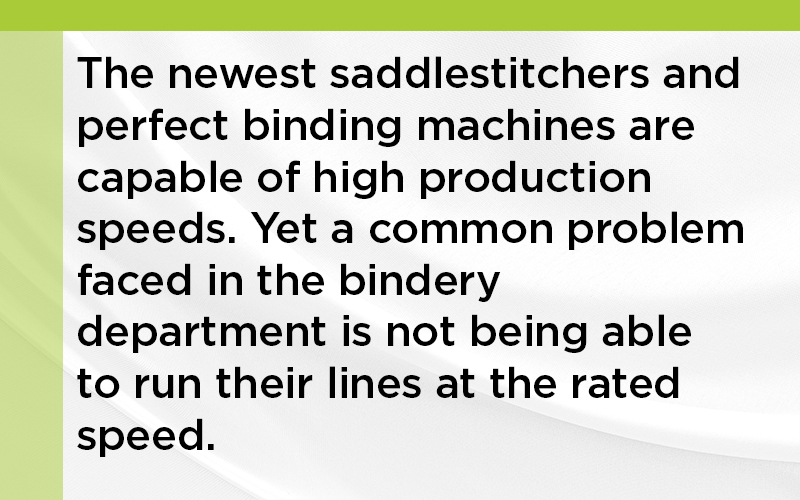
by: By Ken Troemel, Andy Grzesik, and Mark Blitshteyn, MKS Ion Industrial
The newest saddlestitchers and perfect binding machines are capable of high production speeds. Yet a common problem faced in the bindery department is not being able to run their lines at the rated speed.
Incline Stack Tacking Challenges
One of the bottlenecks in the bindery is compensating stackers. There, the magazines are conveyed by the belts up the stacker and dropped into the compensator where they are stacked to varying heights to meet postal routing specifications.
To keep up with the high speed of upstream equipment, the magazines have to be pushed out of the compensator quickly. This process causes some magazines and catalogs to shift, resulting in uneven stacks of shrink-wrapped books. The USPS can reject the defective stacks, which forces the bindery to separate and re-run the magazines off-line. While many outstanding innovations have been introduced to assemble neat square stacks, when the stack is pushed out to be transported through the shrink wrap tunnel or other packaging, the mechanical forces that kept the stack straight are no longer present.
Oval strappers are sometimes utilized after the stack is pushed out of the stacker. The strapper has become less desirable as the post office needs to route individual magazines to their destinations. Additional detractors are strapper maintenance and downtime.
Magazines with UV-coated covers, either perfect bound or saddlestitched, have very glossy slippery surfaces, which make them vulnerable to shifting when stacked. High page count saddlestitched magazines create challenges because the spine side is thicker than the open side. This could cause the books to slide over to the open side and potentially shingle as they exit the compensator.
If the stacker does not produce neat, true stacks, either the entire line will have to slow down, regardless of faster bindery equipment upstream, or operators will need to be added at the output of the line to manually straighten the stacks.
Electrostatic Stack-Tacking
What is difficult to accomplish by mechanical means could be done with electrostatics. Electrostatic forces of attraction can hold magazines in the stack, preserving the perfect shape achieved by advanced compensating stackers.
There are two practical electrostatic system configurations that could be employed in the stackers. One arrangement is known as cross-tacking. It employs three charging bars inside a compensating stacker. When a stack is assembled, two separate plates hold the stack from each side and the third plate comes down and squeezes the top of the stack. The charging bars in each plate are energized; the electrostatic field and ionization tack the magazines together and keep them from shifting. Cross-tacking is the only electrostatic option for magazines conveyed by the belts up the stacker in a shingled stream.
Cross-tacking systems cannot be retrofit in existing stackers; they have to be designed in by the manufacturer of the stacker. The cross-tacking systems are complex and expensive, requiring three charging bars, special insulating plates to hold charging bars in place, and other special design features. Since cross-tacking systems usually come installed and properly engineered, binders do not need to do much to have them provide solid stacks.
Compensating stackers not designed for cross-tacking systems and which receive the magazines singly, can be retrofit with an electrostatic system in the incline feeder section. These are known as incline-tacking systems. Since different types of equipment can be utilized for incline electrostatic tacking systems, a printer needs to know how the system functions, how to select the charging equipment, and how to maintain it.
Electrostatic Tacking in the Incline Feeder
Incline tacking systems typically use a pair of charging bars, one placed above the magazine’s path into the stacker, the other below. The ionizing pin electrodes of the two bars are generally aligned against each other. The positive polarity voltage is applied to one bar and the negative to the other from a pair of high-voltage charging generators or from a single generator with dual-polarity outputs. The distance between the bars should generally be 2″ or less. The smaller the bar gap, the lower the voltage required to generate a sufficient tacking effect.
When the bars are energized with no magazines in the incline feeder, the opposite-polarity air ions produced by the opposed bars will stream toward each other, completing the electrical circuit. When magazines are being fed up the incline, they interrupt the flow of ions between the bars. The ions deposit on both sides of the magazines, charging each surface opposite in polarity, as shown in Figure 1 (page 22). Magazines carry these charges away, in the form of a “convection” electrical current, again completing the electrical circuit.
The immediate effect of the charging is that the magazines “tighten up” and are held closed shut by the electrostatic force between the front and back cover pages. The air gets squeezed out from between the pages. While that certainly contributes to forming a neat integral stack, it is the secondary effect that is most important. When a charged magazine is dropped into the stacker, it lands with its back cover on the front cover of the previous magazine. Opposing charges on the back and cover pages of the two magazines create an attraction between them, causing the books to adhere to each other, as shown in Figure 2 (above). That attraction will keep the magazines from shifting when the stack is in motion.
Selecting and Using Electrostatic Systems in the Incline Feeders
Step 1. Install nonconductive belts to avoid arcing from the bars to the belts.
Step 2. Install charging bars with the effective lengths 1″ shorter than the most common height of the magazines you run on the stacker.
The ions from the correctly sized bars deposit on both sides of the book, charging its surfaces, as shown in Figure 3 (page 26), without the problematic discharge around the side edges of the magazines.
IMPORTANT: If the bars are too long, extending beyond the edges of the magazine, a high portion of the charging current is flowing through the air between the bars at both ends. The ends of the bar could overheat, causing the bars to burn out.
Step 3. Adjust the output of the charging generator to achieve optimal tacking confirmed by the square bundles coming out of the shrink-wrap tunnel. Notice the charging current value, because the electrostatic pinning force is determined primarily by the value of the charging current, not the voltage.
Because the magazine surface can carry only a limited amount of charge, the total current between the bars drops down to one-third of the current between the unobstructed bars (the actual value depends on the magazines size and thickness, and the type of paper, the coating, and the ink). For example, if the current between two unobstructed charging bars is 1 milliampere, the current would drop to 0.3-0.4 milliampere when a magazine is passing between the bars.
Such current fluctuations repeat with the current going up after the magazine passes through, and going down after the next book comes in between the bars. While it’s possible to see some fluctuations in the current meter, charging generators are not capable of showing such fast changes, as the current goes up, down and up again in 0.1 second’s time on the fastest stackers.
The most effective operation can be obtained with charging generators featuring a constant current (CC) mode. In the constant current mode, the generator automatically adjusts the voltage to maintain the preset current. In this mode, the system maintains stable and strong pinning power adjusting output down when there is open space between the magazines, and also offsetting changes in the line speeds, ambient conditions, or paper dust buildup on the ionizing electrodes.
IMPORTANT: Effective control of the pinning process is possible only when the bars do not extend beyond the edges of the magazines – see Step 2. With long bars, the current flowing directly between the bars is not contributing to the tacking process. Under such conditions the monitored current value is nearly meaningless.
Step 4. Keep the ionizing electrodes sharp.
Electrodes of the positive charging bars wear out 3-4 times faster than the electrodes of the negative bars. There are three methods for keeping electrodes sharp:
- Use tungsten pin electrodes.
- Use replaceable pin electrodes.
- Increase the number of pin electrodes to spread the current over a larger number of electrodes and reduce the current density for each electrode.
Step 5. Keep the ionizing electrodes clean.
Paper dust should not be allowed to build up or cover the electrodes. Clean the charging bars often. Use a metal brush to scrub through the electrode channel during makeready. That especially becomes a problem with overly long bars, because the ends of the bars will be collecting excessive amounts of paper dust falling on the electrodes from the sides of the magazines.
Ken Troemel, Andy Grzesik, and Mark Blitshteyn of MKS Ion Industrial share a two-part series with readers. They explain how to create effective electrostatic solutions for various printing and converting problems. The authors have many years of combined experience in creating effective electrostatic solutions for various printing and converting applications, working for Tantec Inc. and later for MKS Ion Industrial. In 2006, Tantec USA became a part of the Ion Industrial product group formed to service the paper and film converting and plastics industries in 1997. For additional information on MKS Ion Industrial, visit www.mksinst.com/ion-industrial.