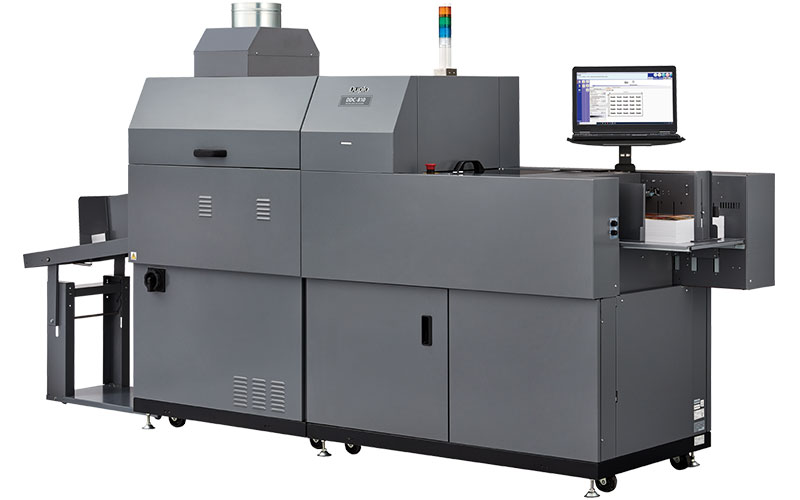
By Lara Copeland, writer, PostPress
With intentions to fill a void in the market, Duplo USA Corporation, a Santa Ana, California, provider of innovative print finishing solutions to the graphic arts industry, introduced its DDC-810 Raised Spot UV Coater back in 2017.
“The available technologies at the time were expensive,” said Duplo Product Manager Anthony Gandara, “and many printers and brand owners liked what these technologies could do but could not afford to invest in them.” He said they also did not know how to justify purchasing the technology since they did not have any immediate need or demand for this type of embellishment work. “But they could see the benefit and value that this type of technology could provide,” he added.
Printers searching for quick, easy and affordable technology to enhance the value of their printed products will find value in the DDC-810. Using Duplo’s technology allows printers to turn their, “plain CMYK prints into an experience that their customers can actually touch and feel,” said Gandara. Printers have used this added value to differentiate themselves from competition, and he said they have been able to sell their printed products for much higher premiums, which in turn, has helped them to generate profit on jobs that they normally would not.
Offering superior accuracy and producing high-quality raised spot UV embellishments, the DDC-810 is easy to use – only requiring the printed sheets with registration marks, a PDF of the spot layer and an operator. “The DDC-810 is the ideal solution for customers who want to increase the value and profit of their printed products,” Gandara said.
Together, the DDC-810 and the EFI Jobflow simplify and streamline the file preparation and submission to the printer and DDC-810. “With just one click of the mouse,” Gandara explained, “Jobflow will impose the job, apply the registration marks for the DDC-810 and add barcode or QR codes for the DDC-810 and Duplo slitter/cutter/creaser to enable automatic job set-up of variable image and job processing.”
Gandara said that the response to the technology has been great. In the last two years, Duplo USA has hosted the Shima Awards, a contest that recognizes a Duplo customer for its creativity and uses of embellishment. “We have seen so many great examples of applications and jobs that our customers have produced; their creativity is simply amazing,” he added.
According to Gandara, “The DDC-810 is compact and extremely easy to use; plus, it can be installed and begin running jobs in one day.”
Technical details
The DDC-810 is a completely digital process, only requiring the printed sheets and a PDF or TIF of the spot layer. The printed sheets are loaded into the feeder. The maximum loading capacity is 5.9″ and the maximum sheet size is 14.33 x 29.13″. It supports a wide range of coated papers, substrates, laminates, toner and offset printed output.
As the sheets are fed, they are side registered and pass through the dust roller to remove any dust from the surface of the paper or substrate. Two CCD cameras read the registration marks that are printed on the sheets. The 600 x 600 dpi inkjet heads precisely and accurately apply the spot UV layer onto the printed sheets. Up to seven different thicknesses can be applied in a single pass. The polymer is instantly cured as the sheets pass under the UV lamp.