUR adhesive is more costly, it is important to monitor the amount/rate of PUR adhesive to be consumed. This will help when sizing the largest pre-melter possible to get the best per pound/liter bulk price and also will help minimize operator pre-melter changeover duties.
Signature or pocket readers
Beyond an OEM (original equipment manufacturer) image verification system’s routine maintenance recommendations for maintaining calibration, we often find many binderies are no longer running their difficult-to-use legacy image reading systems. Binderies with legacy verification systems owe it to themselves to research available upgrades to improve functionality and operator interface with the OEM. Some systems only require replacing the camera and software to enjoy the latest image and barcode features advantage and benefits.
Targeted training
We certainly are not born with the knowledge it takes to operate the latest automated equipment or to utilize every feature. Reviewing real-world obtainable net production goals with your OEM, operators and managers on a given product mix and then developing a targeted training program for success will put you on the path for continuous operations improvement.
While such programs often are dismissed as too costly, the most training-oriented binderies or bindery departments have set up some type of specific area in their plants for training. These programs use the highest-skilled team leaders to hone operator skills on a regular basis, cost-effectively ensuring that investments in automated equipment realize their promises of improved quality and net production.
Other Factors to Consider
With this review of the advancements in bindery automation, companies that are considering an upgrade in existing equipment or a new equipment purchase should look carefully at which investments are suited to their operation’s needs. And, at the same time, look at ways to better automate and organize the bindery through other means outside of equipment upgrades and/or purchases. The following questions should help guide this decision-making process:
- Has the current equipment been comprehensively evaluated by an “objective” qualified technician to determine if it is in acceptable mechanical condition going forward? Objectively decide if maintaining or adding automation to current equipment is worth the investment or if looking at new equipment that has the automation built-in is a better option.
- Do the production scheduling associates optimize the schedule for the bindery? Scheduling like-size jobs consecutively on even the most pre-historic piece of equipment may be as efficient as the highest level of automation on a new machine.
- What is the bindery capability “wish list” from existing customers, new prospects and team members? Look carefully at this and talk with customers and team members within the bindery to determine what type of automation makes the most sense.
- Should an independent bindery consultant with experience in production and automated equipment provide an evaluation with recommendations? This can help determine the best options and whether to upgrade existing bindery equipment or consider the purchase of newer, more automated bindery equipment.
- Are the current operators properly trained on the most difficult products being produced? And, do you have the proper staff for the addition of automated equipment?
- When is the last time you rethought the machine and/or entire bindery layout? Workflow and the layout of the bindery area are extremely important and should be evaluated on a regular basis – especially if new equipment is added or existing equipment is upgraded.
Brad Emerson is the general manager of www.fixyourownbindery.com, a company specializing in consultation, turnkey machine and plant relocations, new and used equipment sales, machine reconditioning, automation, custom fabrication and training. Emerson’s bindery background includes bindery supervision as well as bindery equipment marketing and consultation. For more information, comments, questions or criticism, email brad@fixyourownbindery.com.