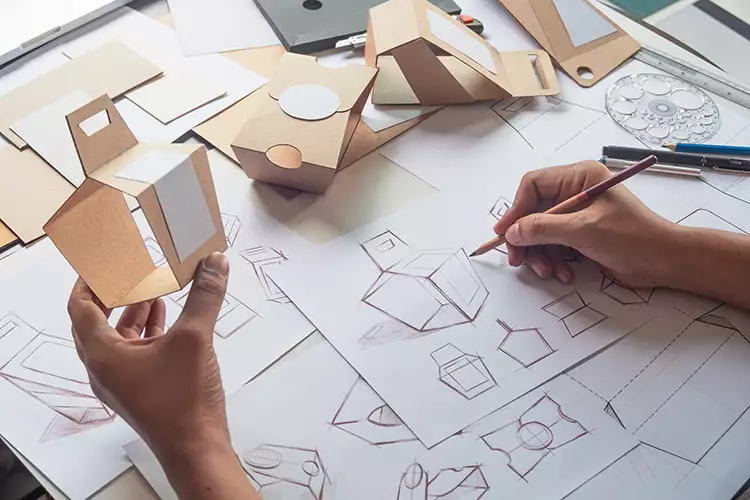
By Stefan Badertscher, director of sales and marketing, IMPACK
Below are the seven most effective ways to maximize your folder-gluer’s productivity without holding anything back. Learn about what steps you should take, how to implement those steps and in what order.
Add an accumulation conveyor after your folder-gluer’s compression belt.
If you already have an accumulation conveyor after your folder-gluer, you can skip this step.
Adding an accumulation conveyor will allow your packing personnel the ability to accumulate more boxes per meter of conveyor, hence the name “accumulation conveyor.” This reduces the speed of your box shingle and allows more boxes within the same time frame. As a result, your packing personnel will have more time and peace of mind, which will lead to a naturally quicker packing process.
This contrasts with having your personnel pack directly from the folder-gluer’s compression belt, where there is no buffer if some boxes need to be checked or adjusted, or if some boxes slip out of their hands.
What I have seen very commonly among clients who do not have an accumulation conveyor is that their packing personnel will attempt to build their own buffer by emptying the compression belt as fast as they can. This leads to a very non-ergonomic workstation.
The accumulation conveyor allows your packing personnel to have more boxes per meter of conveyor, thus giving them a more relaxed work experience and the ability to easily resolve any issues with the cartons if, and when, they happen.
Upgrade basic tables to actual tilting tables.
If you have actual tilting tables, you can skip this step.
What is the difference between basic tables and actual tilting tables? Basic tables are tables locally made from wood or stainless steel that are used to hold the cases which are to be packed with the boxes. Very often, clients will couple those basic tables with a “tilting holder/stand” which is
used to tilt the cases to prevent the boxes from falling when placed into the case. Put simply, basic tables are fixed tilt stations.
Fixed tilt stations require the packing personnel to push the cases upwards onto a conveyor when they’re done packing the case. This represents a pushing movement of 6 to 12 kg each time a case is ejected. On top of that, and depending on the material of the case, the friction makes the filled case even heavier.
Actual tilting tables, on the other hand, are tables made of a metal frame where the case is placed on a section of free-movable parts, such as “gravity conveyor rollers.” The frame holding the case is fixed on both sides at one specific point to allow the table to pivot when the case is moved. These eliminate the friction between the case and the surface on which it is moving by using modern technologies, making the force needed to eject the case almost zero.
Once the cases have been packed, personnel close the flaps of each case and then push the case forward. Subsequently, the case gets ejected onto a conveyor or directly into the case sealer machine.
Benefits of an actual tilting table are as follows:
- It is less strenuous on the packing personnel.
- The table requires less manual workload.
- It is faster, making a difference over time.
Add a box turner.
Another step forward would be to add a box-turning feature.
The purpose of having a box-turning feature is to rotate your boxes 90° to the left or 90° to the right and control your box orientation to meet the requested case packing configuration. If not turned, your boxes would come out standing up, which would require your packing personnel to manually turn them 90° and place them into the case.
What a box turner really does is orient the boxes in a better way for the packing personnel to facilitate the packing. This is because standard straight-line boxes typically are packed with the glue flap lying horizontally when placed into the case.
The box turner automatically facilitates this arrangement so that your packing personnel do not have to manually turn the boxes before packing them into the case. This allows for:
- Avoidance of repetitive movements that lead to constant wrist injuries;
- Simplification of the grabbing movement; and
- Time savings during the packing process.
The implementation of the previous three tips creates the most common packing help machine on the market: a collecting table. Most collecting tables are nothing more than an accumulation conveyor combined with a tilting table and a box turner.
Integrate a case sealer.
Next, integrate a case sealing machine to automate the case taping after you have manually ejected your cases. During visits to clients, this is the one tip that always takes them by surprise.
With some easy calculations, clients quickly realize how much time (and money) they have been spending on packing personnel labor for simply taping cases. Instead of using a hand taper, as you would traditionally do, a case sealer machine allows you to fully automate the taping process so that your packing personnel do not have to manually tape any cases.
Simply push the case through the case sealing machine and the case will come out automatically taped or sealed. Taking it a step further, it even can pack cases without taping the bottom of the case. The case sealer will tape the top and bottom of the case, at once, fully automatically. This investment can save approximately three to six seconds per case.
Ensure that glued boxes do not need 100% inspection.
Equip the folder-gluer with a glue inspection system and a box ejection device. This is to make sure that the boxes coming out of the folder-gluer compression belt are well-glued, even when your folder-gluer is running at higher speeds. It is, by far, the most important step you should apply if you’re searching for ways to speed up your packing process.
Potential clients repeatedly state, “We need our personnel to inspect 100% of our boxes.” If this rings true and there is no way of sampling some boxes for inspection or having the client accept some percentage of minor imperfections, then there is no room to improve a folder-gluer’s productivity.
However, an inspection system that checks boxes during the gluing process can increase the confidence in the whole process by controlling the quality of the boxes that are being packed into cases.
The article “Quality Control Systems Key to Folder-Gluer Production Success” from PostPress magazine covers the importance of glue inspection and box ejection systems, the features and benefits they provide and things to look out for when considering those quality control systems.
Though there is no guarantee for each box to be 100% perfect, these tips can help provide confidence in producing client-approved box quality, at a percentage level that your client has agreed to.
I always tell clients to take a speed test before considering a folder-gluer packer.
If the gluer cannot go faster with more than one or two packing persons because it will lead to quality problems, this means there is one (or more) of the following problems:
- Boxes cannot be glued faster without damaging them.
- A new folder-gluer potentially could glue faster, but this needs to be analyzed in detail.
- The boxes are well folded and glued, but the glue is not sticking as it should.
- Many clients change the type of glue they use to one that offers a quicker and stronger bonding once they start running faster.
- The boxes are well folded, but there is not enough glue or the glue is completely missing.
This issue can be solved with an upgraded gluing and glue inspection system. This will make sure that boxes are well-glued even when your folder-gluer is running at higher speeds.
The folding and gluing process is the core component of production. In other words, mastering the folding/gluing process should be a primary concern when thinking of automating an end-of-line process. The process of tuning a folder-gluer is more akin to craftsmanship than automation. Increasing the output of a gluer is never as easy as cranking up the speed dial of the gluer.
For example, when setting a complex box on the folder-gluer, it would take time to tune the gluer until it’s reached a good production and consistency level. The issue, though, is that when tuning the gluer, either by setting a new box or making adjustments to increase the speed, it is inevitably throwing garbage out.
The more a client moves toward automation, the more folder-gluer inconsistencies will have to be considered in the packing process. Why? If badly glued or damaged boxes are sent to the carton packer, they either will be packed and sent to the client without knowing it, or, in a more automated machine, it may create a box jam and cause a complete stop in the production line.
Incorporate pneumatic tilting tables.
Finally, incorporate pneumatic tilting tables that push cases into the case sealing machine with the press of a button or a push on a peddle.
This step would save additional time, and money, over what can be saved with the implementation of Tip #4.
Explore options of folder-gluer packaging equipment.
Once all the previous six tips have been applied, it is time to start exploring the world of folder-gluer packaging equipment and peripherals. This includes semi-automatic, automatic and fully-automatic folder-gluer packers, stackers and pre-feeders, as well as peripherals such as box turners, batch inverters, counting and separating devices, and custom solutions that are built to meet the unique and specific needs of production.
The main takeaway is that in order to realize Tip #7, Tip #5 must have been implemented carefully to master the folding/gluing process. In other words, be 100% confident that the cartons are coming out well-glued.
Once you are confident about your folding/gluing process, and you know that you either can increase your folder-gluer’s output whilst maintaining your quality or maintain your folder-gluer’s output but with fewer packing personnel, then you can begin considering folder-gluer packaging equipment and peripherals. But, knowing that you need to invest in carton packaging equipment is not “the” ultimate answer to push your folder-gluer to its full potential.
Conclusion
There are fundamental steps to take before considering packaging equipment to become the top-speed producer in your industry. The implementation of these top seven folder-gluer productivity tips creates the best position to add packaging equipment to the folding-gluing process, and, more importantly, get the highest payback off of investments in packaging equipment and peripherals.
The real tipping point between deciding whether to add a folder-gluer packer or not is the setup time. If a gluer is far from reaching its maximum speed, but two packing persons are struggling to keep up, explore the different types of folder-gluer packaging equipment and how they can help unleash a folder-gluer’s full potential.
Stefan Badertscher is the director of sales and marketing at IMPACK Packaging where he has been leading the development of an international sales network and introduction of an inbound marketing strategy. IMPACK specializes in analyzing work methods and designing equipment for manufacturers of carton board and corrugated board packaging. For more information, visit www.impack.ca.