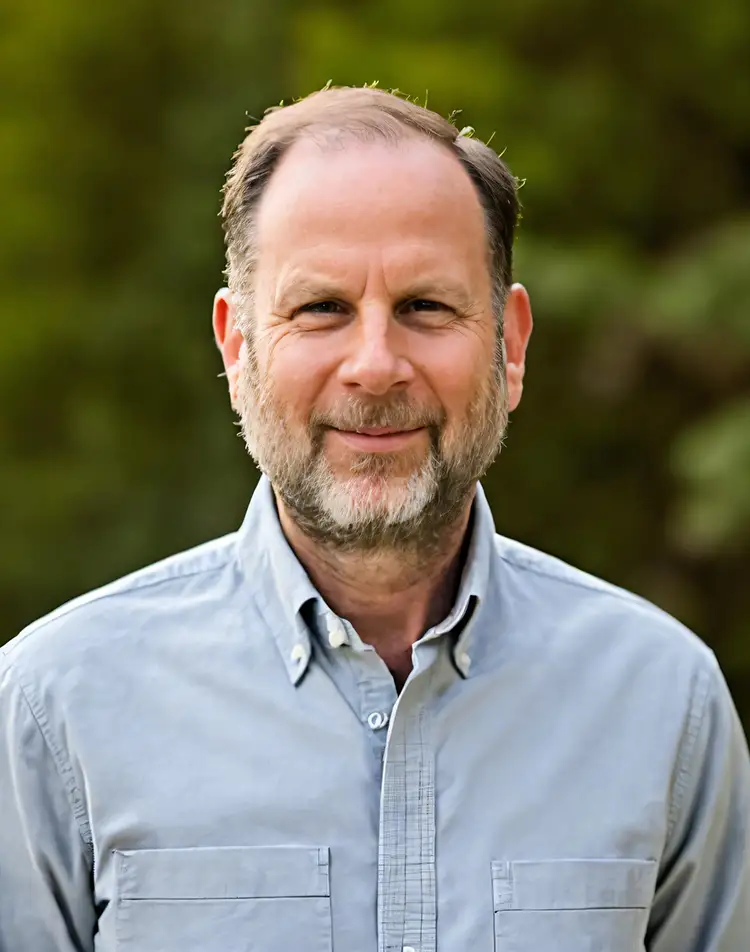
Gary Cohen is the executive director of RadTech International North America, a trade association devoted to promoting the use and development of ultraviolet (UV) and electron beam (EB) processing as an industrial technique offering energy savings, elimination of pollution, greater productivity, higher yields and the opportunity for improved, new or unique products. The association serves as an international forum and reliable source of education and information for individuals and organizations involved in the use of UV and EB processing or who supply equipment, chemicals or other materials to such users. With a background that includes work at the US International Trade Commission, Cohen is focused on supporting US manufacturing across a wide variety of industries, including print and packaging.
How did your career develop into your involvement with RadTech North America and the UV and EB curing industries?
I was born and raised in the Washington DC area – so, way too many lawyers and lobbyists concerned about politics. I started out at the US International Trade Commission looking at imports to the US that may be unfairly harming US industry. From that time on, my work always has focused on manufacturing, with subsequent positions at the Association for Manufacturing Technology and the Consumer Electronics Association / Consumer Electronics Show. That broad manufacturing perspective, focused on technology users, seemed to be a good fit for RadTech as UV/EB has so many applications across industries.
How do you see the industry embracing global trends, such as the circular economy and sustainability demands from manufacturers, brand owners and consumers?
The UV/EB industry is all in on circular economy and sustainability. In fact, it is members who encouraged us to tag our 2024 biennial event as UV/EB for Sustainable and Responsible Manufacturing. Over the years, our industry had grown a bit frustrated as we always have offered low to no VOC, CO2 and Hazardous Air Pollution solutions, but it was difficult for many companies to make the investment to change their processes. Moving to UV/EB means not just changing equipment, but also much of the process. Many of our members used to say that our real job was “changing mindsets” to get the word out about the various operational benefits of UV/EB that come with a more sustainable process.
What are the biggest challenges the UV, UV LED and EB curing industries are facing? How should the industry respond to successfully grow and thrive?
Understandably, it is hard for many manufacturers to make major changes to their processes. In some instances, companies have been running successfully for generations with their equipment, and change always comes with some perceived level of risk. The challenge of the UV/EB industry is to demonstrate not only the benefits of the technology, but that the technology may be implemented seamlessly
and easily.
As we are seeing federal and state regulations pop up around sustainability, UV/EB sometimes are excluded by regulators as they are not familiar with the technology and/or may have heard some misconceptions. Education is the key opportunity for our industry.
What trends are emerging in design and production that will influence the future of the UV, UV LED and EB curing industry? How do you believe this will affect the printing and packaging industries?
With increased computing power and artificial intelligence (AI) design programs, the ideas we have been talking about for years, such as mass customization, are becoming a reality. This technology is perfect to implement for inkjet, customization, direct to object and special effects. UV/EB offer nearly infinite tuning and precise curing.
Which markets/verticals are growing their use of UV, UV LED and EB curing technologies?
The graphic arts industries are by far the largest segment for UV/EB in North America. UV/EB seems to be accelerating its growth in food packaging and all types of printing, offering safe, sustainable solutions to printers for a range of substrates. That includes metal can decorating and coatings, and coatings and decorations for various flooring and wall covering applications.
While sustainability certainly is a driver to the growth of the technology, the main driver for UV/EB always has been the fact that it is an “enabling” technology, offering enhanced capabilities to print, coat and adhere on a wide range of substrates that may not be practically done in any other way. In addition to the environmental benefits, the hyper-speed (UV/EB cure nearly instantly, in most cases, with products ready for pack and ship immediately), increased capabilities to make new products and the efficiency of the UV/EB processes offer manufacturers real opportunities to benefit their bottom line.
What are your predictions for the UV/EB industry in the next five to 10 years?
I have been in the UV/EB industry for a long time, and part of the reason is because the technology and applications are rapidly evolving, making me very fortunate to be involved with this exciting technology. Big, amazing surprises about new applications and processes almost are a certainty, if the past is any indicator.
If the emphasis on energy savings, CO2 emissions and sustainability continues, the outlook for this technology is very exciting. In many cases, I am not sure there is any better way to meet such enviro-goals while enhancing product and process performance.