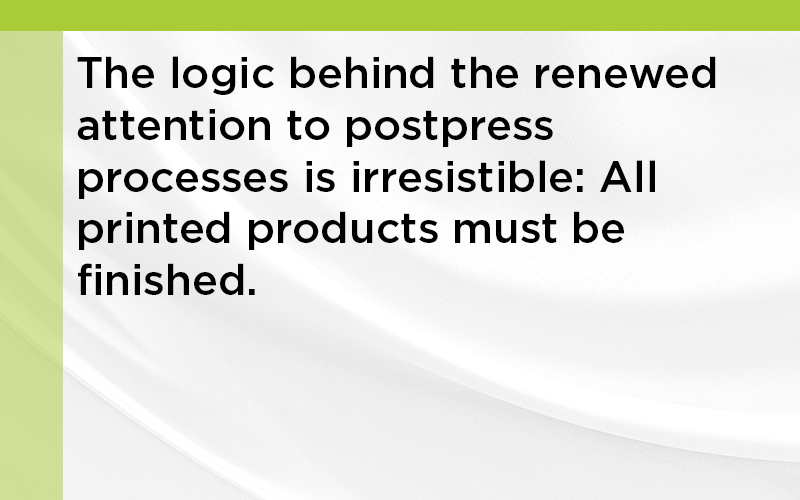
by: Larry Tanowitz
Postpress No Longer an “Also-Ran”
Until relatively recently, the graphic arts industry has compartmentalized its thinking about process management. For years, talk of “seamless” integration stopped at the delivery end of the press, just short of the bindery. That thinking has been replaced by the understanding that printed products are only as good as the processes that tie up their loose ends efficiently. Driving developments beyond automation and toward postpress process integration is the need to get reliable information to the bindery in a useable format. In fact, much bindery equipment already can gather, report and store job-specific data. The key elements of an integrated postpress workflow include the following:
- Improved interface between prepress, press, and finishing equipment
- Centralized control of bindery components
- Automated setup
- Storage of previous job parameters
- Faster makeready to increase net output per shift
- Quick turnaround
- Faster job changeover
- Ability to monitor operational and materials costs via data collection and analysis
- Minimal operator intervention
- Process reliability and consistency
- Higher efficiency
- Productivity gains
- Enhanced flexibility
- Reduced material costs
- Reduced labor
- Reduced waste and spoilage
- Reduced downtime
- Improved load balancing with fewer scheduling conflicts
- Streamlined material handling
Printing Begins with Postpress
The logic behind the renewed attention to postpress processes is irresistible: All printed products must be finished. As a critical determinant of the materials and processes selected for production, finishing is a key differentiator of quality after the press. Poor choices made in the product planning stages have the potential to compromise the quality of the bound and finished job, especially if it contains complex cuts or folds, or uses inks or coatings that are difficult to handle.
Despite the need for an unrestricted flow of data between a plant’s business and production functions, many printers still conceive of the bindery as discrete from the rest of the shop. Even in plants where MIS, prepress, and press processes are networked, the bindery too often is perceived as an island unto itself.
While it is true that computer-integrated manufacturing has eliminated many traditional bottlenecks in prepress and press production, the ability to tie postpress functionality into the system as a whole has been elusive. Despite much lip service paid to the need for so-called “end-to-end” integration, however, the discussion – until recently – has largely excluded the bindery. There are a number of reasons for this:
- Postpress processes tend to resist computer-enabled efficiency. Finishing often requires manual labor and generates waste.
- Finishing must resolve an accumulation of variables including paper weight, bulk, moisture and so on, whose effect on the final product can be hard to predict and often require manual correction.
- The time unbound sheets spend in the bindery prior to finishing, and the need for fine handwork on some projects can slow production to a crawl.
- Lack of skilled personnel in the bindery sector is acute.
Many companies hire unskilled temporary workers to fill vacancies there. At the same time, there are no real trade school or journeyman programs geared specifically for bindery employees. Integrated solutions must be sophisticated and capable, yet simple and accessible.
The sheer durability of postpress equipment functions as a disincentive to capital investment for many printers, who treat the bindery as an afterthought last in their capital investment plans.
According to NAPL, for example, just 16.2 percent of print businesses surveyed for its most recent “State of the Industry” report said they expected the demand for finishing/bindery services to be the fastest growing, compared with a host of other products and service specialties.
TrendWatch Graphic Arts reported earlier this year that 10 percent of digital printers plan to invest in bindery/finishing equipment, compared with just 3 percent of print and prepress firms overall.
In fact, computer-enabled automation is a prerequisite for an integrated bindery – so much so, that the longevity of heavy-duty bindery equipment may no longer be an asset if it deters a printer from pursuing a much-needed upgrade. The reality is that the older the equipment is, the harder it will be to integrate. If it is automated, older bindery equipment is already CIP 3/4-PPF-compatible, meaning that machines can receive and collect prepress data without also having the ability to transmit setup and production data back upstream. Whether legacy equipment can be modified to accept CIP3/4 presets, however, will depend on the type, age and degree of automation of the equipment in question. Consider the following:
- Older machines may be only partly automated, or not at all
- Many older machines cannot be retrofitted to take advantage of computerized presets
- Older machines take longer to set up, run more slowly, and require more operator adjustment – all drains on time, manpower, and other resources or factors at odds with the shift in emphasis from price to cost and the pressure to provide short runs at high volumes.
Consequently, flexible equipment should be installed now as a hedge against being caught behind the rapidly escalating technological curve. If a postpress upgrade isn’t in the cards, even an old folder can be productive when paired with advanced press equipment. Another solution may be to semi-integrate older equipment with the aid of off-line, computer-aided programs.
All of the Above
Failure to view the components of a print manufacturing workflow as a single, interdependent system that encompasses the bindery reflects the industry’s painfully slow adoption of CIM. According to a recent report by TrendWatch Graphic Arts, between fall 2003 and spring 2004, the percentage of printing firms who are challenged by “implementing the SmartFactory, CIM concept” slipped from 3 percent to 2 percent, even as “understanding the SmartFactory, CIM concept” remained steady at 5 percent. Furthermore, while 32 percent of print businesses acknowledged “reading about/studying CIM,” the same percentage also indicated that “CIM is not relevant to our business.”
Much of the resistance is economic: CIM can involve new equipment, new employees, and a potentially expensive learning curve. Some is psychological: many printers, already slow to evolve, are overwhelmed by the concept, and this has tended to blunt, not whet, their motivation to embrace change. This is especially true of the bindery, which still functions as a loss leader in many shops, yet upon whose shoulders the burden of productivity ultimately rests.
However, for printers who educate themselves about the potential benefits of integration, who are willing and able to make the necessary capital investment, and who are prepared to work closely with suppliers to maximize the return on their investment, connectivity is possible now. The tools needed to construct a postpress workflow that can participate in the growth of productivity plant-wide already are available.
Implementing an Integrated Postpress Workflow
In an ideal world, all bindery equipment would be perfectly matched in terms of speed, flexibility and control with every printing press. Machines designed to handle the output from traditional offset presses would function equally well in digital and direct imaging environments, unaffected by format, substrate or volume limitations. Bindery setup and makeready would accurately mirror the speed of the press and the size of the print run. To say that these efficiencies are not universally available or are not being taken advantage of fully, is not to denigrate the advances that have been made, nor to minimize the importance of investing in postpress technologies that can adapt to changing requirements. Instead, the opposite is true: the newest postpress innovations present more opportunities than ever for print shops to specialize and stand out from the competition.