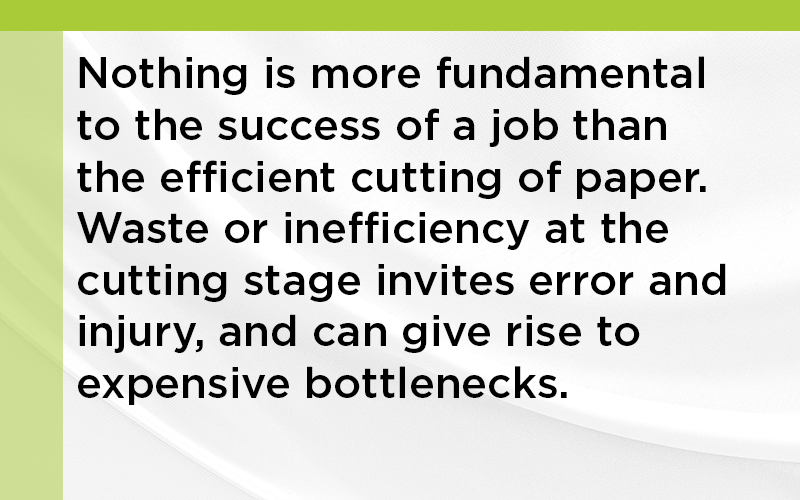
by: Rob Kuehl, Director of Product Management, Heidelberg USA, Inc.
Don Quixote had Sancho Panza. Batman had Robin. Even the Lone Ranger had Tonto in his hour of need. Like these famous pairs, automated cutter workflows are more efficient and more productive with a partner – paper-handling peripherals.
Nothing is more fundamental to the success of a job than the efficient cutting of paper. Waste or inefficiency at the cutting stage invites error and injury, and can give rise to expensive bottlenecks. Sheetfed operations, in particular, can benefit from the use of labor-saving devices that reduce operator bending and lifting.
In the bindery’s cutting department, emphasis has shifted from conventional stand-alone guillotine cutters that traditionally have relied on manual loading, offloading, and adjustment to sophisticated systems. These new systems are designed to protect operators from injury, reduce the occurrence of bottlenecks, slash the time that printed materials must wait on the cutting table, and ease the transmission storage and repurposing of job-specific data throughout the plant.
New cutting solutions meet the need for:
- Networkability
- Ergonomic integrity
- Minimal makeready
- Simple maintenance
- Operational readiness
- Faster turnaround
- Higher quality
- Simplified processing of shorter runs
- Fully automated production of large-volume jobs
- Integrated materials handling
- Complete cutting programs generated from prepress data, avoiding multiple input of complex job parameters.
The difference between stand-alone cutters and these more sophisticated systems is twofold. First, paper cutters have a limited ability to network with the rest of the plant. Second, a wide range of peripheral components are available to help ease the movement of paper to and from the cutter.
In any bindery department, the goal is to get material to and from the cutter quickly, easily, and reliably. Accordingly, the newest generations of high-speed cutters and cutting systems have been designed to be capable, productive, intelligent, user-friendly, ergonomically sensible, and infinitely configurable. However, equally important is the cutter workflow. An automated cutter workflow has two equally important parts: cutting and paper handling. Cutting is the main attraction, and it is performed by the cutter or diecutter itself. Paper handling is more easily overlooked. The default position of most bindery departments has been to rely on manual resources. Current options, however, are designed to standardize and automate as much of the grunt work as possible. Some of these paper-handling options include front- and rear-loading stacklifts, joggers, conveyors, and pile-turners.
It Takes Two
Both the cutter and paper-handling peripherals are necessary to achieve a fully automated system that maximizes the operator’s cutting time and the number of cuts delivered by the knife while also minimizing the volume of paper handled and the time and labor needed to handle it. The aim is not to eliminate the human element but to increase the utilization of both man and machine. Automated cutting and paper-handling systems can improve the workplace environment and promote the health and well-being of bindery employees. (See Figure 1.) Cutter peripherals promote better utilization and increase the efficiency of the high-speed cutter and cutter operator. Repetitive motions, including but not limited to bending and stooping, are responsible for many bindery injuries.
Automation can reduce:
- Time lost to cumulative trauma disorders, including back injury and carpal tunnel syndrome
- Accidents caused by operator fatigue
- Workers’ compensation claims
Well-designed mechanical solutions also can yield production efficiencies and drive growth by:
- Reducing shifts and overtime
- Redeploying workers
- Enabling fast turnaround
- Eliminating backlogs
- Taking on more jobs without increasing overhead
Additional benefits of automation include reductions in:
- Product damage
- Material waste
- Production and shipping delays
- Wasted floor space
Moving Toward Automation
While the bindery offers the biggest opportunity for realizing the benefits of streamlined materials handling, few printing company owners and managers see it as a means of reducing their manufacturing costs. Many hesitate to invest in post press upgrades because they dont consider the bindery a profit center and instead reserve the bulk of their capital investments for the pressroom and prepress department. The reality is, whether through benign neglect or ignorance of their costs, too many printing company executives treat cutting and paper handling as a necessary evil.
Cutting and paper handling are far from “top of mind” in all but the most highly industrialized printing plants – and sometimes not even there. Consequently, after a company installs a new press or piece of bindery equipment, jobs start piling up at the cutter because the bindery’s paper-handling solutions aren’t fast enough to keep up with the increased load. This is more likely to happen when people are considered the paper-handling “solutions.”
Given that the most expensive variable in any cutting operation is labor, replacing manual lifting and repetitive-motion tasks with streamlined mechanical solutions makes more sense today than ever. The task for vendors is to demonstrate how automating their customers’ manual practices can benefit employee health, safety, and morale, as well as throughput rates. Viewed in this way, the automation of manual practices can literally pay for itself.
Don’t overlook the gains that can be realized by reducing cutter operators’ stock lifting and handling
Laissez-faire Is Best
Virtually every sheet of material to be cut needs to be handled internally before and after it winds up on the cutting table. Depending on the application, paper might need to be lifted, jogged, aerated, turned, and repeatedly moved. If an operator has to do the bulk of the labor involved, he or she risks back injury, especially with large sheet sizes and heavy stock. In addition, the likelihood that errors will occur increases the more materials are moved around by hand.
The addition of automatic loaders and off loaders, stacklifts, in- and offline joggers, trim-removal and banding devices, sorting and inspection devices, electronic counting scales, pile-turners, robotic arms, conveyors, and buffering systems can significantly reduce turnaround times and reduce or eliminate operator fatigue and back-related problems. (See Figure 2.)
For example:
- Automated transport systems can regulate the efficient loading of materials to the clamp opening, reducing labor and promoting high productivity.
- Operators using a fixed or freestanding stacklift can raise loads to a convenient height for loading uncut sheets to the cutter or jogger, or for unloading finished sheets. (See Figure 3.)
- Automatic in- or off-line joggers can reduce the time it takes an operator to jog the stock into proper alignment for cutting, which makes for better product quality especially for high-quality, long-run jobs. (See Figure 4.)
- Automatic off loaders or palletizers can help increase throughput during cutting for large-volume applications.
- Pile-turners can facilitate preloading, work-and-turn applications, skid manipulation and aerating, and they can boost throughput by reducing or eliminating misfeeds due to double or missed sheets.
All of these peripherals are designed to increase the efficiency and utilization of the cutter and to make work easier and safer for the operator because heavy lifting is minimized or no longer required. Finally, graphic touchscreens and other user-friendly features of advanced cutting systems enable binderies to enjoy the benefits of computer-enabled technologies without depending on bindery employees’ high-tech capabilities.
Leverage Your Human Resources
Take steps to transform your cutting department from a loss leader to a profit center by automating as much of your cutter workflow as possible. Don’t “cut off your nose to spite your face” by overlooking the gains that can be realized by reducing lifting and handling by operators who are responsible for moving heavy stock to the cutter.
Consider an integrated, high-speed cutting system with flexible, modular paper handling. Cutting operations should not be balanced on the backs of your bindery employees. Do them and yourself a favor by installing systems that will help you leverage your human resources to their best advantage.
Rob Kuehl has been with Heidelberg in Germany and the U.S. for over 24 years. He was the first U.S. citizen to complete Heidelberg’s first-class machinist’s apprenticeship and moved up through corporate Manufacturing, Engineering, Procurement, Research, and Development. He can be reached at rob.kuehl@heidelberg.com or (770) 419- 6636.
Reprinted with permission from the 2008 GATFWorld. Copyright 2008 by the Printing Industries of America/Graphic Arts Technical Foundation (www.gain.net). All rights reserved.