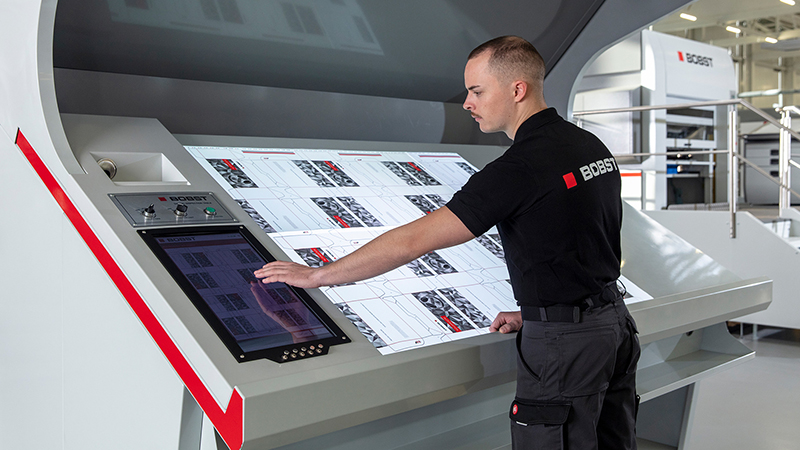
Switzerland-based BOBST, a supplier of substrate processing, printing and converting equipment, and services, has launched oneINSPECTION. An integrated and evolving set of quality control solutions to proactively meet the needs of brand owners and converters, it makes zero-fault packaging a reality in the labels, flexible packaging, folding carton and corrugated board industries. The new quality control also will provide significant value to packers, retailers and consumers as part of the packaging value chain.
oneINSPECTION ensures an end-to-end data-driven quality process specifically tailored for each industry, which can be deployed in both new and existing production lines. It is a core enabler of the BOBST vision to shape the future of the packaging world and a core component of BOBST CONNECT – an open architecture cloud-based platform delivering solutions for prepress, production, process optimization, maintenance and market access.
The current solutions for each industry are as follows:
Labels
- Print Tutor Max – a system specifically designed to measure and control color for DigiColor.
- iQ 500 – a 100% inline quality control system checking each individual label for quality, color, codes, text and register.
- Flexible Packaging
- HAWKEYE – an optical density and pinhole detector monitoring system.
- Digital Inspection Table – a quality center that enhances the operator’s skills with augmented reality overlays while gathering photographic evidence for audit; ensuring trust and top production quality for flexible packaging production.
Folding carton
- New ACCUCHECK – a 100% inline quality control system checking each individual blank for quality, color, codes, text and register.
- iQ 400 – a 100% inline quality control system for web-fed folding carton production.
Corrugated board
- iQ 300 – a 100% inline quality control system for corrugated production.
- Premium gap control – a system controlling the folding process of all finished boxes at full production speed.
- Digital inspection table – a quality center that enhances the operator’s skills with augmented reality overlays while gathering photographic evidence for audit; ensuring trust and top production quality for corrugated packaging production.
These solutions provide data-driven quality control processes, eliminating human errors. They offer digital reporting for quality tracking, and unique and robust image processing algorithms for perfect inspection. They also provide new capacities, such as:
- machine learning, available on the New ACCUCHECK and iQ 500 systems, which enables easier and faster machine setup;
- accurate proprietary PDF functions, developed on the iQ 500, which allow precise conformity checks and shorter setup times;
- optimized overall production, thanks to close-loop functionalities with the HAWKEYE and the Print Tutor Max, which guarantee quality and maintain a high level of productivity;
- increasing connectivity and workflow integration for fact-based decision making, e.g. OEE statistics on the New ACCUCHECK and iQ 500 products.
For converters, oneINSPECTION means complete peace of mind, enabling them to deliver the highest possible quality products to brand owners, while simultaneously improving efficiency and profitability. It puts guaranteed quality control at their fingertips, making zero-fault packaging a reality.
For more information, visit www.bobst.com.