Press release submitted on behalf of Konica Minolta
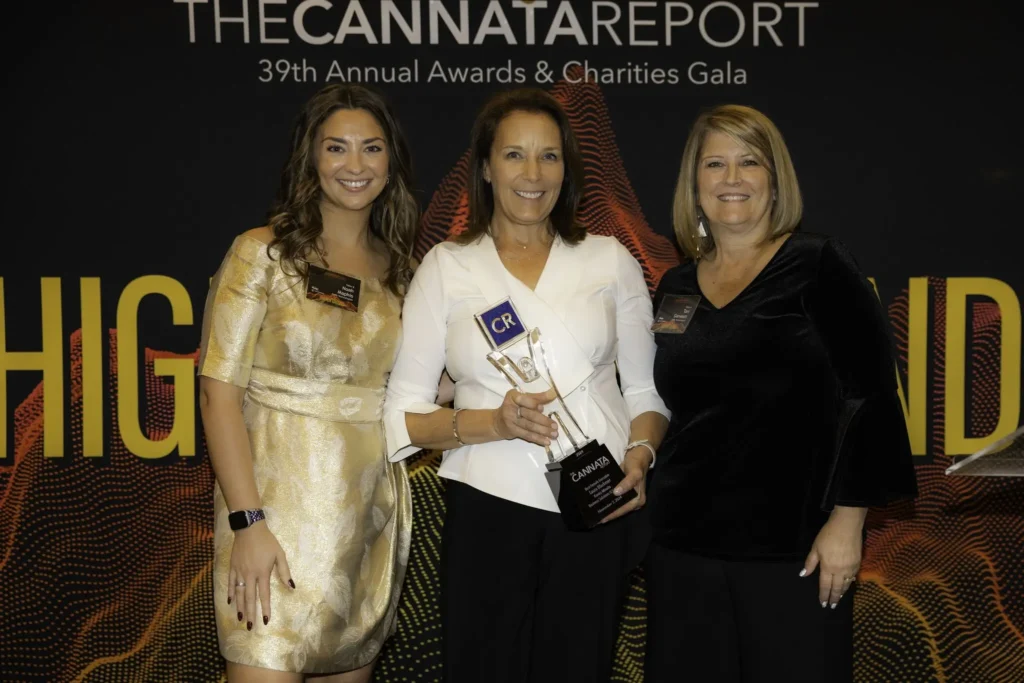
Konica Minolta Business Solutions U.S.A., Inc. (Konica Minolta), Ramsey, New Jersey, is pleased to announce Laura Blackmer, President, Dealer Sales, has received the 2024 Frank Award for “Best Female Executive.”
The Frank Awards recognize outstanding achievements and excellence in the independent dealer channel of the office technology industry. This is the eighth time Blackmer has received this distinction. Toni Gorveatt and Noah Maphis of Cobb Technologies presented the award to Blackmer during The Cannata Report’s annual gala on November 7.
“It was a delight to have again received this accolade, I am always humbled by this award since it is open to all dealers. I truly appreciate their support and have enjoyed my relationships within this community,” said Blackmer. “I am grateful to The Cannata Report for not only recognizing women in leadership roles with this award category, but also the importance they place on female executives through their Women Influencers program.”
“Laura Blackmer’s recognition as Best Female Executive reflects the deep respect and appreciation she has earned from dealers across the channel,” said CJ Cannata, President and CEO, The Cannata Report. “Her dedication, approachability and communication skills set her apart as one of the most highly esteemed leaders in the industry, and her multiple wins demonstrate her remarkable influence and unwavering commitment to dealer success.”
The Cannata Report’s annual gala raised funds for research led by Rena Feinman, Ph.D., Associate Member of the Center for Discovery and Innovation at Hackensack Meridian Health, seeking to improve response to anticancer therapies for breast cancer patients.
See the full list of 2024 Frank Award winners online.
About Konica Minolta
Konica Minolta Business Solutions U.S.A., Inc.’s (Konica Minolta) journey started 150 years ago, with a vision to see and do things differently. The company innovates for the good of society and the world. The same purpose that kept it moving then, keeps it moving now. Konica Minolta aims to partner with clients to Give Shape to Ideas by supporting their digital transformation through its expansive Intelligent Connected Workplace portfolio. Its business technology offerings include IT Services, intelligent information management, video security solutions and managed print services, as well as office technology and industrial and commercial print solutions. Through its ongoing work, the company is fortunate to be continuously recognized for its products and services. This includes, but is not limited to being included on CRN’s MSP 500 list numerous times; named a finalist in the IT Software Category by The World Technology Awards; recognized as the #1 Brand for Customer Loyalty in the MFP Office Copier Market by Brand Keys and presented with Keypoint Intelligence’s BLI 2021 A3 Line of The Year and BLI 2021-2023 Most Color Consistent A3 Brand Awards for its bizhub i-Series. For more information, please visit Konica Minolta online and follow its account on Facebook, YouTube, LinkedIn and Twitter.
About The Cannata Report
The Cannata Report is the leading intelligence resource for the document imaging channel in the office technology industry, covering a range of topics, including managed IT solutions, managed print services, digital transformation, cybersecurity, cloud communications, network security, production print, services and supplies, vendor finance, mergers and acquisitions, and more. Written specifically for the independent dealer channel, The Cannata Report, founded in 1982, has an audience that includes business leaders in the office technology industry’s hardware, software, IT, leasing, and supplies segments.