
By Richard Pallante, president USA and Canada, Baumer hhs
Quality control systems are not new to the folding/gluing and finishing industry, but there have been continued improvements in recent years, and the need for these types of systems is as important now as ever before. PostPress asked the experts at Baumer hhs for their input on the importance of quality control systems and what customers should look for when including quality control on new equipment or adding it to existing equipment.
What benefits do advanced quality control systems provide folder-gluers?
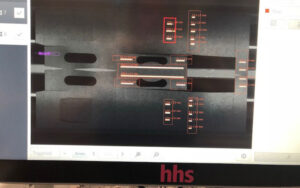
Suppliers that offer advanced quality control systems are providing a key competitive advantage to OEMs and their end customers. The ability to confirm to customers that their production runs have been checked for product accuracy and gluing accuracy reduces stress on all sides. With reduced access to trained labor, there are simply not as many experienced folding/gluing operators as in the past. Additionally, operators have many more responsibilities than just running the folder-gluer. A quality control system will catch issues that can arise from unintentional operator errors in set-up or operations and prevent incorrectly manufactured cartons from being shipped to a customer.
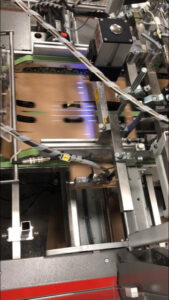
This is extremely important for the pharmaceutical industry where quality control validation is required as there can be severe legal and human ramifications if a product is mislabeled or improperly packaged. Additionally, manufacturing has changed. Long carton runs on the same machine no longer are the norm. Shorter runs with multiple set-ups per day are the new norm and can allow for more opportunities for possible errors. An advanced quality control system can provide that additional level of security to protect the operator, reduce waste and provide ultimate customer satisfaction. It truly becomes more economical to have a quality control system than not to have one, and consulting with a knowledgeable, experienced glue dispensing and verification system manufacturer can help customers find the best technology for their applications.
What features should customers be looking for when installing a quality control system?
It certainly is recommended that customers do their homework and talk to others in the industry who have purchased a QC system or have one that was included with their original folder-gluer. A reputation in the market is a good first cut on who to consider working with before purchasing a quality control solution. If the QC system is difficult to use, then end users are not going to get the full benefits from it and operators are going to try and bypass it instead of using it. Companies should be looking for ways that they can validate that the products are properly manufactured.
The following are some key questions to ask before investing in a quality control system:
- Who offers the most solutions (glue detection, code detection, camera-based detection)?
- Can verification data be downloaded and shared
with the customer? - Can the faulty product in the production process be traced?
- Can the sensors differentiate between wet glue and
cured glue? - Is the operator able to validate presence and placement of adhesive or a code?
Customers need to know how the system works and how it processes the data. Just knowing that the product did not kick out does not always mean it is good. How the operator sets up the system and what parameters are being measured need to be understood. Verification systems only are beneficial if the user finds value in using them.
Are different types of systems and sensors needed for hot melt glue vs. cold glue?
Cold glue and hot melt both are adhesives but have different makeup and characteristics. Cold glue is an emulsion where the glue is carried in another medium, such as water. When detecting cold glue, quality control companies will try and detect the water medium or will add another ingredient, such as an ultraviolet (UV) tracer. So, for a cold glue system, the glue itself is not really being detected but rather the carrier or additives used for it. A cold glue QC system could use a moisture sensor to detect the amount of water. These are small sensors and widely used in the industry. Typically, the sensor shines a light into the glue bead and measures the spectrum of light that reflects back to the sensor that is not absorbed by the cold glue. It compares this absorption with the background. If the background is damp or wet, it can skew the readings, resulting in inaccurate verification results. Fortunately, wet or damp cartons are not the norm.
UV tracers have their own challenges. With the increased use of UV inks and specialty UV coatings, the UV additives make the board indiscernible from the UV tracer in the glue, so the UV sensors cannot tell the difference between the two. This can create all types of challenges on the folder-gluer.
Hot melt detection is done with a thermopile detector. The sensor is looking for the temperature difference between the paperboard and the glue and is typically placed close to where the hot melt is dispensed from the hot melt applicator to achieve the largest temperature difference possible. The sensors need to be kept at least 30 mm away from the heated hot melt gun in order not to affect the functionality of the hot melt sensor. Some hot melt sensors can limit the line speed of the folder-gluer machine as it can become saturated and no longer process the temperature difference. This limitation needs to be discussed before choosing a hot melt sensor.
Besides cold glue and hot melt sensors, camera systems can be used as well. Cameras can take a digital picture of each product and compare it with a baseline picture where the patterns or codes have been verified. If a picture varies from the original picture, the product is identified as non-conforming and is marked or mechanically removed from the production line. Camera systems also have traceability capability, so if a product is found to be faulty after delivery to the customer, if marked or time coded, it can be traced back to time of production, the machine it was processed on and the operator involved. These additional capabilities bring a great deal of value, and, therefore, camera-based quality control systems are more expensive than standard sensor-based systems.
When is adding a camera system on the glue line suggested? What added advantages does it offer?
When choosing a camera vs. a sensor-based quality control solution, it comes down to the following issues:
- Economics/number of glue lines – A beverage carrier can require 16 cold glue guns to glue the carrier. This means there are 16 separate lines of glue patterns that must be verified. In a sensor-based system, 16 individual sensors are required, where a single camera could provide the needed verification. So, in this scenario, a camera system can be determined to be a very feasible option for quality control. Considering the opposite scenario with a single gun, straight-line system only requiring a single sensor, a camera-based system could be an over-investment. Because of the wide variation in patterns, cartons, operator preference and set-ups, there unfortunately is not an easy way to say there is a general tipping point where the decision goes from sensor to camera. The decision is best discussed with a gluing and QC specialist.
- Set-up time/makeready – Adhesive sensors are quick to set up. They usually are mounted directly to the dispensing guns and follow where they are mounted on the machine. They require a simple teaching function where they memorize the correct pattern and tolerances and monitor them through the run. A camera system will require proper lighting and mounting that allows it to see the entire pattern. If a new carton is run, a completely new set-up needs to be undertaken, adding time to the set-up. So, the length of the normal runs by the customer can have an impact on the decision between a camera system and using sensors. If a customer is changing over continuously, a camera system may not be very feasible. However, if a machine is running a particular job over and over, it may well be worth the investment.
- Traceability – A camera system will store a picture of each carton and can allow the operator to trace a potential issue all the way back to the actual creation of that carton. A sensor system will not be able to provide a visual output of what was good or bad about the carton. If the customer received a series of bad cartons, a picture can show what the cause was while a sensor-based system will require the manufacturer to tear open the carton and play sleuth to figure out what happened.
What projects or industries are best suited to take advantage of a quality control system?
Almost all types of cartons or other folding/gluing work can benefit from a quality control system, but it really comes down to who is willing to pay for it. It is similar to buying insurance in that hopefully it never needs to be used, but it is good to have if something goes wrong. How much does it cost to get a semi-trailer full of pallets of cartons back because some of them were not glued? Doing this once may not equal the amount invested in a quality control system, but how much is the manufacturer’s name worth? Is it worth the risk of having the quality of the shop questioned?
There are specific industries that benefit the most from a quality control system. Pharmaceutical, food processing, and health and beauty are good candidates. Each company could be critically impacted if a product were mixed, not sealed or incorrectly packaged. A mistake could prove fatal. While it is unlikely to happen, it is not worth the risk.
Baumer hhs is a leading supplier of glue extrusion and quality control systems for the folding carton and print finishing industries. For more information, visit www.baumerhhs.com.