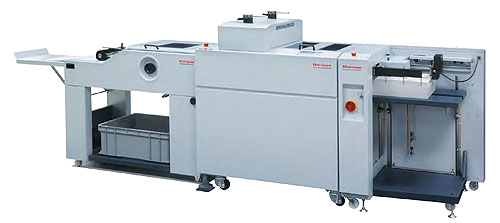
by Brittany Willes, PostPress

Standard Finishing Systems, a leading North American distributor of digital duplicating and document finishing products in Andover, Massachusetts, recently has unveiled the Horizon RD-4055 rotary diecutter. Developed in direct response to the rising demand for short-run diecut products, the RD-4055 boasts of simple operation and easy changeover with an intuitive touchscreen that displays easy to understand graphical illustrations for set-up and control.
Neal Swanson, director of marketing communications for Standard, stated the new system, “is a finishing solution that delivers consistent quality from one end of the run to the other.” The RD-4055 is able to diecut, crease, perforate, slit, hole punch and round corner in a single process for digital and offset printed sheets. The vacuum belt feeder allows for superior feeding while the ultrasonic sensor enables double-feed detection on a wide range of substrates. Additionally, a servo motor-controlled “Repeat Register” allows for multiple-up applications from a single die. The only diecutter with this capability, the RD-4055’s register function allows for significantly reduced die cost.
Able to perform simultaneous die- and kisscutting, the RD-4055 can create stickers and labels. Furthermore, the crease function helps prevent image cracking, making it appropriate for boxes, pocket folders and greeting cards that require additional folding after diecutting. According to Swanson, customers have responded positively to the new system. “They are happy with the trouble-free operation of the unit, the wide variety of applications and the very short learning curve,” he said. “They are reporting faster changeover times and greater than anticipated productivity.”
Even small diecuts are “neatly executed; the final result is nothing less than amazing,” remarked Swanson. “I’ve never seen another diecutter finish as many pieces in so short a time. Watching the RD-4055 go through a stack of digitally printed material, while accurately diecutting each unique shape, is eye-opening. The finished pieces seem to roll off the delivery tray in a steady stream.”
The RD-4055 recently was selected as a Must See ‘Ems award winner at the 2014 GRAPH EXPO in Chicago. Chosen by a panel of industry experts, the Must See ‘Ems award acknowledge the most compelling technological advances spanning the entire graphic communications industry.
Technical Details
Feeding, diecutting and separating are achieved in one pass with a speed of 6,000 cycles per hour, making the RD-4055 the fastest in its class. The new system is capable of processing normal paper, coated paper and cardboard. For diecutting, it can handle materials 0.5mm/0.019″. Maximum material thickness for creasing is 0.4 mm/0.015″. The system has single-phase voltage/frequency of 200 to 240v, 50/60hz.
A uniquely designed diecutting section enables quick and easy diesetting. Flexible die plates can be used in thicknesses of either 0.6mm and 0.8 mm/0.0236″ or 0.0315″. Rigid magnetic upper roller and solid lower anvil rollers ensure high-quality diecutting.
Vacuum belt feeding allows for feeding with easy setup and operation. An ultrasonic sensor is used for double feed detection on a wide range of substrates. The RD-4055 is designed to handle sheet sizes ranging from 200x275mm/7.88×10.83″ to 400x550mm/15.74×21.65″ before processing. An optional separator removes the waste from the finished product and delivers it to the waste bin. Finally, a delivery section, supplied with the separator, delivers finished products on a motorized conveyor.