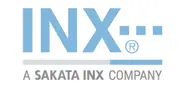
Press release submitted on behalf of INX International
INX International Ink Co., Schaumburg, Illinois, has completed a venture capital investment in AssetWatch, a leading condition monitoring and predictive maintenance organization based in Columbus, Ohio. INX participated in AssetWatch’s $40M Series B round of financing which was led by Wellington Management. AssetWatch represents the sixth investment completed thus far via INX’s $50M corporate VC program established in 2022.
AssetWatch provides end-to-end remote condition monitoring solutions for industrial rotating equipment to reduce downtime. The company uses sensors and AI-backed, cloud-based software to detect and resolve equipment issues, augmented by best-in-class service and prescriptive insights delivered by certified condition monitoring engineers.
“AssetWatch delivers predictive insights which are accelerating INX’s “Plant of the Future” initiative,” says Shane Bertsch, Senior Vice President of Innovation & Strategy. “AssetWatch is a progressive company that is helping to enhance our operational efficiency and ensure the safety and reliability of equipment and products at INX facilities around the world.
“With a real-time centralized view for our manufacturing plants, we can detect and resolve issues, note the proactive impact across the company, and continuously learn for future improvement,” he explained. “Their predictive maintenance programs prevent unplanned asset failures, improving production capacity and product consistency.”
After completing a successful pilot in 2024, INX has now implemented AssetWatch at four manufacturing facilities in the United States. Moving forward, INX plans to roll out the solution across all facilities in North America says Chris Rodgers, Corporate Director of Operational Excellence.
“AssetWatch has been a great help to the maintenance staff in finding equipment related issues before they become breakdowns, and scheduling repairs to minimize interference with manufacturing schedules. AssetWatch has diagnosed issues and provided insights that have allowed us to make repairs and improvements that extend the useful life of the equipment and increase the uptime of the facility.”
Brian Graham, AssetWatch’s CEO commented, “We are excited to have INX as a strategic investor and commercial partner. The investment demonstrates INX’s commitment to digital transformation and sustainability, and we are eager to demonstrate ROI and an ability to transform maintenance and reliability from a reactive to proactive discipline across all INX facilities in North America.”
About AssetWatch
AssetWatch is a leader in predictive maintenance solutions, providing a rapidly deployable, end-to-end remote condition monitoring service. Their solutions eliminate unplanned downtime and optimize operations for global manufacturers by simplifying the predictive maintenance process through a network of wireless sensors and communication hubs, cutting-edge software, and condition monitoring engineers. By combining an AI-powered risk engine with the predictive insights of a certified expert, AssetWatch gives more than just the standard “pass/fail”. They truly are a partner in the journey, helping change the culture of maintenance and reliability teams from reactive to proactive.
INX International Ink Co.
INX International Ink Co. is the third largest producer of inks and coatings in North America, with full-service subsidiaries in Europe and South America and is part of SAKATA INX worldwide operations. We offer a complete line of ink and coating solutions technology for commercial, packaging and digital applications. As a leading global manufacturer of inkjet inks, we provide a full palette of digital ink systems, advanced technologies and integrated services. Stay updated on the latest developments and follow INX on LinkedIn, Facebook, and X, or visit www.inxinternational.com.