
By Gary A. Jones, director, EHS Affairs, Specialty Graphic Imaging Association
Despite what many may think, the concept of sustainability is not new and has been evolving for decades. To some extent, the roots of sustainability were born with the conservation movement that was spearheaded by President Teddy Roosevelt, who worked hard to establish the national parks system. Since then, the focus of sustainability has grown to encompass an examination of just about all aspects of daily life and a search to find approaches, products and services that have a positive impact on the planet.
Sustainability background and emergence of the circular economy
Modern sustainability emerged in the mid to late 1980s with the publishing of a report titled “Our Common Future,” also known as the “Brundtland Report,” in 1987 by the UN’s World Commission for Environment and Development, chaired by former Norwegian Prime Minister Gro Harlem Brundtland. The report defined the principle of sustainable development as, “development that meets the needs of the present without compromising the ability of future generations to meet their own needs.”
There was a period after the release of “Our Common Future” before the sustainability movement became a hot topic for the printing industry. The question about what is a “green printer” began in earnest in the mid 2000s and reached a crescendo near the end of the decade. In response, the printing industry created and launched the Sustainable Green Printing Partnership (www.sgppartnership.org), an independent third-party certification program addressing sustainable print manufacturing.
During the last decade, sustainability in the print industry focused on the packaging and point-of-purchase displays market, with many print customers requiring their products to be both sustainable and manufactured in a sustainable fashion. Then, in 2018, a sustainable tsunami hit the world, with tremendous ramifications.
Two events focused targeted attention to the issue of sustainability. First, National Geographic launched a campaign to reduce waste from plastic products, such as single-use bags and straws, called “Planet or Plastics?” The National Geographic initiative not only included an awareness campaign about plastics pollution but also addressed investments in research programs and partnerships.
The second action, and perhaps the one that had the greatest impact, was China’s implementation of its Blue Sky program that set strict regulations about the scrap material imported into the country. Over the last decade, China has accepted a wide variety of wastes from many countries in the world – including the United States, Canada and Europe – for recycling. It only was able to use a small fraction of the material received, and the rest was either landfilled or left to accumulate. To combat the overwhelming amount of waste that could not be recycled, China outright prohibited certain materials from being imported, and for those they were willing to accept, it set an extremely low contamination rate of 0.5%. The targeted materials for ban included plastics, scrap paper, certain metals and textile materials. China continued to set bans around additional materials and may completely ban all materials.
This positive leap for China to achieve its national environmental health goals has caused major repercussions for the rest of the world. The ramifications for the US have been particularly impactful as approximately 40% of the total materials collected for recycling were being exported to China. While other countries such as Indonesia, Vietnam and Korea are willing to take some wastes, the amount they can process is not large enough to absorb what China was accepting. These countries, along with other Asian countries such as Malaysia and the Philippines, have been closing their doors to these waste products.
Push for a circular economy
The actions taken by China and other countries highlighted the limitations of the linear economy. The linear economy is characterized by the take-make-dispose approach to producing products and services. This approach tends to consume finite resources to produce products which end up in landfills or incinerators. The launching of a new model was seen – the circular economy.
The circular approach, as envisioned by the Ellen Macarthur Foundation, entails gradually decoupling economic activity from the consumption of finite resources and designing waste out of the system. The circular economy incorporates renewable energy and is based on three principles: designing out waste and pollution, keeping products and materials in use, and regenerating natural systems.
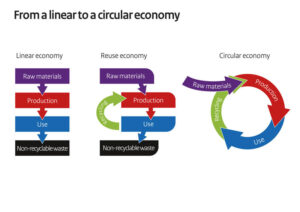
The illustration in Figure 1 offers a clear illustration of the differences in material flows between linear, reuse and circular economic models.
Achieving a circular economy is not an easy path to take as it is difficult to fully eliminate waste. Some products, such as those made from renewable resources, readily are adapted to the circular economy model while others are more challenging. There are many practical barriers to establishing a closed-loop economy. However, changes toward closed-loop or circular economy operations are achievable within specific sectors, companies or product categories.
One business strategy for closing the production-use-disposal scenario includes shifting from selling products that the consumer owns and eventually disposes of to providing a service with an agreement in which the products remain the responsibility of the manufacturer to repair, replace, refurbish or repurpose. This shift in ownership incentivizes the manufacturer to design for less waste, produce a more durable product and create loyalty with their customers.
For example, a recent assessment by Ricoh concluded that by 2050 there will be an insufficient supply of many virgin materials at a reasonable cost to support its manufacturing needs. As a result, Ricoh has revised its business model using life-cycle analysis as the basis for decision-making and establishing a series of “Resource Smart Solutions” for product design and manufacturing, re-use, collection, maintenance and materials recovery. Since the company owns 60% of what it sells, it can engage its customers in new business solutions derived from a circular economy approach.
Government action
Many argue that government intervention is needed to both encourage and instill a more sustainable environment. Several approaches have been proposed, using the circular economy model, to address reaching this goal. Approaches under consideration involve the imposition of mandates to use a specified amount of recycled materials in products, banning the use of certain products and implementation of Extended Producer Responsibility (EPR) programs. EPR programs are designed to shift the waste management cost or physical collection partially or fully from local governments to producers.
EPR as a concept is not new in the US, with almost every state having some type of producer responsibility laws covering consumer products such as automobile batteries, electronics, mobile phones, paint, pesticide containers, carpet, thermostats and pharmaceuticals. Several states have enacted landfill bans which have had an increasing positive impact on product recycling.
Packaging and paper have not escaped the grasp of EPR. Many provinces in Canada and many countries in the European Union have had EPR programs extending to packaging or printed paper for many years. So far, none have been enacted by a state or local government. However, that may soon change with the states of Maine, Massachusetts, New York, Oregon and California.
Maine’s legislation has come the closest to being enacted. It was debated in this year’s legislative session, but failed to pass. Maine’s legislation would see producers with more than $1 million in annual gross revenue paying into a managed fund, with participating municipalities then eligible to be reimbursed for recycling and disposal costs. The costs imposed would be done on a sliding scale of how “readily recyclable” a material is and those that are difficult to recycle would be charged a higher fee. Unless there is a special session called, it will not be considered again until next year.
While there has been activity, virtually all government legislative and regulatory activity has occurred at the state and local level. The combination of the National Geographic focus on plastics, including ocean plastics, and China’s Blue Sky program and its ramifications spurred many state and local government entities to ban the use of certain types of plastic-based products.
Many states have implemented bans on plastic bags, plastic straws, polystyrene food containers and other single-use plastic products. Likewise, some corporations have initiated their own programs. A good example is several large hotel brands are eliminating the use of individually packed toiletries such as shampoo, conditioner, etc. in guest rooms.
Some states have taken the approach of focusing on setting requirements for certain types of packaging. For example, California has established, through legislative action, a program that sets requirements for state-controlled food service packaging. This new program requires state-owned food service facilities, those operating on state-owned properties or those under contract to a state agency to dispense prepared food using food service packaging that is reusable, recyclable or compostable.
Marketplace responses
There are bright spots. Emerging trends around both the use and manufacturing of alternative substrates that are easier to recycle is on the rise. While there is a movement to increase infrastructure recycling using existing technology and new technologies such as chemical recycling, it will be some time before it comes online and sufficient capacity exists to relieve the downward pressure.
Some brands are shifting away from plastic to paper-based products. Several examples include using paper-based material to replace six-pack rings or the recent announcement by Procter & Gamble Beauty that it will start offering both Old Spice and Secret brand deodorants in all-paper, plastic-free, tube packaging. There is no mention if the paper tube is recyclable.
For textiles, there is movement to use cellulosic fibers, recycled poly, organic cotton and Better Cotton Initiative (BCI) cotton, which is a cotton sustainability program. For labels that are being used on PET-based containers, there is a move to use labels that are compatible with the recycling process and for other plastics, work is being done on polymers that are more compatible to both mechanical and chemical recycling.
It also is important to understand that, in addition to new substrates and recycling technologies, there are companies exploring reductions in packaging and package-free options. Lightweighting a package is not necessarily new, along with concentrating certain products to reduce package size. The new options being explored involve selling a single product where the package can be reused multiple times with the subsequent purchasing of super concentrated product that is reconstituted by the consumer.
A corollary to this approach is refillable packaging, where the consumer returns to the store to refill their individual container from bulk dispensing units. Package-free options already are being explored by smaller grocery stores where products are not sold prepackaged.
How this impacts the printing industry
For those facilities involved in packaging and labels, the sustainability and circular economy movement is real. Companies such as Wal-Mart, Target and Unilever have adopted sustainability goals related to the reduction of packaging materials. While attention has been focused on the use of plastics and packaging, increasing attention has been turning to the fashion industry. The drum beat to reduce the impact of “fast fashion” is increasing and getting louder every day. The effect is hitting both the products being produced for customers and the manufacturing operations.
The pressure on brands to address the waste associated with their products has been growing and will only continue to increase. A second, and possibly most important, impact of China’s Blue Sky program is felt around the country as municipalities have stopped or suspended local recycling programs.
With China no longer accepting most of the US-generated recycling, the market has disappeared. With the approaches that many brands and other companies are taking to address these issues, those that are producing products, packaging, labels and other supporting material need to understand they could have their businesses severely interrupted and threatened. Imagine the impact if someone’s primary business was producing packaging or labels and the company’s number one customer decided to offer its products as package free.
With the focus on textiles, packaging and paper waste increasing, printing operations need to become engaged on several fronts. They need to become educated about the changes occurring with respect to new substrates, advances in recycling technologies and recycling services, such as those offered by TerraCycle. This education provides the ability to offer solutions when requested by the customer.
Establish a dialog with customers to educate them about the current and future changes being driven by pressure from consumers, consumer groups, environmental organizations and government regulation. Given the economic pressures being applied to local municipal recycling programs, it is almost certain that there will be additional government regulation imposed on those that produce products, even if they are currently readily recyclable.
The benefit of having this type of dialogue is it allows the printing operation to gauge the understanding and options being considered by the customer. Customers are not monolithic. Some are proactive, while others will wait until circumstances dictate action on their part. If some of the ERP laws come to fruition, understanding the impact of various substrates and alternative options that are more readily recyclable would enable customers to pay less of a fee due to their ability to be recycled.
The education about the changing landscape also allows printing operations to understand the possible changes occurring and potential shifts by their customers to new substrates or the abandonment of current substrates. There are a host of issues that need to be considered, including performance, cost, printability, waste, etc. Understanding how to work with these new or “new to you” substrates will allow for a competitive advantage and allow for a fast response to changes in demands from customers.
Conclusion
The building of a circular economy is not going to be easy. There are many considerations that need to be evaluated as the linear model and the mindset associated with it will be difficult to transform. Nevertheless, the physical realities of the linear model have reached a tipping point as the world has quite simply run out of places to put the waste generated by modern society. Landfilling waste is not a solution as it is just long-term storage and more eloquent solutions are mandatory.
The path forward for many products is not clear. The key to expanding the circular economy is the engagement of consumers, business, academia and government to provide the demand and proper incentives to find solutions. With government now adopting circular economy legislation, more consumers demanding solutions and some brands adopting circular approaches across their value chain in order to mitigate reputational, supply chain, financial, environmental and regulatory risk, printing operations will need to adopt new business models that align with an emerging reality that discourages waste and encourages resource efficiency with design and innovation. This means they need to become more cost efficient, incorporate renewable technologies and resources, partner with like-minded suppliers and engage with emerging approaches to remain relevant and competitive.
Gary Jones is SGIA’s director of environmental, health and safety (EHS) affairs. His primary responsibility is to monitor and analyze EHS regulatory activities at all domestic and some international government levels. He provides representation on behalf of the printing and specialty graphic imaging industry. For more info, visit www.sgia.org.