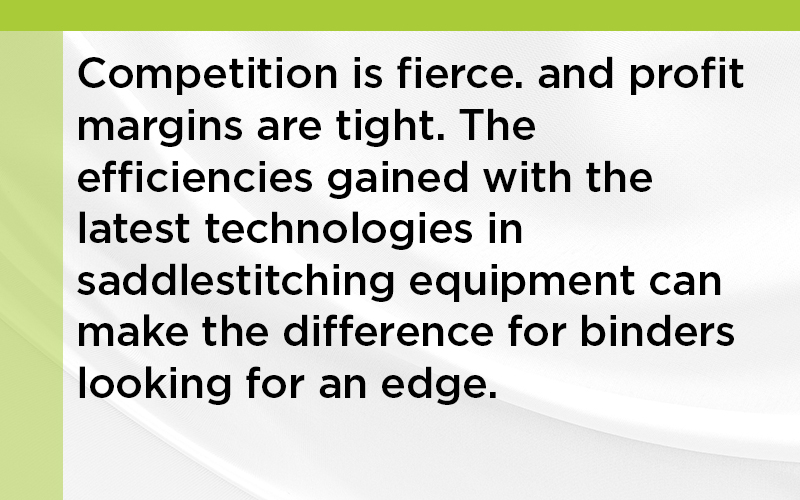
by: Renée Varella
Binderies look to reduce production costs through automation and other innovations that offer quick set-ups and changeovers. Here’s an overview of saddlestitching technologies and equipment upgrades from five companies, all designed to enhance efficiencies – and profits.
Automation Options
Automation and other technologies in the saddlestitching process can save set-up time, help binderies use materials more efficiently, and reduce the number of operators required to do a job. For example, Standard Horizon’s automated StitchLiner 5500 gathers flat 4-page signatures, scores, plow-folds, and then drops the sheets onto a saddle for stitching. A single operator can run the machine, which features large, icon-based color touchscreens, prompting the operator through all set-up steps. The operator selects the graphically-represented finishing style, inputs sheet dimensions and other parameters, and then stepper-motors drive all of the substations to the correct settings. The commercial-duty system can handle up to 50 physical sheets (200-page booklets); job changeovers can be completed in three minutes or less.
“The process has another advantage, too,” said Mark Hunt, director of marketing for Standard Finishing Systems. “With conventional saddlestitching, parent sheets are printed 8- or 16-up and then signature-folded, but booklet production cannot start until all of the signatures have been prepared. With the StitchLiner, production can start immediately after printing, allowing partial deliveries or a jump-start on the next downstream process, such as mailing and inserting.”
Heidelberg’s Stitchmaster ST 450, for mostly short-run jobs, offers advanced automation features, quick make-ready, and fast changeover. A touchscreen controls automatic synchronization of machine aggregates and automatic format presetting for feeders, trimmer, and compensating stacker. The ST 450 runs at speeds up to 14,000 cycles per hour.
With the Stitchmaster ST 450, an operator can configure as many as 32 pockets to the specific requirements of any job. Pockets can be moved easily and placed anywhere on either side of the saddle chain, automatically synchronizing to the chain based on the format and the cycle speed. When coupled with the independent servo-motor drive, which helps send electronic job tickets for automatic presetting, these features create flexibility and automation for any type of stitching job. Servo-motors and stepping-motors eliminate the need for moving of guides by hand – creating a faster, synchronized makeready time.
Heidelberg’s ST 350, which runs at 12,000 cycles per hour, offers a semi-automated solution for work that tends to keep the stitching line in continuous from small- to high-volume operation. The central graphical touchscreen and controls on every unit enable automatic synchronization of the saddle chain with feeders and the stitcher. Heidelberg’s ST 90 and ST 100 models, for small- to medium-volume production, run up to 9,000 cycles per hour, with easy changeover and operation. Both models allow a printer to keep jobs in-house for complete finishing.
Vijuk Equipment’s 321-T saddlestitcher automatically feeds and gathers signatures through its independently-driven horizontal feeders. The in-line cover feeder/folder offers regulated air blasts for dependable feeding, and on-the-fly adjustment for cover alignment and scoring. The 321-T also offers high-quality control with missing- , double- , and dropped-signature detection in each feeder, in addition to an oblique monitor for signature registration, an over/under caliper, and missing-stitch detection.
“The 321-T stitcher offers an optional programmable, in-line, digital, variable-data ink-jetting system with dual print heads that simultaneously ink-jets the outside and inside of booklets,” said Kevin Boivin, sales coordinator for Vijuk Equipment. “An in-line multi-purpose trimmer that performs perimeter diecutting, interior diecutting, hole punching, perforating, and trimming of booklets in 1- to 3-up formats can be attached.” The CE-certified machine is rated at 10,000 cycles per hour, and 2-up production is available.
Other Innovations
New stitching technology can be found in the MBM Corporation’s StitchFold bookletmaker, an ISP wire-fed stitching system that offers lower operating costs than systems using pre-formed staples. The StitchFold can produce booklets up to 100 pages, and jogs, stitches, and folds up to 65,000 booklets without the need to replace the wire spools. Magnetic stitching heads feature one-step threading for quick and easy set-up, and the knife fold with dual-fold rollers provides crisp, consistent folds.
The Deluxe Stitcher Company manufactures a range of freestanding machines, stitcher heads, and replacement component parts for nearly all makes and models of stitcher machines and heads. Multiple-head machines include the pamphlet-making M17 Stitcher, the versatile M27 pad stitcher, and the Behemoth 18AW that takes up to 10 heads. Deluxe multi-head stitchers are designed to increase productivity with the ability to put in as many as 10 stitches in one cycle.
Cost Savings for Customers
In addition to wanting features that simplify production, binderies aim to reduce customers’ costs. Heidelberg’s Stitchmaster equipment can save time and effort in the final phase of a job, where delays in prepress and printing often have to be made up. Digital controls and sophisticated technology help Stitchmaster operators avoid post press “bottlenecks” and higher productivity in the bindery means high-quality jobs are finished in less time.
“Customers using Standard Horizon’s automated saddlestitching systems can efficiently process short-run jobs with lower set-up labor costs v. conventional saddlebinding lines, Hunt said. Operators input job parameters on the color touchscreen, then precision stepper-motors drive all sub-systems – such as side guides, end stops, stitching heads, and trimming knives – to the correct position in minutes. “Automated systems also have a great deal of the set-up intelligence ‘built-in,’ so customers can rely less on specialized operator skill,” he said.
“One trade binder decided to put our ‘easy-to-operate’ claims to the test, and pulled an employee from shipping and receiving to run our system,” Hunt added. “That employee was subsequently promoted and is still running the StitchLiner, overseeing several million booklets through the system. Trade binders with the right automated equipment now can compete effectively and make money on short-run work that they used to turn away.”
Boivin notes that Vijuk’s 321-T offers many of the top mechanical features of comparable computerized saddlestitchers, including a flying stitching-head system and Hohner stitching heads, allowing operations of any size to upgrade their binding capabilities. “The 321-T is designed and priced for printers who cannot justify computerized automation and highly skilled labor,” he said. “Our customers cite labor savings because of how quickly employees can be trained to operate the system. With the 321-T’s comprehensive quality-control features, customers realize material savings almost immediately.”
Competition is fierce. and profit margins are tight. The efficiencies gained with the latest technologies in saddlestitching equipment can make the difference for binders looking for an edge.
Our thanks to the following companies for contributing information to this article: Deluxe Stitcher Company, (800) 634-0810, www.deluxebostitch.com; Heidelberg, (888) 472-9655, www.us.heidelberg.com,; MBM Corporation, (800) 223-2508, www.mbmcorp.com; Standard Horizon, (877) 404-4460, www.sdmc.com; and Vijuk Equipment, (630) 530-2203, www.vijukequip.com.