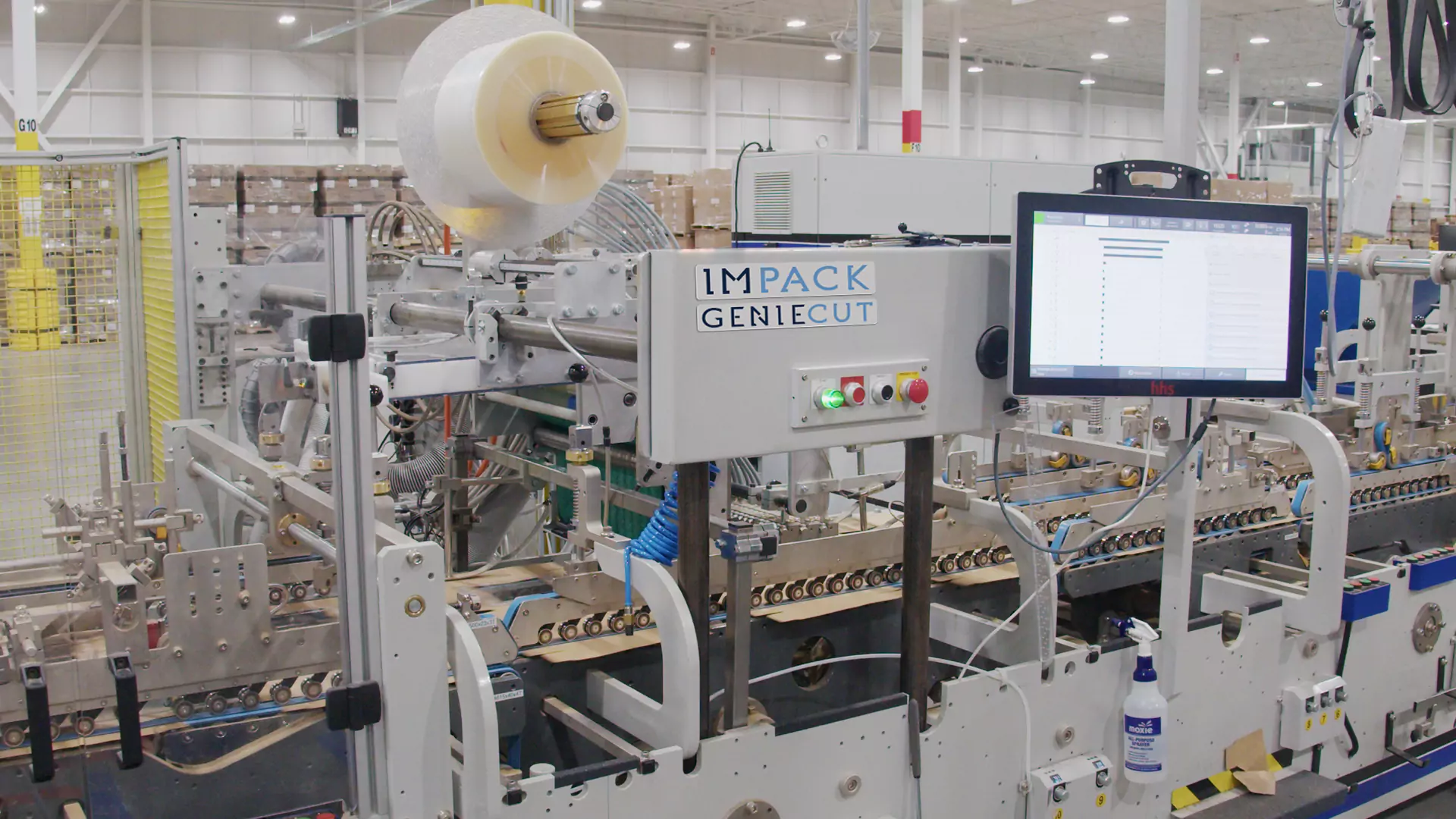
Press release submitted on behalf of GenieCut
IMPACK, a pioneer in machinery solutions for the carton packaging industry, is thrilled to introduce the GenieCut, an in-line window patcher designed to redefine carton windowing. On August 16, 2023, IMPACK completed the acquisition of the GenieCut and formed a partnership with inventor Jeff Shaffer.
“With already 25 installations running across North America and the UK, the GenieCut is a tested and proven concept! It integrates directly onto the folder-gluer and it is a game-changer for businesses looking to optimize their operational area and provide additional packaging options to their customers using their current folder-gluer production line.” – Mathieu Tremblay, Deputy General Manager
Compact & In-line
With the GenieCut, packaging producers can offer window patching as a new service to existing customers, or modernize and streamline their current window application process. The GenieCut’s revolutionary technology introduces a significant paradigm shift in terms of speed, functionality, flexibility and efficiency. One of the GenieCut’s standout features is its compact design, which provides the same functionality as larger competing systems while taking up virtually no additional floor space.
Inspiration for Innovation
Jeff Shaffer, inventor of GenieCut, explained the inspiration for this new approach to window application: “Over the years, as a production manager on a folder-gluer line, I saw many ways that the outdated window patching technology could be improved. In the 1930’s a windowing machine was introduced that utilized a timed feeder, chain register, glue pot, printed glue pattern and a knife-to-anvil crosscut of the film. Nearly 100 years later, conceptually nothing much had changed…. until now. The GenieCut is a simple, low-maintenance design that promises years of easy operation with less waste and down time.”
Paradigm Shift in Window Application
This cutting-edge technology further increases productivity by significantly reducing, well, everything else – training time, set up time, cleaning time, and maintenance. How so? The GenieCut boasts a simplified, streamlined mechanism. It has removed unnecessary complexity, making it easier to operate and maintain. Many of the details you’re used to seeing on traditional window patchers simply don’t exist. The GenieCut does not have a glue pot, glue stencils or cylinders that need to be changed, customized or removed for cleaning. While standard window patchers can take 3 to 4 hours to set up, the GenieCut usually takes less than 15 minutes to set up when recalling an existing job. Since it does not interfere with or come in contact with the folder-gluer, the GenieCut can be maintained or prepared for a future windowing batch while the folder-gluer is processing windowless boxes. While traditional window patchers require fairly frequent blade replacements due to their knife and anvil cutting system, the GenieCut uses a patented stationary knife film cutting system.
Designed with the Operator in Mind
Speaking on the improved operator experience Jeff says, “The GenieCut is the most user-friendly window machine on the market! No prior window machine experience is necessary. With some basic knowledge of any adhesive extrusion system, operators already know how to run this machine.” This is a significant improvement over other leading machines, allowing businesses to achieve faster time-to-value.
IMPACK and Baumer hhs: Joining Forces, Creating Bonds
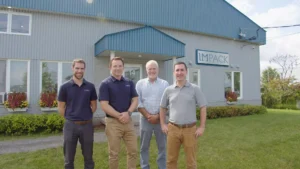
The GenieCut window applicator system features a specialized state-of-the-art glue system capable of feeding 60 glue guns or more. To accelerate customer return on investment, IMPACK and Baumer hhs offer optional glue gun modules for the GenieCut so that customers can select the smallest module that meets production needs. The glue gun modules come in standard widths of 6, 9, 12, or 15 inches and 18 inches for specialized productions. The glue system comes standard with an intuitive and user-friendly Baumer hhs touchscreen controller that allows operators to define precise glue patterns. Each dot of glue is 6.2mm center to center, adjusting the glue volume ensures an unbroken glue pattern once the film patch is placed. Film and glue patterns are stored in the controller reducing machine changeover from hours to minutes.
The New Benchmark for In-line Window Application
GenieCut sets a new benchmark for operational efficiency, outpacing other in-line and offline one-lane window patchers. Traditional window patchers have servo motors that need to “home” before cycling again, but the GenieCut design allows it to cycle continuously, so it can cut the film over 15 times a second. The maximum speed of the machine components is 200 meters per minute. With this high-speed window patcher, optimized folder-gluer lines can expect to achieve actual production times of up to 150 meters per minute or 15,000-40,000 boxes per hour depending on blank size. The GenieCut is capable of countless window patch widths on corrugated or carton straight-line, 4 corner, 6 corner, and crash-Lock boxes.
The Perfect Fit
“Sometimes, you encounter a new innovation and think, ‘This is ingenious; I wish I had come up with this idea.’ That’s precisely what crossed our minds the first time we laid eyes on GenieCut! The GenieCut fits into our product portfolio seamlessly, much like a missing puzzle piece. Like all of our products, the GenieCut is designed to improve functionality and productivity of folder-gluer machines and has the potential to help every single one of our customers be more competitive in the global market. Like IMPACK’s other patented products, GenieCut is a game-changer and is poised to become the new benchmark for in-line window applications.” – Dominic Theriault, President & CEO
Jeff adds: “I’m excited to be working in collaboration with IMPACK. With their many years of engineering excellence and quality manufacturing, they are in a position to take the GenieCut to the next level and bring it to folder-gluer producers around the world.”
For more information about this revolutionary in-line window patcher or to talk to an expert about your specific needs, please visit the GenieCut webpage on our website and fill out the form.