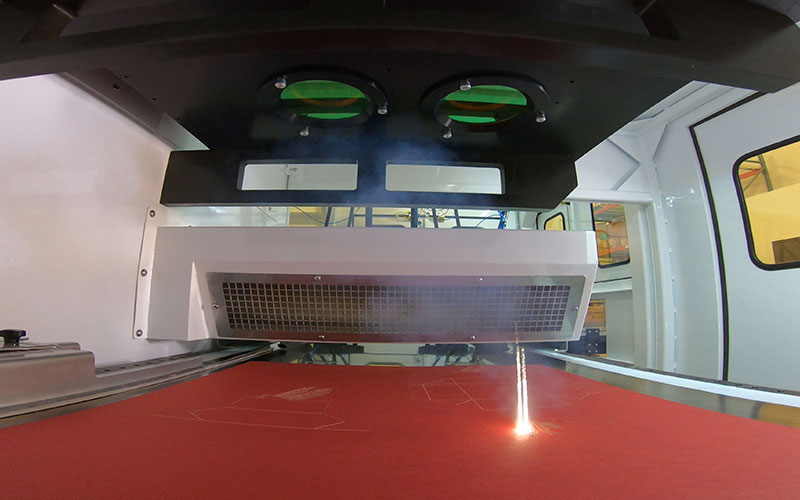
PostPress
Laser cutting is making its mark as both a decorative and functional technology for the graphic arts industry. It is used to create detailed decorative designs on greeting cards and invitations and also is used to cut short- to medium-run folding cartons, where cartons can be cut and scored inline without the use of any type of tooling or dies.
PostPress talked with Michael Aumann, senior vice president with LasX Industries, to provide further details on laser cutting technologies today and their applications.
What advantages does a laser cutting system provide?
Laser cutting systems provide many advantages, including the elimination of costly mechanical dies and expensive setup times. Laser cutting expands design and functional features with the capacity to create intricate patterns, shapes and etched images that are not achievable with traditional mechanical cutting techniques. Short runs can be produced efficiently and economically due to digital file management and the elimination of costly tooling and makeready. The precise X/Y registration is ideal for digital print which “floats” on the material. This minimizes waste at changeover and provides a higher degree of accuracy than traditional diecutting, which only can adjust in the X direction
(down web).
What is the difference between fixed-beam and steered-beam galvo systems?
An X/Y fixed-beam system delivers the laser beam straight down and requires moving the mass of the fixed-beam head and optics above the material. A galvo system delivers the laser beam to the material by sitting above the material and steering two mirrors. The mirrors are lightweight with much less mass than the fixed-beam system. This allows the laser beam to travel faster and allows laser cutting while the material is moving. This results in a much higher throughput than a fixed-beam system.
Furthermore, the galvo system is ideal for processing thinner materials, which will have an angled beam delivery at the edges. The fixed-beam is better for cutting thicker materials since it is cutting straight down and will have no bevel.
What paper stocks work best with a laser system? Are there limitations with paper stock weight?
The laser can process a range from lightweight paper to heavyweight paperboard. The thicker the material, the slower the laser process is to cut. Not all paper and paperboard are created equal. The paper pulping process varies, and some lasers cut cleaner than others.
For example, chlorine can be heavily used in the pulp so when the laser interacts with the material, it can create a more yellow edge than others. So, it always is suggested to test the material to see if it is clean. Just as printers have better-performing papers, the same exists for laser-process papers. Some paper vendors have developed specific papers that perform well under the laser.
Are plastics or vinyls appropriate materials for laser cutting?
Polyester, polypropylene and BOPP are great with the proper laser. Vinyl is not laser friendly. Laser processing vinyl will yellow the edge badly and produce an off-gassing that essentially creates a HCL acid gas – not good for the operator, the exhaust equipment or the environment.
How can a laser system help to streamline operations and reduce waste in a facility?
Systems equipped with digital workflow features support instant order change and network connectivity and will support multiple file types. They can eliminate mechanical die setup and teardowns. Systems equipped with vision allow for automated cut-to-print registration, and integrated robotic handling can eliminate waste stripping and automate stacking and batching.
What file types work with a laser cutter?
Entry-level systems may require proprietary file structure. Sophisticated systems are capable of using vector files – such as PDF, DXF and DWG – as well as image files for rastering and etching – such as JPG, BMP, PNG and TIFF files.
What features are a “must” for processing digitally printed materials?
Camera registration: If processing digital print, operators must have a system that uses a camera register to print fiducials. This allows the laser to adjust both in the X and Y directions to compensate for the print floating on the material. Otherwise, the operator will have to monitor the registration all through the run, which will result in higher waste quantities.
Support for PDF file processing: This format already is established as the standard for most art departments within print companies.
Instant order change: Instantly change from one job to the next with little to no waste. Eliminating the setup time of a job yields more throughput within an eight-hour shift. This allows for a much lower minimum order quantity and still maintains an adequate profit margin on the job.
Expandiblity: This provides the ability to add a laser in the future to increase throughput as the business grows.
Automated file workflow: The ability to automate the file preparation from the art department for the laser systems can free a skilled operator for other tasks. Files should be automatically prepared and leverage a barcode to instantly load and run on the machine.
How does the laser register the cut to the sheet?
There are three methods for registering a sheet. Traditionally, a sensor can provide lead edge detection and registers to the lead edge or to a print mark. The downside of this is that it only allows registration in the single direction. In applications of diecutting blanks, this is appropriate.
However, if registration to print is required, there are two methods which lead to different degrees of accuracy. If a single camera is implemented, then one can register to a corner of the material or to printed fiducials on the material and adjust both directions (direction of movement X and cross direction Y). A single camera can work for both sheets and a web.
The use of two cameras across the lead edge of a sheet or web allows for not only X and Y compensation but can compensate for skew of the sheet or the printed web, bringing an even higher degree of accuracy. This eliminates the need for upstream material handling to perfectly place and square the sheet. The laser can compensate for a slightly skewed sheet or print.
Are laser systems available to produce both decorative and production work?
For some companies, decorative work is their production. A laser does not need to be dedicated only to decorative work. The same laser cutter can work for more functional production work as well. Throughput of a laser is directly related to two variables: thickness of the substrate and amount of dieline. The thicker the substrate, the slower the laser must travel. The more complicated the dieline, then the slower the process.
Many people concentrate on rate (sheets/hour or feet/minute) of a process, but with the proper laser system the objective should be about throughput – the drive to maximize uptime, reduce set-up time and minimize waste when comparing the traditional process to a digital process. Sometimes the impact of a digital process is seen in how something is done two or three steps downstream.
A laser cutting system can be part of a digital finishing system that cuts, removes the part from the material, stacks, counts and delivers for the next process downstream. With an instant order change, operators can digitally print sheets in any order and quantity, and the finishing system can complement this.
Because of the digital nature of the laser, it allows automation at an entirely new level. The traditional diecutting process favors high quantities and long runs. This is directly related to the cost of the tooling and the setup time invested in the job. The digital process breaks the setup time barrier and allows a plant to run the quantity needed, reducing the warehouse inventory space required in traditional methods.
LasX develops and markets intelligent laser processing and cutting solutions for manufacturing innovations. In addition, it also provides contract manufacturing services for flexible packaging, medical and digital finishing applications. For more information on its line of laser cutting equipment and services, visit www.LasX.com.