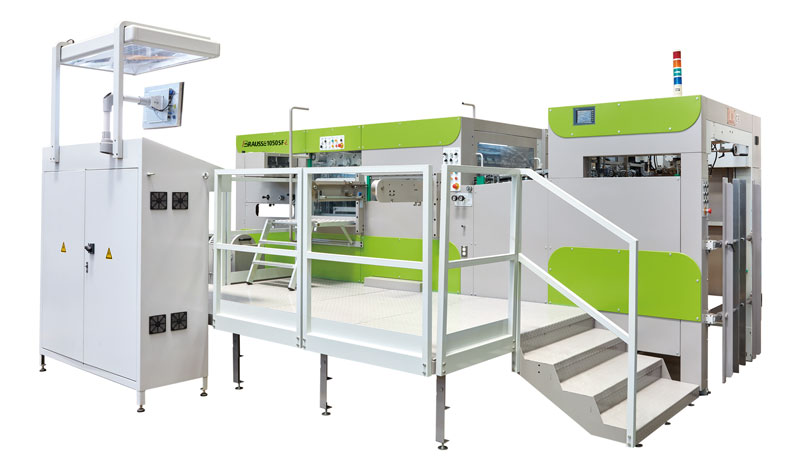
by Lara Copeland, contributing editor
PostPress
Brausse Group, a member of the Bobst Group since 2012 and headquartered in Vancouver, Canada, provides machinery that now incorporates proven group technology, delivering an excellent product at an affordable price. With over 30 years of experience in design and manufacturing of its diecutting and folder-gluer machines, the company’s Brausse 1050SFi foil stamper and diecutter comes with a number of high-end features.
“With Brausse being a member of Bobst Group, proven group technology and existing technology in electronics engineering and functionality can be seen throughout the press,” said Matthew Sharp director of sales and marketing at Brausse Group North America. The foil stamping and diecutting controls are easy to use on the computer’s touchscreen, and “with our Advanced Foil Control System (AFCS), which provides reliable and precise foil-advancing controls, the operators can make any adjustments during operation,” he added. The press includes a pneumatic, push-button die chase locking mechanism to ensure safe and operator-friendly die changing, which eliminates the use of a wrench to remove the chase. A slanted feed table allows for stable and accurate registration, especially for lightweight paper at high speeds. The sheet stretching air blower included in the delivery section lets the operator add air as needed to help the sheets to lay flat. “This helps during fast speeds,” Sharp commented.
The 1050SFi assists operators in reducing downtime during runs. “This piece of equipment allows the operator to make a number of important changes to the machine while it still is running, which helps reduce downtime,” Sharp said. Additionally, with both an automatic feeder and delivery section, the press does not have to stop when adding more material or removing finished product.
More updated components of the machine make the 1050SFi something operators can use with ease, resulting in efficiency. A redesigned platen offers a more leveled impression to reduce makeready time, while a precision ground 15 mm-thickness insulation plate located behind the heating base optimizes heating efficiency and maintains constant temperature. A sandwich plate with micro-adjustment in both running and cross direction allows for quick set-up and facilitates effortless makeready. The push and pull side lays (OS and OOS0 with photo sensor sheet arrival control) are easy to use as well. A self-diagnostic touchscreen detects the location of an alert and provides information on how to repair or clear an error. The pneumatic one-push, button-activated safety doors are operator-friendly. Finally, the machine comes equipped with a tape inserter that has a counter which allows the operator to pre-set and insert a piece of paper tape to mark the load.
“We are extremely happy with the 1050SFi,” Sharp exclaimed. “By utilizing proven group technology, we have brought a very advanced press to the market at a very reasonable price point.” In fact, customers already are responding positively to the new technology. Sharp said that due to the price point of the press and all the improved features, “the response has been fantastic.” Operators also are pleased.
Technical Details
The Brausse 1050SFi foil stamper and diecutter features a max speed of 7,500 sheets per hour. The machine also offers 300 tons maximum cutting pressure. Folding carton stock range is 90g/m2 to 600g/m2. Corrugated stock range is maximum 4 mm
(B Flute).