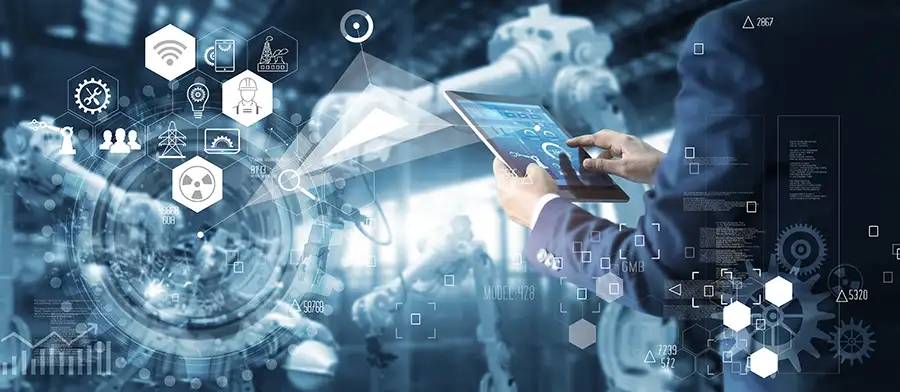
Submitted by Messe Düsseldorf
Continuously networked, digitally controlled, quality-monitored, fully automated, vertically integrated from the sensor to the cloud, and horizontally integrated across company boundaries – these buzzwords summarize the most important technology trends on the way to Industry 4.0. What is more important for users is what concrete benefits they will derive from this. Answers can be found by looking at the economic development in the print and packaging industry:
- Cost pressure and competition are increasing.
- The globalization trend continues.
- Customers are becoming more aware of quality and the environment.
- Run lengths are falling, large orders are being called off in batches as required.
- Demand for individualized/personalized print products is increasing.
Print and Finishing 4.0 provide the right answers to these challenges. Automated, inline, quality-monitored data and process chains simultaneously guarantee maximum efficiency and maximum quality. Inspection systems detect minute color and position deviations in print, embossing or finishing at every stage from artwork to postpress and find missing dots, commas and faulty characters across all languages.
Where the human eye cannot keep up at all or only slowly, image processing ensures process reliability, precision and efficiency when setting up new print jobs. Startup waste and misprints can thus be reduced to a minimum. This fully automated makeready of new jobs and the seamless linking of previously separate work steps to form continuous process chains are the keys to successful, high-quality production, despite falling run lengths. The more intelligent and autonomous the print and packaging technologies, the less dependence there will be on the experience of qualified specialists, which only is accessible to a limited extent in many places.
Thanks to international standardization efforts, machines and systems from different suppliers usually now can communicate smoothly. The Open Platform Communications Unified Architecture (OPC UA) provides the appropriate framework that is being recognized by more and more industries and players. Where a continuous flow of data from prepress to postpress is ensured, process linkage quickly follows suit. Instead of the usual stagnations between individual process steps, the duration of which depended on employee availability, a continuous production process is established. Capacity utilization increases, the need for storage space decreases and monotonous tasks, such as breaking out punched folding boxes, no longer have to be done by hand.
At the same time, data-based processes increase flexibility. Finishing 4.0 solutions compete with the claim to produce error-free from the very first copy – and thus to reduce to a minimum the expensive rejects of the already printed, cut and finished intermediate products at the end of the 4.0 process chain.
But this only covers part of the novel structures. In the background, sensors along the process chain continuously collect machine and production data. Some of this data is processed decentrally and cost-efficiently with edge computers close to the production line in order to feed the information obtained back to the control and regulation systems in the process without any loss of time. The larger, less time-critical part of the data flows into the cloud for further use and now increasingly AI-supported analysis.
Analogous to this vertically integrated data chain, horizontal integration ensures close organizational networking of the players along the value chain. This allows previously separate competencies and know-how to be brought together. Users, suppliers of production hardware and software, developers of a wide variety of substrates and consumables, and research institutes form cooperation networks to jointly further develop print and packaging technologies and process chains and better align their respective products and processes. In addition, data integration and networking create the necessary transparency for efficient recycling and longer machine service lives, for proactive maintenance, refurbishing – and thus for the transition to the circular economy.
Last but not least, horizontal integration paves the way for simplified digital order processing, accounting, costing, personnel and order planning, benchmarking, inventory management and much more.
A final important aspect concerns the operation and service of print, packaging and finishing technologies. As the database continues to grow, the effort required to integrate new human-machine interfaces (HMI) and workflow solutions is decreasing. Via smartphone or tablet, operators, service specialists, production planners and managers can access current machine and production data at any time. They carry the control station of the smart process chain with them at all times. Whether it’s troubleshooting or planning maintenance and repairs; an overview of spare parts, consumables and operating material availability; documentation; track and trace functions or forwarding printed rolls and sheets to finishers and postpress – in the process world of Print, Packaging and Finishing 4.0, all that’s needed for manufacturing execution is the mobile device in a pocket. This also is an effective antidote to unproductive downtime in analog, highly segmented production.
Meanwhile, the trend is toward HMI solutions that support operators and assemblers in maintenance procedures and repairs via augmented, mixed or virtual reality (AR/MR,VR). Especially where skilled workers are scarce, this use of data and digital networking also opens up potential for a highly productive print and packaging world of the future.
Source: Messe Düsseldorf. For further information about drupa 2024, contact Messe Düsseldorf North America; telephone: 312.781.5180; email: info@mdna.com; visit www.drupa.com.