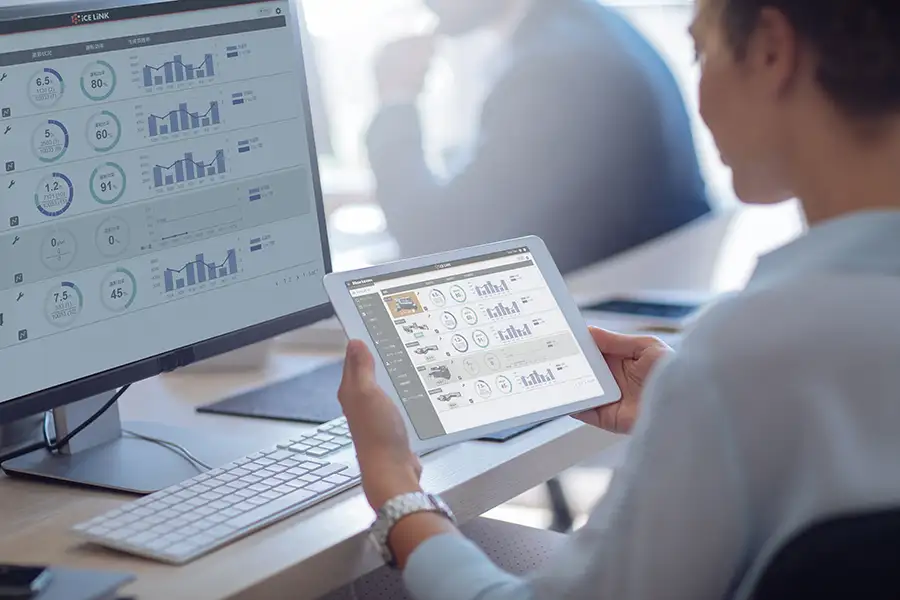
Edited by Erin La Row, editor, PostPress
Investing in workflow management software to connect binding/finishing operations helps streamline specific tasks of the production processes, increasing efficiency and minimizing the chance for costly errors.
PostPress posed questions to these industry experts – Andrew Bailes-Collins, head of product management, Ultimate TechnoGraphics, Inc.; Yashi Potdar, workflow solutions analyst, Standard Finishing Systems; Carlo Ruas, partner, Taktiful Software Solutions; and Mauro Valle, solutions manager, SigmaLine & Connex Workflow, Müller Martini – to gain a better understanding of how workflow management software is helping to improve outcomes from the printing to the finishing/binding environments.
Improving communication
The development of these applications mainly was triggered by the prepress departments that were being modernized and digitized quickly, Ruas explained. Workflow management software could help prevent or avoid errors along the processes, which were mainly caused by human factors. “It is well known that errors in prepress will have a direct impact on subsequent processes, such as printing or finishing, since all three are interrelated,” he said. “It is for this reason that the evolution of these developments has maintained among its principles the automation with which production errors are minimized by seeking to anticipate them.”
Bailes-Collins agreed. “It could be argued that prepress is more important than the actual press in a lot of scenarios. As the prepress department imposes the pages for the press, it’s the information that’s generated by prepress that is used to set up the finishing equipment, including embellishment, and this normally is achieved by JDF [job definition format]communication or by placing barcodes on the printed media.”
The development of new finishing systems is a challenge for workflow software today. These technologies are not yet compatible with XJDF [exchange job definition format, which is a subset of JDF], which keeps them excluded from management software and means the processes involved for the adjustment and set-up of the equipment still are manual and prone to errors. “The challenges that these new finishing technologies pose in terms of their integration into a workflow still are very varied since it is necessary to first document and define the variables of the processes involved so that they can be integrated into the XJDF format,” Potdar said.
Many print providers identify the finishing process as a bottleneck in their operations, especially as job runs get shorter, he added. Finishing equipment often doesn’t run at press speed, and there often are multiple machines that need to be set up to complete the finishing on a job – such as a booklet application requiring cutting, cover sheet insertion, saddlestitching and trimming.
“When the printing environment isn’t communicating with the finishing environment, it places more burden on operators to keep track of which jobs are being processed and when. This introduces inefficiencies in the form of wasted time and human error, especially as experienced operators become scarcer,” Potdar said. “When the press and the finishing are in communication through workflow software, there is less friction in processing applications.”
Valle said with shorter production runs, makeready times become more crucial by passing the information from the digitally printed product to the binding equipment. He added “You drastically reduce the makeready times by eliminating operator input.”
Important considerations
Compatibility is the most important element of workflow software for communicating between the printing and binding/finishing processes, according to Potdar. She said manufacturers incorporate proprietary software within their equipment that can manage the workflow within that specific piece of equipment.
“A press may use one type of software and the finishing equipment may use another. For an end-to-end workflow solution, the workflow software must be able to communicate with all these different machines,” Potdar said. “Luckily, this isn’t as complicated as it once was. Advancements in workflow software have improved compatibility across systems so providers can implement a true end-to-end workflow.”
Another factor that plays a role in why the adoption of finishing automation through workflow management software still is slow compared to the adoption of other technologies is that many print shops still have older finishing equipment that is not compatible with JDF.
“It is no less important to highlight the need to continue with the dissemination and training of XJDF to catalyze its adoption, which will indirectly promote new finishing developments to also include compatibility with the XJDF format in their systems,” Ruas said.
Bailes-Collins believes connectivity and open communication are key considerations. The ability to work with open standards is important, he said, as all of the individual applications in a print production workflow need to communicate with each other using standards such as JDF, XJDF, XML (extensible markup language), JMF (job messaging format) APIs (application programming interface) and JSON (JavaScript object notation). “To be honest, a company doesn’t need to understand these formats as they are under the hood and transparent to the users – they just ‘work,’” He said. “But as they are the building blocks of connected workflow solutions, companies should ensure anything they buy is ‘open’ and they are not locking themselves into a single solution or vendor.”
“So-called ‘islands of automation,’ where solutions provide automation within themselves but cannot openly communicate with other software or hardware in the production environment, are to be avoided,” Bailes-Collins said. “Open end-to-end communication is what the market is demanding. Proprietary systems and formats can create dead ends in modern production. If you are buying a new piece of finishing equipment, ask if it can be connected to your network, if it’s driven externally by JDF or some other method, and about integrations that already exist at customer sites. Prepare for the future.”
Overcoming challenges
Companies get overwhelmed when talking about software tools, Potdar said. “Introducing a new workflow solution into an operation will require training operators and staff, which intimidates many print providers. Also, setting up end-to-end integration is a large, though cost-effective, investment, and it requires buy-in from executives and managers from across an organization to work to its fullest potential,” she added.
Even with improvements in software compatibility, some organizations will still require some manual customization from their software providers to automate all their processes, which can further affect costs.
Ruas explained that equipment manufacturers are free to integrate into their workflow software proprietary data exchange formats for intercommunication of their systems, and it is quite possible that they could deliver some additional features to those that XDJF could naturally deliver. However, he added, this would only be feasible when a printer has decided to work with systems from the same brand/manufacturer.
“The real challenge faced when implementing workflow management software would not directly be related to manufacturers’ proprietary interchange formats,” Ruas said. “An example worth mentioning is the rapid adoption of the PDF format which, since it became available in 1993, has rapidly replaced other formats used in prepress environments and now is accepted as the standard format for sending electronic files for printing. The modernization of the installed plant of prepress devices and their compatibility with the PDF format allowed this file format to be integrated as a technical standard.”
Valle said he has observed that as companies try to move into the digital space, not many people have embraced the JDF standard. “Many customers do not have the required upfront data to push downstream to optimize their production runs. This means that they still are leaving a lot of manual work for operators,” he said.
In some cases, automation can be viewed as a threat if not explained properly. “Any automation project requires a change of mindset,” Bailes-Collins said. “The whole team should feel that they are involved in the project. Automation is a company-wide initiative, so everyone should be included with clear messaging about why it’s happening and what the goals are.”
Recommendations
As companies begin the implementation process, it’s important to set clear goals for the company and include representation from each department on the implementation team. Bailes-Collins advised, “Don’t try to bite off more than you can chew. And don’t overcomplicate things.” Any automation project is best done in small, bite-sized pieces, he said, adding that “Too often the focus is too small and, when you want to achieve end-to-end automation, you can end up having to replace small pieces if you don’t keep the end goal in sight. Automate in step but with a clear end goal in mind.”
Valle said a lot depends on and starts from the customer entry and the file submission that is going to be printed. “It is important to have that data upfront. Knowing how the product will be finished (such as paper type, binding methods, etc.) and having a good management information system (MIS) are crucial to passing all the information downstream to the bindery,” he said. “Having the ability to receive feedback from the printing and post-press equipment also is important.”
Potdar said the most important thing is for companies to look at their entire operation holistically, from intake to shipping, adding, “Many companies try to simply connect existing, separate workflows, and this is where problems can arise. A holistic view of operations not only helps identify inefficiencies and redundancies up front but allows companies to build in capacity and capabilities for the future instead of only working with what already exists in their shop.”
Take a holistic view but then focus on one area, perhaps the biggest bottleneck or the place where the company will get the greatest return on investment. “Do that first and then move on to the next area and so on,” Bailes-Collins said. “Learn as you go. Keep the scope of project tightly focused and don’t fall into the trap of adding and adding functionality. You will never finish your first step if you do that.”
Another tip is to nominate an “automation champion” in the company to drive the project forward and manage it. “Give that person the time to step outside his or her daily work to focus on the project and make it happen,” Bailes-Collins advised.
Whether or not there’s a benefit of having a workflow software platform for separate trade binding/finishing operations depends on the company, according to Potdar, who said print service providers that do high-volume, long-run applications will benefit the most from end-to-end automation and workflow solutions. Smaller print service providers that work on a lot of short-run jobs may find that separate workflow solutions work best for their operations.
“Incorporating workflow automation software even in just binding/finishing can automate the finishing process, including machine set-up, which is helpful to reduce dependency on skilled labor, reduce errors and improve overall production,” she said. “Again, the key is to evaluate the entire operation when considering the addition of workflow solutions to find the best configuration for each specific business.”
Future of workflow management
Valle foresees a better MIS in the future. “I think the impact is going to be a better MIS system that fully understands the process from order entry to printing, binding and down to shipping, where they can utilize and take advantage of the available standards, such as JDF and JMF,” he said.
“The current trend in the adoption of artificial intelligence tools across industries undoubtedly will have an impact and future changes on what we currently know of as XJDF,” Ruas said. “Workflow tools will be able to anticipate with greater certainty problems related to finishing processes which would help production processes to be further optimized.”
Also not new, but a growing trend Bailes-Collins sees is the ability for two-way communication between the finishing and the upstream systems. “Whether this is related to analytics relating to machine performance, or information regarding the progress and status of each job, this will enable real-time status data for managers, production planners and even customers to know what is where, if it’s on schedule or late,” he said.
As a work mix becomes more dynamic on the press and runs get shorter, Bailes-Collins said finishing automation also must be more dynamic in set-up and operation.
“Therefore, we expect to see more JDF automation, as a JDF set of instructions is job-specific and does not rely on a set-up on the finishing device,” he said. “In short, you won’t need any set-ups, and each job can have a different finishing set-up that automatically is controlled by accompanying JDF instructions.”
Potdar said she expects to see further improvements in compatibility to make integrations even more painless and cost effective. Many software providers are moving to cloud-based models so that print service providers can access data from anywhere, even across multiple business locations, to optimize operations on the go. She added, “We expect both print manufacturers and finishing manufacturers to continue to incorporate even more advanced automation, including robotics, predictive maintenance and data analytics, into their equipment and software to push the capabilities of workflow solutions even further.”
PostPress would like to thank Andrew Bailes-Collins with Ultimate TechnoGraphics, Inc., www.imposition.com; Yashi Potdar with Standard Finishing Systems, www.sdmc.com; Carlo Ruas with Taktiful, www.taktiful.com; and Mauro Valle with Müller Martini, www.mullermartini.com, for their assistance with this article.