
Edited by Erin La Row, editor, PostPress
Digital embellishments can take a project to a new level – enhancing the look and feel of a product and propelling its brand recognition. But even the best-laid plans can experience hiccups along the way. Selecting the correct paper stock and lamination (if applicable) are keys to a successful job when working with digital inkjet spot coatings and/or digital foiling.
Kevin Abergel, president of Taktiful, sat down with two experts on selecting paper stocks and working through lamination challenges with digital embellishment: Ken Huizenga and Matt Redbear.
When it comes to digital embellishment specifically, what kind of limitations are you seeing when it comes to the type of paper stocks you can and can’t use? And which ones do you recommend for the best possible results?
Redbear: I divide it up into three different categories. There are paper stocks that absolutely work, there are stocks that absolutely do not work, and then there are the ones that can be made to work – they have special situations, special production requirements. Obviously, what’s going to work best is a smooth, coated stock. It’s going to give even results if you want a mirror finish. And I want to clarify, too, that what we’re mostly talking about here is polymer varnish overlays. We can move on to talk about other digital development embellishment methods, but when it comes to laying down inkjet varnish, the smoother the stock, the smoother your results.
There are certain types of offset stocks that I have had good success with, including Royal Sundance Felt – which you would think would never work with the polymer overlay. Cougar® Digital will work as well if the operator is applying the varnish in small areas. If the spot varnish image is large, you’re going to run into problems.
I have used an offset parchment and offset laid paper, which aren’t supposed to work and have had success. There are others that simply cannot work – anything that has a heavily embossed or hatched surface will be difficult. They do make a digital linen, but it will pick up the texture if you’re laying foil on top of that. Any super-porous felt-types of paper or a cork surface simply won’t work with digital embellishments.
When working with uncoated stocks, you must create a barrier somehow, whether it’s through laying down a toner first or a lamination on the sheet. You have an advantage when you’re using a Xerox® iGen® because you have the fuser oil, which creates an additional barrier on top of the toner. You can use a clear or white toner as an underlay as well. Any color of toner can be used as a barrier – the darker the toner, the better coverage you will have. You must have some type of barrier with uncoated stocks – a pre-varnish or lamination works as well.
Huizenga: Much like what Matt said, the smoother the surface, the better. If you’re going to have a stock that isn’t the smoothest sheet, then you may not want to have fine details in the design. However, larger areas or more of a full flood coat can be accomplished with your embellishment press. I tend to prefer, and so do many customers, a dull coated sheet to create the contrast from with spot digital inkjet varnish.
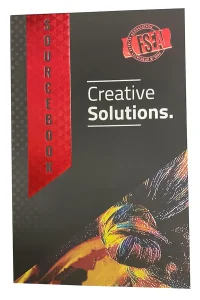
A critical point when working with paper stocks and digital embellishments is to make sure you keep your substrate as flat as possible. I always found when ordering parent-size sheets and cutting them down, it reintroduced a moisture change. It often can curl a stock, which can create challenges with the sheets going under inkjet heads that clear by half a mil. You want to be sure to keep it as flat as possible. Ordering precut stock that’s already been conditioned and has been sitting on your shelf a while will lend itself to a much better embellished product. A lot of the pearl ices and metallic-look papers do work. You just have to take into account both design elements and what the end use is for the product because there’s a lot of concerns: whether or not it’ll crack, whether or not it can stand up to the bindery concerns; as well as just making sure that it’ll stand up to its environment, depending on where it’s going or where the customer is going to send it.
Your dyne level is very important. You’re putting down a liquid that has to distribute itself just right. There are dyne pens to test substrates so you don’t get yourself into a bind before you start. If a customer were to ask you to use a certain type of stock that you’ve never used before, I strongly recommend having dyne pens available because you want to make sure that it is in the perfect printing range to apply the digital spot coating. The range is between 34 dynes (minimum) to 45 or more dynes.
Testing the dyne level of the sheet is going to help with bite (how much adhesion you’re going to get into the paper), but also wettability (how well does the varnish smooth out to get a nice, glossy look). Those are the two things you really want – you want it to adhere and you want it to flow on that sheet as nicely as possible. I remember running into issues for clients from time to time on certain C2S sheets. So basically, the coatings are on both sides of the sheet and, if you built up a big enough stack, some of that issue is the coating would stick to the varnish if it was too hot in the production environment.
Redbear: If you’re printing on both sides, it’s all stock dependent, but the smoother and glossier your stock, the more of a problem you’re going to have. We have built a rack where we can literally stand the sheets up apart from each other when it comes off the stacker. We stand them up rather than lay them down to get the pressure off them. Then they cure for another 24 to 48 hours and that usually overcomes the problem.
Including a soft-touch or matte lamination before a digital inkjet spot varnish or foil is used creates a nice barrier but also great contrast for the finished piece. What suggestions do you have when it comes to using lamination, and what kind of limitations have you experienced?
Huizenga: Laminating the paper stock is a great addition – soft-touch laminates can look fantastic. That contrast I talked about earlier becomes tremendous with a soft-touch laminate. I think for me, the biggest concern is what kind of laminator is being used. You obviously need to consider heat and curl, because as discussed earlier, you can’t get a curly sheet under inkjet heads. Making sure that you get the temperature just right, that your finished product lays flat and that it can go into the machine comfortably are very big concerns.
Redbear: Lamination issues are widespread and either it’s just not a full lamination or you get the ragged edges because the blade didn’t cut it clean – either can create issues with sheets being sensed as a double-fed. As far as appeal and use, people seem to gravitate toward the soft-touch laminates more. You’re adding the reverse tactile effects to the other tactile effect. You’ve got the complete 180 degrees going on. This can create really sexy pieces, particularly with a lot of contrast or very dark colors or just black.
Another concern is it can be too thick for some digital embellishment machines. If laminating an already thick stock, you accidentally may find yourself beyond the machine specs. Another thing is to be mindful of your registration marks. Make sure the glossiness of the laminate doesn’t throw off any registration system you may have on your press, and make sure that if you do laminate, the entire width of the sheet gets laminated. If not, those registration marks can remelt in the laminator, and then ghost across the sheet via the hot laminator rollers, and subsequently throw off your registration system when it comes time to embellish.
The dyne level also is important when it comes to laminate rolls and unfortunately, laminates have a shelf life just like foil has a shelf life. The dyne levels will start dipping after the laminate roll has gone past its prime. Also, when you’re buying your laminate, number one, make sure that you’re getting that sell-by date. And number two, if you’re using something you have in stock, track how long it’s been on the shelf. If it’s been on the shelf for two to three years, you might have flow issues and adhesion issues that are linked to the dyne levels. And, of course, as you mentioned, getting the right laminate to stick to the right ink – some laminates stick better with specific inkjet inks or toners.
Huizenga: I also would like to add one quick thing to consider when you’re using laminate – a lot of people are using single-sheet cutters
for their cutting of the dimensional products. Laminate is pretty much a no-go on most of those machines, so you need to be thinking about diecutting or very carefully guillotine cutting these sheets. It’s an important thing to keep in mind when you’re designing.
This article was derived from a recent video interview with Ken Huizenga and Matt Redbear in a four-part series. Members of the Foil & Specialty Effects Association and the Digital Embellishment Alliance have access to this video series and others. To learn more, visit www.embellishdigital.com.