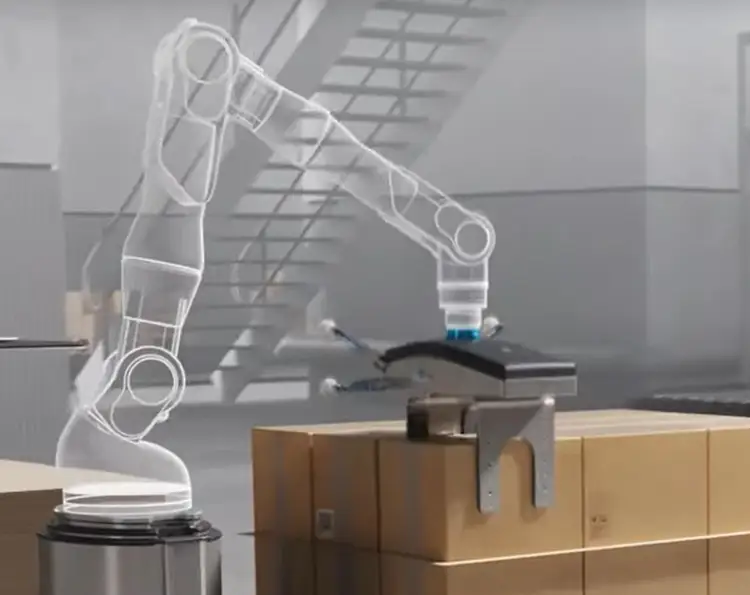
By Brad Emerson, general manager, www.fixyourownbindery.com
What have printers and finishers/binders seen in bindery automation advancements in recent years? Beyond robotics increasing their labor-saving advantages with paper banding and palletizing, it pretty much has been digital bindery automation advancements. While most binderies realize the benefits of well-calibrated manual measuring devices to input format data on automatic makeready equipment, it’s time to fully embrace the ‘touchless’ bindery workflow, which works seamlessly, end-to-end, in a digital bindery. The word ‘touchless’ on digital lines seems to be smoking out the real-world ROI benefits of automatic makeready alone.
The digital bindery automation bar has been raised in single-book production. For many, digital perfect binding is all the same where (among sizeable digital binderies) two digital bindery production worlds exist: long-run digital (grouped size formats) and single-book production, where each book has a size format change. One of the latest digital perfect binders released seems ideal for both with amazing 2,000 c/hr production in single-book format mode and 4,000 c/hr when only the content changes. This hybrid two-digital-perfect-binding-worlds-in-one binder goes a step further with optional signature-feeder expansion on the same perfect binder to include conventional offset perfect binding for short runs, adding a third type of perfect binding in one machine.
Automation review
Training first and foremost
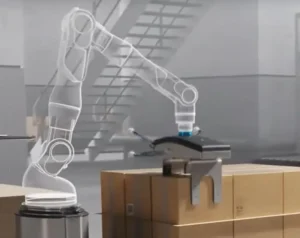
A manager’s training obligation isn’t completed by getting the PO number issued to bring in a training technician. Outside equipment trainers do not have the desire or bandwidth beyond the proper cycling machine to optimize the training to match the manager’s terminology, product mix, and existing systems and procedures. While it may seem ideal to train as many associates as possible, training three people works well. Fewer than three people may increase the cost per person and more than three people can lead to counterproductive sidebar conversations.
Before hands-on training starts is the perfect time to repair and tune the machine(s). Also, plan for a means to capture and transfer this valuable training expertise (usually video). If the ability to do in-house training does not already exist, seek outside options. Most original equipment manufacturers (OEMs) offer machine training on newer equipment. If new installation training at commissioning has been unsuccessful, find out what went wrong and incorporate lessons learned into the new training session. Operators might have to dig a little deeper to find an independent trainer(s) for legacy or obsolete equipment training. Whether an outside independent trainer is hired or an OEM technician, a highly skilled trainer or technician can teach maintenance technicians (in a separate session) beyond the operator’s routine minor maintenance duties.
Cobot automation
With the bindery labor shortage combined with rising costs over recent years, bindery cobots continue to arrive from major bindery equipment OEMs. This typically cage-free human/robot cohabitation is welcome in the bindery where relatively slow cobot speed does not restrict overall line output due to a particular plant’s product format mix.
Delta robots, which are popular in other industries (packaging), have yet to take hold in the bindery. Besides the Delta drawbacks of requiring interlocked safety enclosures, smaller x/y/z axis reach and lighter payloads, the major benefits cannot be denied: high-speed, lower investment cost and long-term cost of ownership savings of inexpensive maintenance-free components. Delta robots can cycle more than 10,000 cycles per hour, making them ideal candidates for bindery feeding and processing applications of ‘individual’ bound and unbound products. I hope any drupa bindery robotic releases this spring continue to accelerate this growing area of bindery automation.
Automatic and semi-automatic cartoning
Both automatic and semi-automatic cartoning have advantages and disadvantages. Semi-automatic cartoners have a distinct advantage over fully automatic cartoners as they allow the plant to produce extreme formats, plus they handle imperfect cartons. Trying to force a fully automatic cartoner near its format and size limitations in a general commercial bindery environment creates a manpower nightmare. When an extreme-size format job and/or off-spec carton shuts down an automatic cartoner for minutes, hours or days, a small army must appear to keep the line running, and then disappear when this carton job is finished – not a problem 30 years ago when a bindery had a few folks in the ‘handwork wings’ for such emergency tasks 24/7.
Palletizer automation
Whether a traditional palletizer or robotic palletizer, the ever-expanding palletizer installation base, combined with automated changeovers, is accelerating the transition from dedicated bindery lines to general commercial lines. Purchasing the right palletizer based on product format and speed requirements is only half the battle. It is important to visit/confirm with other satisfied palletizer users running similar product formats and production speeds before purchasing. Ask these questions:
- How well can the palletizer process uncovered stacks with thin endsheets on work-in-progress hardcover book blocks?
- Can the palletizer process variable height stacks when postal sorting?
- Can the palletizer locally be supported to some extent? The pain is real with a palletizer down. Additional labor must appear and disappear as a palletizer goes up and down to maintain production schedules.
Gatherer feeding automation

Processing difficult, thin paper stocks on new hard/softcover book binding lines has been realized with new thin paper adapters that now are on the market. The adapter gently allows the transfer of offset web press signatures for two-up production into the gatherer raceway, raising the industry bar in overall book quality and net production performance.
Printed digital roll automation
This is the most interesting and limitless area of evolving bindery automation. Whether a digital bindery is expanding its touchless capabilities or raising the roll width/‘feet-per-minute’ bar, the evolution from Gutenberg’s moveable type is most apparent.
We all have seen roll-to-stitched books or roll-to-perfect bound books, and more. From an unwinder into a sheeter into a folder or cut stacks, the possibilities seem endless except for electrical obsolescence. The only chance a digital bindery has against obsolescence is avoiding the complete ‘networked solution’ (if possible) when purchasing. Not only can a single component (unwinder or sheeter or folder or anything) of the overall line be powered off, but the network also remains satisfied if that component is permanently removed. Solid state and physical relay interfacing for upstream/downstream, stops/ready should not cause issues. And if an additional encoder is required to monitor upstream or downstream line speed to avoid the network, no problem.
Avoiding the network can create some touchless book data input challenges throughout the line depending on the OEMs, final line configuration and data handling. Upstream barcode scanners are great options, where possible. Preprinted laminated barcodes of a particular format to quickly wave in front of a scanner (or manually input data as a last resort) should be considered.
The elephant in the room
It was not by mistake that my first point in this article under the automation review subhead is ‘training first and foremost’ and not the latest in bindery automation equipment. The aftermath remains in our post-pandemic marketplace across many plants and industries – finding qualified personnel is difficult.
I know of no better path to the finish line than running smart and strong. Create the ‘perfect shift’ net production bar to be reached that is not just something easily achieved but celebrated with the bindery team. As a bindery manager, I always was fine-tuning my plans with my bindery personnel, whether taking longer or more frequent breaks to keep lines running or changing something responsively. Maximize the company’s entire investment: planning/implementing/training/running. Automation is necessary and will continue to be an important part of the bindery operation growth; however, people will remain the difference between success and failure.
Brad Emerson is the general manager of www.fixyourownbindery.com, a company specializing in consultation, consolidations, relocations, equipment sales and training. Email Emerson at brad@fixyourownbindery.com.