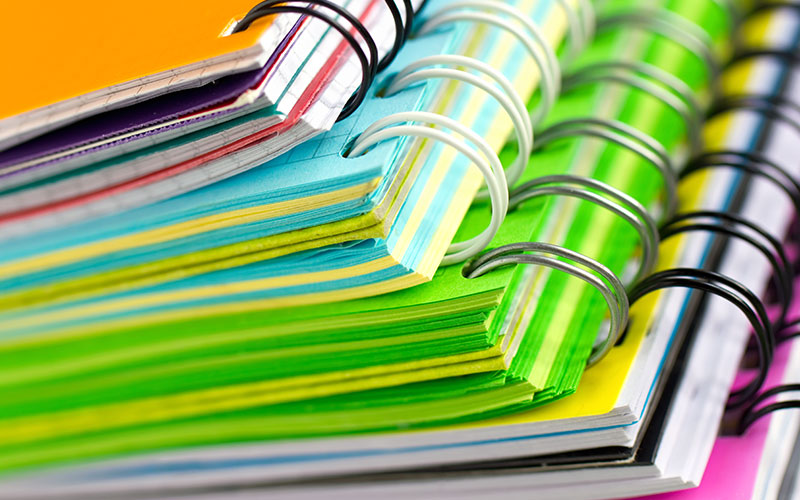
Reprinted from The Binding Edge
While many predicted the digital age would be the death of print, time has proven that to be anything but true. If anything, digital technology and print have proven to co-exist quite nicely. This is due in part to the continued need for hard copies of important documents and reference materials. As a result, processes such as spiral binding and on-demand printing will continue to have a place and purpose even as technology continues to evolve.
Industry experts at Punchmaster Tool & Die Ltd. and Update Ltd. have weighed in on the subject of paper punching technology in the digital age and how technology has and will continue to affect the process.
What factors can affect the quality of the paper punch?
Todd Boynton, owner of Update Ltd. in Chaska, Minnesota, recommended investing in high-quality punching equipment and then maintaining that equipment to ensure that it holds up and stays sharp.
“You have to stay on top of the maintenance and replacement aspect,” Boynton said. “The replaceable parts – the parts that do the piercing – are made in different capacities, and some punches are made better than others,”
John Xynos, owner and operator of Punchmaster Tool & Die Ltd. in Sharon, Ontario, Canada, added, “Punching tools are highly misunderstood. For example, I commonly hear people ask for a spare set of punch pins. They figure that if they get a bad cut, then they simply can replace the pins and the hole quality will be as good as new. But, that is not the case.”
He explained that when it comes to punching tools, it’s the fit that provides the hole quality. “If you have a bad fit – if the pin is sloppy in the hole – then the punch quality will be terrible. The sharp edge on the punch pins does help, but not as much as the proper fit does,” Xynos said.
How can operators determine the best die to use for the punching job?
Both Boynton and Xynos said die choice is customer driven. “There are many patterns available – oval, round, square, etc. – and there are six or seven different punch machines on the market that can create the pattern most desirable to the customer for the job at hand,” Boynton said.
Have there been any recent advances or modifications to paper punching equipment?
According to Xynos, punching tools have not changed much in the last 10 years. He added that, “If you don’t do it on press, you only can punch through so much thickness at a time – 12 sheets up to 4.5 mm thick – regardless of new technology.” Boynton added, “You can spend a lot of time and money designing conveyance or auto-feeding capabilities, but in the end, the job still will require a lot of handwork.”
Xynos said that Punchmaster uses the best steel alloy for any application, and if new technology or materials become available, then the company will test it on a few tools. “We will build a tool using new materials and then provide it to a trade bindery for a trial period of time,” he explained.
How has the demand for faster production speeds and smaller run sizes changed paper punching technology?
Xynos said the switch to digital panels has resulted in faster changeovers for smaller runs. Boynton added that coil has sped things up nicely in the smaller-run market, but standard notebook work hasn’t changed much despite increasing demand for faster production speeds and smaller run sizes.
What maintenance steps should be taken to keep the punch working efficiently?
When it comes to lubrication, different tools require different lubrication. “All tools that have a felt strip should be lubricated only with oil,” Xynos said. “We recommend using only oil on all Punchmaster tools because our fit is very precise. The worst thing you could use on our tools is grease, which is too thick to get where it’s needed.”
Boynton added that the cleaning, storage and handling of punching tools is very important. Once the teeth become dull, there’s an entire row of teeth that will need to be either sharpened or replaced.
Punchmaster Tool & Die Ltd., Sharon, Ontario, Canada, specializes in designing and building paper punching tools and providing equipment manufacturers with tool designs for use in their punching equipment. Update Ltd., Chaska, Minnesota, is a service company that provides a variety of equipment, parts and supplies for the finishing industry. For more information, visit www.punchmastertools.com and www.updateltd.com.
Troubleshooting and Maintaining Punching Equipment
Trouble usually arises with punching equipment when the holes are not cut smoothly or evenly, or when the machine seems to jam. This often is due to a few simple reasons:
- The paper is not lined up correctly in the unit, so that the resulting cut is not parallel with the edge of the paper.
- Trying to process too many sheets. As a result, the bottom holes may not completely pierce the paper.
- The chip tray is so full that the paper chads created in the punching process block access for more waste.
When done carefully, lining up the pages to be bound is simple. In the punching process, be sure not to exceed the drilling capabilities of the machine. If trying to punch more than the recommended number of pages, the machine punches may be incomplete, and, for manual machines, may require putting more pressure on the handle. For electric machines, this can strain the motor.
As for paper waste, cleaning out the tray is a matter of replacing a cover or opening a door, so it should be emptied during and after jobs to prevent clogging. If punching a document with adhesives, die maintenance should be done, as described below, when the job is complete. This prevents the adhesive from hardening around the pins.
Most problems with the machine can be controlled by proper use and occasional maintenance to the machine and the dies. By simply dabbing lightweight machine oil on a cloth, and gently rubbing it over the exposed areas of the punch pins while the die is out of the punch, it can be lubricated so the unit runs smoothly.
Before resuming work with the machine, punch some scrap paper until the oil is absorbed – usually after several punches. Use the same lubricating process on dies after using paper with adhesives on it. If using accessories, such as an electric coil inserter or openers or closers, check the instruction manual to see if these parts need lubrication.
The information for this sidebar was obtained from the Rhin-O-Tuff blog post, “Well-Maintained Binding Equipment Makes for Clean Machine Punches,” by John Lugviel, vice president of business development, www.rhin-o-tuff.com/blog. For more information on Rhin-O-Tuff’s line of bindery equipment, visit www.rhin-o-tuff.com.