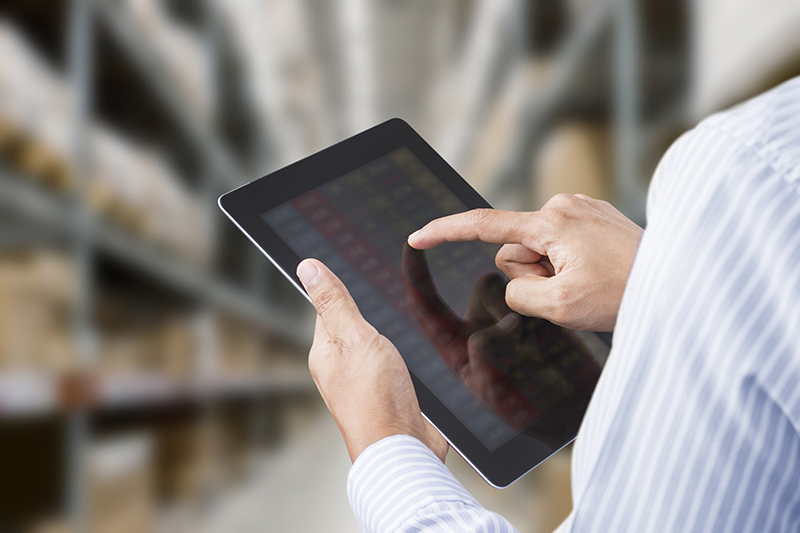
by Grainger Editorial Staff
Is a large percentage of your company’s dollars going toward inventory? Managing inventory efficiently can help cut down on many costs that you may not even be aware of. Poor inventory control can lead to emergencies, such as running out of much needed materials. This can take time away from production, and finding a quick replacement part can be expensive. On the other end, an overstock of products can take up valuable shelf space and lead to unnecessary purchase costs.
Knowing the flow of managing your inventory is the first step to getting a better understanding of how inventory control works and how you can manage your inventory properly.
Types of inventory
Different facilities keep stock of different items to fill different needs. Because hospitals are service-based businesses, their inventory will mostly consist of items needed to perform medical care. Bandages, disposable gloves, thermometers, even surgical tools – these are all items that must be available for everyday use.
Manufacturing plants, on the other hand, will have a strong inventory of production materials. Sheets of steel, plastics, parts for assembly – these materials must be on hand to keep business running. Retailers also carry a high inventory of items waiting to be sold, and running out means missing out on potential revenue.
Other industries, such as hotels and offices, may not need as large an inventory as manufacturers, retailers and hospitals, but they will have an inventory of maintenance, repair and operations (MRO) items. Light bulbs, reams of paper, ink cartridges, fuses you name it – this all contributes to an inventory that costs money to purchase, store and use.
The flow of inventory
Regardless of the type of inventory your business is handling – whether it’s for service, manufacturing, retail or maintenance – there is a common flow that can help you manage your inventory better.
Purchase
An initial purchase must be made to get things going. Unless your facility is an expansion, your first purchase will be based on your best estimate. In order to make the best guess possible, try researching what other facilities like yours are using and in what quantities. For your first buy, it is better to err on the side of caution – this is one time where having a little too much won’t hurt. This will allow you enough wiggle room for mistakes, but be sure to allot enough storage space for surplus.
Store
All the items you purchase have to go somewhere. You will need enough storage space, as well as an organized system in which your on-hand items are easy to find and get to. Time spent searching for an item or traveling to and from the storage location is time that is taken away from your business.
Use
Congratulations! You’re in business. That means that items that have gone into your inventory are now being taken out. One by one, the items are removed from their storage location and are sold, used or fabricated – whatever the case may be. In this stage, the items are being taken for their intended use.
Tracking
As items are purchased and used, it is essential that they are properly tracked. A system must be in place in order to know, at any given time, how much of a particular item you have on hand. This way you will know when your supply is low and needs to be replenished.
Reorder
Once an item has reached its reorder point, it is time to replenish your supply. This can be done manually or through automated systems.
Forecasting
Once you have used, tracked and reordered a few times, it is possible to start forecasting your future needs. This is a proactive attitude toward your inventory in which you take control of what to bring in ahead of time, rather than waiting for your supply to deplete and reacting after the fact.
Common management pitfalls
Just as inventory flow is similar among industries, so are the common issues that cause costly inventory problems. Being aware of common problem areas can help you avoid potential (costly) mistakes.
Lack of automation
With computerized options available to track, forecast and reorder items for you, there is no longer a need to miss a needed reorder. Manual tracking takes time, and even the most skilled data-entry person will make mistakes. There always will be a gap between updating records and the real-time use of your products.
Improper training
Any system you have in place for tracking your inventory won’t amount to much if the people responsible for keeping those records arent using it. Inventory software users should be fully trained on the program, and the workers using the inventory must be trained on how to account for the items that they use.
Picking inefficiency
Efficient organizing of your facility’s space can make a world of difference in your productivity. How much time are your workers using to get to the items they need? How difficult is it to get from the point of production (or sale, or service) to the storage space? How easy is it to find the most used items on your shelves?
Infrequent cycle counts
Yearly cycle counts represent a costly and ineffective way to reconcile what you think you have with what you actually have. This usually involves shutting down operations for a day or two to take your inventory counts for all the items you stock. More frequent cycle counts on specific areas can be more cost-effective and will keep a regular tab on what you have on hand.
Sources
http://mhlnews.com/warehousing/top-5-solutions-common-inventory-management-mistakes
https://www.entrepreneur.com/article/252704
http://www.dummies.com/business/accounting/how-to-track-inventory-flow
Reprinted with permission from Grainger. The information contained in this publication is intended for general information purposes. No representation is made that the information or references are complete or remain current.