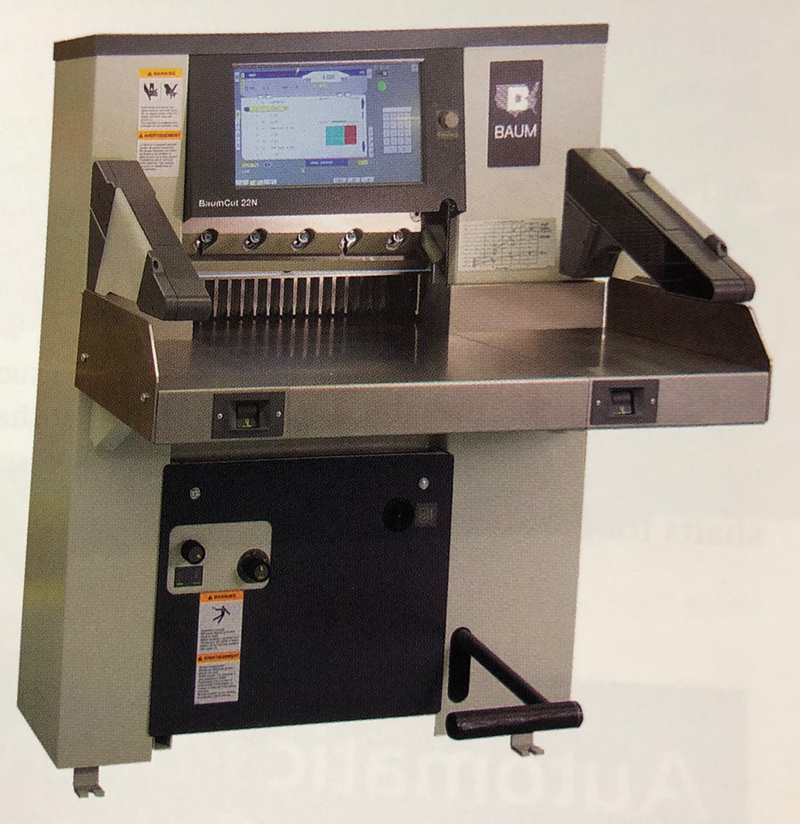
by: Staff
As binderies look more and more toward automation as a cost-saving measure, new technologies are being developed to meet this need. Job Definition Format (JDF), an XML-based file format that serves as a single source of real-time job data, is one such advancement. While JDF doesn’t mandate a given workflow, its flexibility allows a printer of any size to work with vendors to design a workflow appropriate for its needs.
The first version of JDF that could be implemented by vendors was released by the International Cooperation for the Integration of Processes in Prepress, Press and Postpress Organization or “CIP4” a little over a decade ago and the first JDF-enabled products hit the market at drupa 2004. A case study conducted at GRAPH EXPO 2008 showcased the first-ever successful end-to-end live JDF workflow collaboration between multiple vendors. Since then, manufacturers have been offering the technology, but have yet to release a full implementation in the marketplace, said Mark Pellman, director of sales and marketing for the Baumfolder Corporation, Sidney, OH.
He said the use of JDF technology really depends on the size of the operation. “We see only a few smaller operations utilizing the benefits, and some larger binderies do, but implemetation has been limited.”
Pellman offered his take on the latest technology to hit the folding industry and what to expect in the coming years.
What other advances have been introduced to the folding industry?
We are seeing customers using folding machines to produce more specialized folded products, including heavier stocks with multiple panels that traditionally have been limited to a simpler knife folder. The adaptation of various glue systems and attachments helps create attractive folded products that add value to direct mail, special promotion pieces, etc. Gluing systems have advanced to the level that they can add special cards and other items on a folding machine with great accuracy and verify that the glue line was placed for each piece.
Have digital printing and shorter runs necessitated changes in folding equipment?
Many manufacturers saw this change coming years ago and have adapted product lines to meet these needs. One recent change is the ability of a single digital print engine to produce a 14×25.5″ sheet for short runs, and the equipment manufacturers have responded by introducing folders with the capability to feed and fold this size of sheet for the short-run markets. It’s also important to be sure folding roller and fold plate technology are prepared to prevent marking in a digital environment and reduce static.
One way BAUM has adapted to the need to reduce static is with new urethane coatings on suction wheels and the use of state-of-the-art coatings on the feed tables and platforms to reduce static build-up.
Folder technology has kept up, but what about feeders and joggers?
New feeding technologies had to be developed as well to include sheet staging capabilities and utilization of PLC controls to adapt to more inline applications. Feeders have had to adapt to do more than just feed paper to folding machines. New feeder solutions are available for feeding inkjet bases, diecutters, UV coaters, print engines, packaging lines and more.
Do you foresee a point in which folding machinery will require zero human intervention?
We would love to have this, but the marketplace will probably not want to pay for the price of a machine with this level of automation. Manufacturers are producing folding machines with less setup and operation, but the variations in printing/imaging, grain direction, stock weights and other factors still create the need for human intervention. Another key area is the setup of perforating, scoring and slitting. Even though many manufacturers offer automation and “information” on their folding machines, a high skill level is required to set up the slitter shafts for a successful job run. One solution is to provide cartridge slitter shafts that can be easily removed and replaced with another set of pre-set shafts for the next job.
What’s next? Where do you see the folding industry in the next 10 years?
We see more inline and near-line folding applications being utilized. We also see our customers wanting to use the folding machine for more than just folding. A folder can be utilized more as a feeder and scoring/creasing/perforating machine while being run inline with other equipment. The increase in personalization of printed/imaged products also will require the folding machines to adapt to more sophisticated monitoring devices to insure the folded piece is accurate for each recipient.
It also will be important to review and adapt to the needs of customers that have multiple printing and imaging technologies from various manufacturers. There will be a need to continue to simplify the setup and operation of folding equipment to adapt to a newer workforce that is more digital in nature and companies that strive to compete by lowering their costs with easier-to-operate equipment.