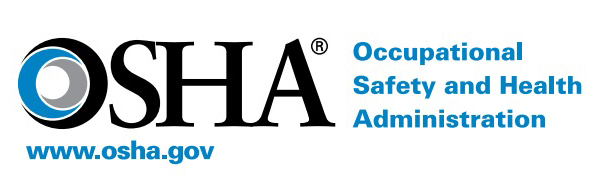
by Rick Hartwig, Printing Industries of America
The Occupational Safety and Health Administration (OSHA) never can announce an enforcement inspection ahead of time, but it does provide a host of indicators that can be used to predict the chances of an inspection. OSHA collects a vast amount of data on specific industry sectors that are used in part to develop materials such as compliance directives, emphasis programs and injury and illness trends, among others. Combined, this collection of information paints a picture for a particular industry or sector as to OSHA’s focus, and therefore, probability of being selected for an inspection. For companies within the printing and printing-related sectors of manufacturing, the probability for enforcement inspections is high. Ultimately, (OSHA) has the legal authority to develop and issue standards and enforce those standards through on-site inspections.
What Triggers an OSHA Inspection?
OSHA inspections occur for a number of reasons such as a programmed inspection policy, employee complaints, other agency referral, the Site Specific Targeting (SST) program or through self-reporting requirements.
Programmed inspections are the result of OSHAs emphasis programs, which are designed to address specific hazards or industries with particular risks and are the main trigger for inspections these days. These could be either local emphasis programs (LEP) or national emphasis programs (NEP). While there are several programs concerning General Industry, the two main NEPs impacting the postpress industry include the Amputation NEP (addressing injury potential associated with running certain equipment) and the Combustible Dust NEP (addressing fire and explosion hazards associated with paper dust generated within the bindery operations). Employee complaints remain the second largest reason for enforcement inspections to occur. The Site Specific Targeting (SST) program is a database of injury and illness data collected by OSHA through a survey of companies, and it identifies companies that have higher than average injury or illness rates. Both states following the Federal OSHA plan and those with OSHA-approved state plans are required to implement a targeting system. Agency referrals occur via first responders, police, fire rescue or others that report to a company incident because of an accident or emergency. Self-reporting of accidents or fatalities are self-explanatory.
Understanding Inspections
Those involved in the printing industry need to recognize and treat compliance of OSHA standards as a true legal issue that has the potential for legal action. Days or weeks prior to an inspection, OSHA begins to make its legal case by collecting information about the company and continues this effort throughout the inspection process. This can include records of previous violations, corporate structure of the company, operations performed at the company, equipment used and applicable industry standards. OSHA will be working to prepare a case that would hold up in court if necessary. Will your compliance program?
Once at the facility, OSHA will hold an opening conference and then begin the physical inspection, which will include a records review of injuries and illnesses forms, a facility tour, photographs, written notes and confidential employee interviews. A closing conference is held at the end of the inspection process, which can be anywhere from a few hours to a few weeks depending on the circumstances or scope of the inspection. Finally, the Area Director for OSHA will determine whether any citations should be issued and assess the appropriate penalties.
If citations are issued and a notice of penalty is issued, there are opportunities for discussion to clarify or contest either a citation or penalty; however, a companys best chance of success is with a fully compliant safety program already established.
What are some of the core materials to have developed for compliance?
- Written programs
- Company policies and guidelines
- SOPs
- Sampling/test results
- Audits and assessments
- Medical records
- Injury and illness recordkeeping
- Accident investigation reports
- Training records
- Discipline records
In order to be sure a company is in compliance, the company must have a strong knowledge and understanding of the applicable OSHA regulations. There are over 130 general industry rules that could apply to postpress operations. Some of the regulations have very specific elements that often are overlooked and cause increased and unnecessary citations to be issued. Further, to effectively defend the company’s compliance program, an understanding of all supporting evidence is needed. This can include letters of interpretation, OSHA directives, case law precedence, compliance strategies, ANSI standards, ISO standards, NFPA standards and much more. An OSHA inspection can be well-managed if the facility understands the scope of the inspection, has a compliance program in place and understands which regulations do and do not apply. Effectively communicating the compliance program to all employees and having documentation to support the safety program that was implemented can go a long way toward ensuring compliance and making it through the OSHA inspection process.
The Best Offense is a Good Defense
A review of 100 companies cited by OSHA showed that 58 percent had not developed a required compliance program. Of those with a compliance program, 71 percent were found to be generic, missing several key elements and/or seriously inadequate. Eighty-two percent of those with generic programs were unaware of any of the standard requirements. The citations and penalties associated with these companies easily could have been avoided.
A commitment must be made to ensure OSHA compliance. The first step toward that commitment is assessment. Inventory your facility and operation; find out what is actually occurring and measure this against the regulations. Initial development of a compliance program cannot begin without support from all levels of employees, so seeking staff input is vital. Additionally, compliance requirements must be woven into everyday business operations and should be handled just like any other personnel matter in order to be effectively maintained and monitored.
Compliance does not have to be “THE” priority, but it must be “a” priority. A leader must be appointed to walk the company through the requirements, and that leader should be given thorough training and support.
As previously mentioned, all employees should be involved in compliance efforts. Explain the need for compliance and ask for input from the front-line employees. Find ways to combine OSHA requirements with everyday procedures, and make those procedures consistent throughout the facility. Then maintain oversight, whether through safety committees, production meetings or scheduled walk throughs of the facility. Violations should be addressed with consistent and fair disciplinary measures that demonstrate – both to the employees and potential OSHA inspectors – that compliance is active and a priority.
Remember, inspections cannot be prevented, but preparation can greatly improve the outcome.
Rick Hartwig is manager, Environmental, Health and Safety Affairs at Printing Industries of America. With over 27 years’ experience within the printing industry, he has been directly involved with operations management, regulatory compliance and sustainability. In his capacity, Hartwig works closely with all regulatory agencies on addressing related EHS issues at the federal, state and local levels. Hartwig provides assistance to print members, including regulatory and standard interpretations, industry representation, enforcement and penalty engagement, sustainability consultation, facility and operation assessments and compliance program reviews. For more information, visit www.printing.org.