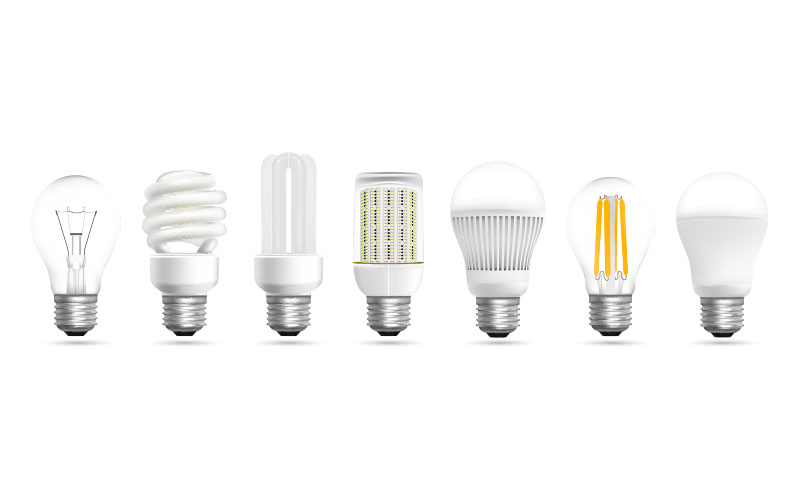
by Grainger
When you look for ways to enhance your profit margin, energy management is a logical place to begin making changes. Doing an energy audit or switching to energy-efficient lighting, two key steps in an energy management program, can have a significant impact on the bottom line.
Yes, as the operator of a large facility or multiple large facilities, you will need to make an investment – perhaps substantial – to get the ball rolling on energy management, but the data compiled by the US Department of Energy’s Energy Star clearly indicates that the savings will be real and that you will begin to realize them in fairly short order. Energy Star notes, for example, that the average commercial building wastes 30% of the energy it consumes1.
Understanding energy management strategies can help your business benefit fiscally, but it has other advantages as well. If you’ve not explored this area before, take time to review key property and behavioral changes that can boost your business’s profits, improve productivity and increase safety.
Switching to LEDs
One of the biggest ways to reap savings comes from small sources – your lighting. The newest generation of bulbs – light-emitting diodes or LED lighting – offers more bang for your buck than traditional lighting options, such as standard filament (incandescent), halogen and fluorescent strips. LED bulbs can last far longer than other lighting choices, with a range of 20,000 to 70,000 usage hours, while the average life span of incandescent bulbs is a diminutive 1,200 hours. LEDs also outdistance another energy-saving choice, the compact florescent lights (CFLs), by four to five times the life span.
Fewer replacements means lower direct and indirect costs, as well as reduced hazard potential. When you switch to LED lighting, you’ll spend less money replacing bulbs, and you also won’t be bogged down with frequent, time-consuming production delays while new bulbs are installed.
In many cases, the replacement of ceiling bulbs requires an aerial lift or extension ladder, which can contribute to numerous safety hazards. Limiting the number of times this operation is conducted by installing longer-lasting LED lighting certainly is an indirect but vital benefit to productivity and worker safety. Plus, since LED tube lights do not require a ballast the way fluorescent tube lighting does, maintenance of the fixtures is less costly.
However, the biggest bonus is in the energy reduction. Not only do LEDs last longer, they use just a fraction of the energy (up to 80% less) of conventional lighting and throw off far less heat, which can reduce the need for cooling and air conditioning. Remember that halogen and incandescent bulbs produce light as a by-product of heat and release up to 90 percent of their energy as heat. LED bulbs, by contrast, provide light as their foremost function and release little heat. Switching to LED lighting means your organization can start seeing an almost immediate return on investment as monthly electric bills plummet.
LED lighting has additional benefits that help it outperform other choices. For property areas that necessitate prompt lighting, LED provides the security of immediate bright lighting, unlike CFLs, which require time to reach full brightness. If full brightness isn’t required, a dimmer switch can be used on LED lighting, which is not an option for some lighting products.
To add to their many cost-saving benefits, LEDs are more durable to shock, vibrations and temperature extremes than traditional lighting. The bulbs do not contain harmful mercury, which means LEDs are environmentally friendly. They spread light uniformly, come in a range of hues (from soft amber to bright white) and can be tailored to the location and user preference. These factors can increase worker productivity and property security. The low heat emitted by LEDs also makes them a safer option than traditional lighting.
You won’t drop a bundle making the upgrade. If you’ve priced LED lighting in the past, you may be pleasantly surprised to find the price has significantly dropped in recent years. Bulbs that once cost $100 each have dropped to a fraction of that, with most standard LED bulbs in the range of $3 to $8. The lower price point means business owners now can retrofit the entire property with LED at a nominal cost. (The US Department of Energy has a run-down on options, complete with cost comparisons2.)
Changing behaviors
To make additional and meaningful cost reductions, look at your workforce. Profit improvements can be made by modifying behavior to be more energy efficient.
Although behavioral changes aren’t as easy as replacing light bulbs, new habits can be learned over time, especially when they are embraced as a whole organization.
Among ways to save costs and conserve energy are the following:
- Perform routine maintenance on equipment, especially on HVAC systems
- Install or use fans to assist HVAC systems
- Reset the thermostat for weekends and after hours
- Institute practices to keep vents clear and unobstructed
- Inform employees which equipment can be shut off when not in use
- Use laptops, as opposed to energy-hungry desktop computers
- Make it a practice to turn lights off when areas are not in use, or install motion detector switches
Whenever possible, select energy-efficient windows, appliances and equipment, such as those labeled as Energy Star®-certified. These products are designated to save significant energy and meet stringent industry requirements.
For example, computer monitors that are Energy Star-certified are 25% more energy efficient than standard options. If you have an entire department using outdated monitors and computers that consume large amounts of energy, replacing them with efficient models might be an investment that pays for itself in a relatively short time.
Conduct or commission an energy survey
With your managerial and technical leaders, perform a survey of energy usage that considers areas such as industrial processes, refrigeration, HVAC and building controls. You also can commission an in-depth survey by an independent source.
Monitor business energy consumption and try to avoid high usage during peak times, as your cost may be increased during these peak hours. Talk to your local utility companies about peak and off-peak programs and pricing. It may be worthwhile to run some heavy equipment later in the evening, when electrical rates are lower.
Commitment
Change starts at the top. Create a written statement of senior management’s commitment to energy conservation and its environmental impacts. Include strategies, such as procurement of equipment and procedures, which outline how energy-saving methods will be applied.
Using tax credits, rebates
Not all improvements need to be out-of-pocket costs, either. Businesses may find credits, grants or reimbursement options to help fund energy-efficient lighting, equipment or HVAC changes through various programs. Federal tax credits have been available previously for property owners making energy-efficient upgrades. Local utility rebates or state program options may be in place. Check the Federal Energy Incentive Program3 for a list of funding opportunities available in each state.
Remember, embracing energy efficiency in your organization need not be a dramatic or costly investment. Even small steps, such as swapping out light bulbs, will make a difference that you’ll see reflected in your bottom line. And, as energy management practices are incorporated as a company goal with the support of corporate leaders, the benefits will only increase.
References
- https://www.energystar.gov/buildings/facility-owners-and-managers/existing-buildings/save-energy
- https://www.energy.gov/energysaver/save-electricity-and-fuel/lighting-choices-save-you-money/led-lighting
- https://www.energy.gov/eere/femp/state-energy-offices-and-organizations
The information contained in this article is intended for general information purposes only and is based on information available as of the initial date of publication. No representation is made that the information or references are complete or remain current. This article is not a substitute for review of current applicable government regulations, industry standards or other standards specific to your business and/or activities and should not be construed as legal advice or opinion. Readers with specific questions should refer to the applicable standards or consult with an attorney.
Grainger provides discounts to FSEA members in a variety of categories, including safety, material handling, power tools, motors and more. Visit www.fsea.com for more information or log into your Grainger account at www.grainger.com.