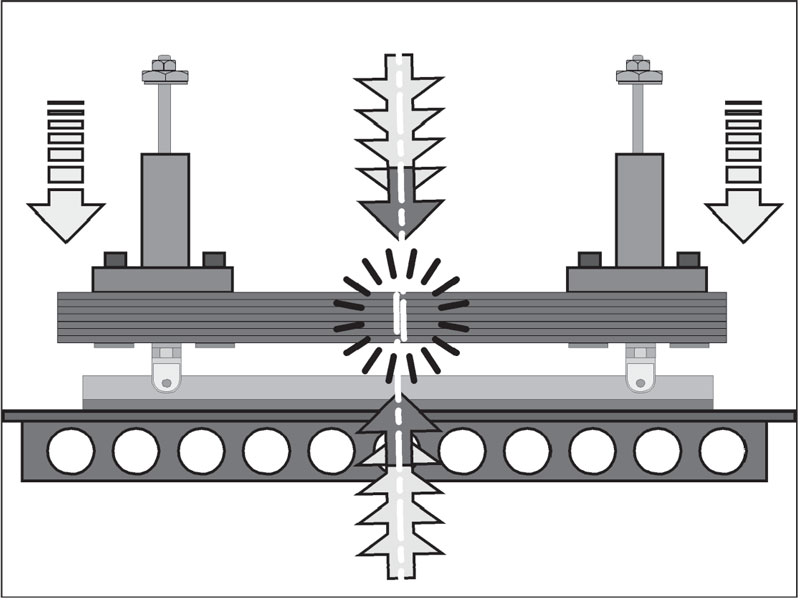
By John Norgard, president
Converting Technology, Inc.
The following article was derived from a presentation made at a previous IADD•FSEA Odyssey. For more information on Odyssey Expo 2019, visit www.OdysseyExpo.org.
For many applications, stripping can be the most difficult aspect of sheet-fed diecutting, not to mention the stiff necks from spending countless hours under a press setting pins or the occasional minor concussions from standing upright too soon when exiting. Unfortunately, we spend too much time underneath a cutting press trying to understand how stripping works.
The press stripping station determines press run speed. Therefore, it is extremely important that the tools used are designed properly for the material running and the scrap shape that is being stripped. The introduction of the quick lock system eliminates the majority of pre-makeready time and brings to focus the importance of bottomless pin stripping.
Why is stripping difficult?
The first area to examine is carton design, because many times a simple carton design change can make the difference between successfully stripping or struggling on press. Diagram 1 shows a simple redesign that resulted in 100% bottomless pin stripping.
The original design has a radius on the tuck fl ap that joins the straight knife at almost 180 degrees.
The original design makes it very difficult to get a proper fitting rule joint and potentially can cause natural nicks, which would interfere with stripping. The original design also has a narrow gullet with angled knives between the minor and major flaps.
To facilitate stripping, a simple change was made to the tuck radius, and the gullet area was opened up by changing the angled knife to a radius. These simple changes eliminated the potential of natural nicks and opened up the gullets so that restrictions could be placed on either side of the scrap and a stripping pin in the middle of the scrap.
Communication is key. When designing cartons, all aspects of manufacturing should be considered. These include printing, diecutting, gluing and performance on the filling machines. Many times, poor designs are copied because they are submitted as correct size and style. Furthermore, production operators are not always asked for their input on how to improve run efficiency.
Tooling and press maintenance
The quality of the dieboard determines stripping efficiency. Items that inhibit bottomless pin stripping include broken miters, natural nicks, over-nicked scrap and incorrect ejection rubber.
A rule map, with running spares, is required on press. The map is numbered, showing the sequence the die was knifed. In the event of a smash-up, the press operator can use the map when replacing knife. This prevents breaking of miters when rule is being replaced on press. A die condition and repair form completed at the end of the run will ensure that repairs are made before the next press run.
When programming the ruling sequence, the operator should preplan where the nicks will be and how the job will be mitered. When knifing the die, rule number one is inserted first, followed by two and so on. When replacing rule, the sequence is reversed. If the nick is placed in the run direction and the scrap is not balanced, it will cause the scrap to pivot and not strip cleanly. Nicked scrap must be balanced.
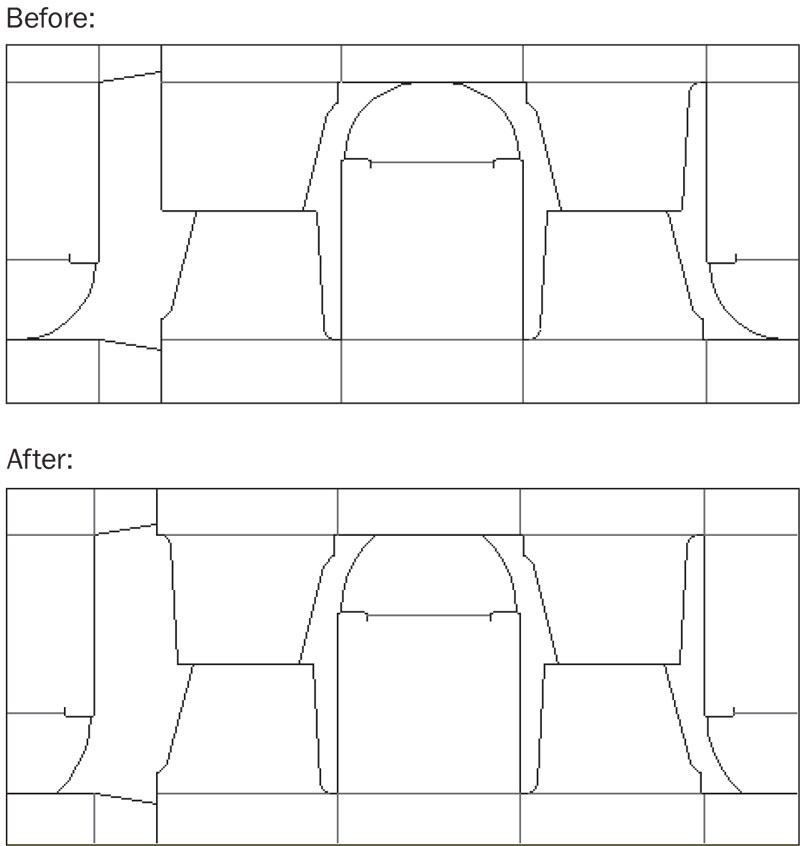
Each tool on the press must line up not only to the sheet, but also to each other. The machines that are used to manufacture the tooling should be routinely checked and verified to be within tolerances. It can take up to four machines to manufacture a full tool set: one to laser cut the dieboard, another to laser cut the blanker and lower stripper, a machine to insert stripping pins and a counter cutting machine.
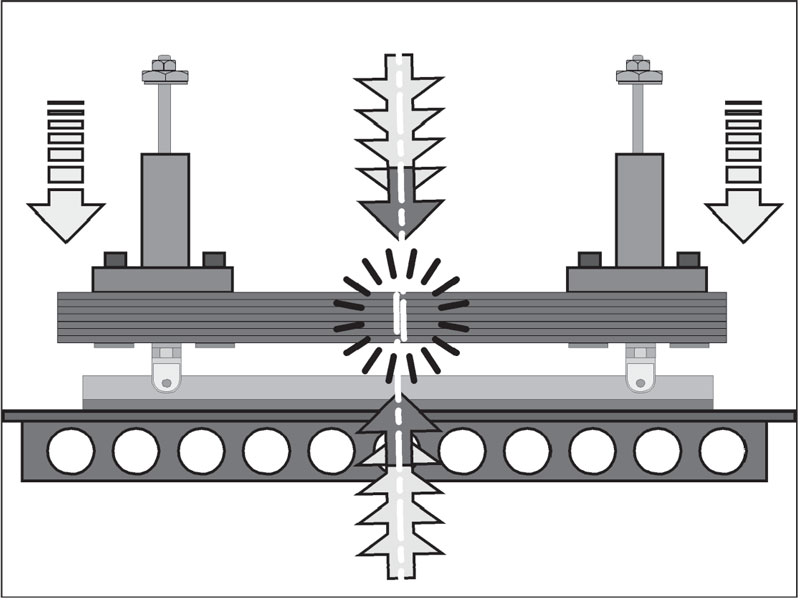
Tool-to-tool registration alignment. Quick-Lock systems eliminate alignment problems. Tools are inserted into the press and locked in place (see Diagram 2). On older machines, make sure the pre-makeready tables are synchronized with the presses. This will eliminate time on press spent trying to realign the tooling.
Press maintenance is of utmost importance. Chain stretch and parallel alignment of chains and grippers have dramatic effects on successful stripping. To fully benefit from new tooling design, the press must be able to hold acceptable tolerances.
Nicking on press
All internal scrap should be nicked before the job goes to press. This results in controlled nick size and placement. Since all press operators have nicking preferences, it’s best to gather everyone and review numerous jobs. This will result in a nicking consensus and reduce changes being made on press. The goal should be, on press, to only have nicks that hold the sheet together and are necessary because of changes in the substrate.
Another suggestion is to be sure all nicks are included in the CAD program and placed behind the rubber so that they are visible when etched in the dieboard. Another option is micronick rule. This rule is manufactured in different quantities of small nicks per inch and ensures uniformity.
Eliminate problems
The concept of bottomless pin stripping has been around for years. We now have the machines and hardware to successfully predict performance.
Let’s look at how to support lower stripping boards. If the lower stripping board is not properly supported, it will flex. When the board flexes, the restrictions do not line up, and positive stripping is compromised. Support bars can be installed by a diemaker so that they are permanently attached to the lower stripper. This will eliminate the need to re-attach bars each time the jobs run.
Another common problem is the presence of too much foam on the upper stripper. Too much foam will prevent the upper tool from fully penetrating the lower tool.
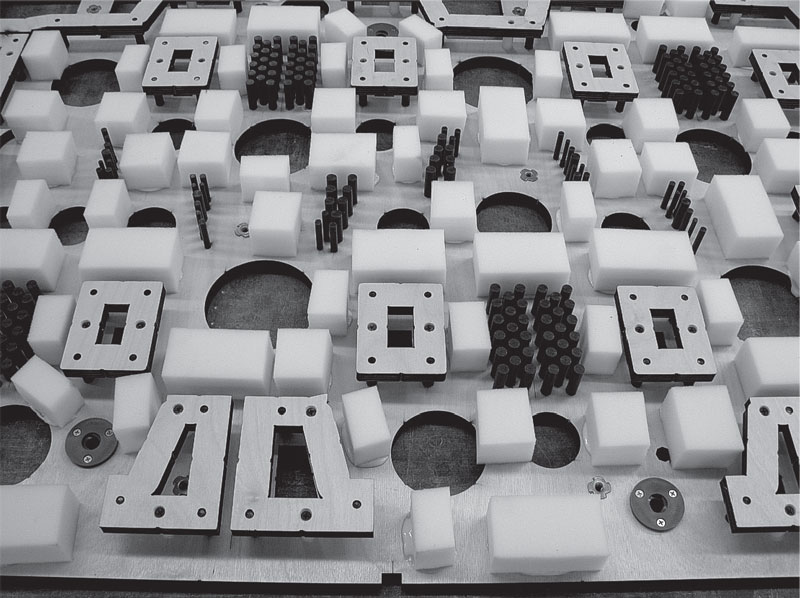
Diagram 3 shows an example of too much foam. The only purpose of foam is to hold the sheet stable while stripping.
Place the foam behind the pins far enough away so there isn’t pinching between the opening of the lower stripper and the pin on the upper stripper (see Diagram 4).
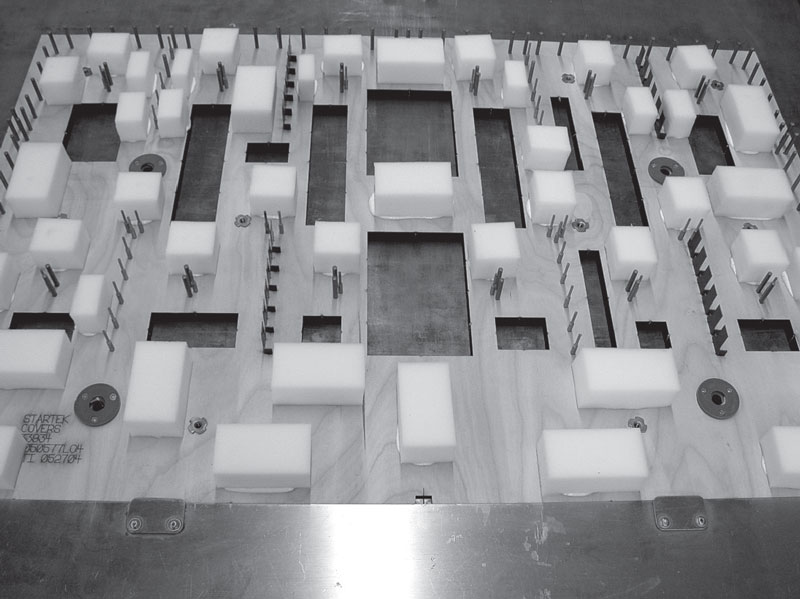
Stripping equals speed
The potential for increased yield lies in the ability to strip at maximum speed.
Where do we start? First benchmark by documenting current press makeready times and elapsed per-hour run speed for each cutting press. Keep separate records for each machine. Make sure numbers of makereadies per day/week are recorded for each machine so that elapsed per-hour press run speed is accurate. Then document labor hours for setting up and tearing down pins in the pre-makeready department.
Set goals. Communicate makeready and run speed goals to the press crews.
Measure performance. Continue to document makeready time and press run speed, and communicate that information to press crews.
Assign value. What is the value of increased throughput? I believe improvement should be measured by assigning an average sales price of a diecut sheet, then multiplying by the sheet-per-hour increase. Calculate this number over a one-year period, and it will be surprising to see the amount of additional sales dollars a diecutting operation can run without adding labor or new equipment.
Minimize overhead and press downtime by determining which stripping system works best. Use a stripping system preference for all jobs. However, many times companies are tempted to try a new system on the most difficult jobs. This is a mistake when a new tool is presented. Remember the 80/20 principle and select a job that represents 80% of the work mix. Otherwise, failure can be expected.
Any new stripping system must be explained to the entire press crew, and the vendor should be on hand for the first run. It also is recommended to make sure that the first trial run is performed during the first shift. The last thing a diecutting manager wants to hear in the morning is that a press was down for an extended period of time, and the new tool didn’t work, but no one knows why.
One success does not solve all stripping problems! Make sure the diecutting manager or a lead person is assigned to monitor all jobs with the new tools. Operators have a habit of going back to old ways if they encounter difficulty. Most times, jobs are not stripping because of off cutting, nicks had to be added or the tools are not aligned properly.
Effective stripping without bottom pins is an achievable goal. It takes time and determination, but the rewards are huge.
Editor’s note: The author thanks Kevin Carey, Kevin O’Connor and Brad Owen for their help in putting together the Odyssey presentation which led to this article.
John Norgard is president of Converting Technology, Inc., which is a leading supplier of laser cutting dies and all related tooling for both sheet-fed and web cutting presses. The company’s customers include manufacturers of folding carton, micro-flute and related packaging. For more information, visit www.convertingtechnology.com.
This article appears in a past issue of IADD’s The Cutting Edge: www.iadd.org.