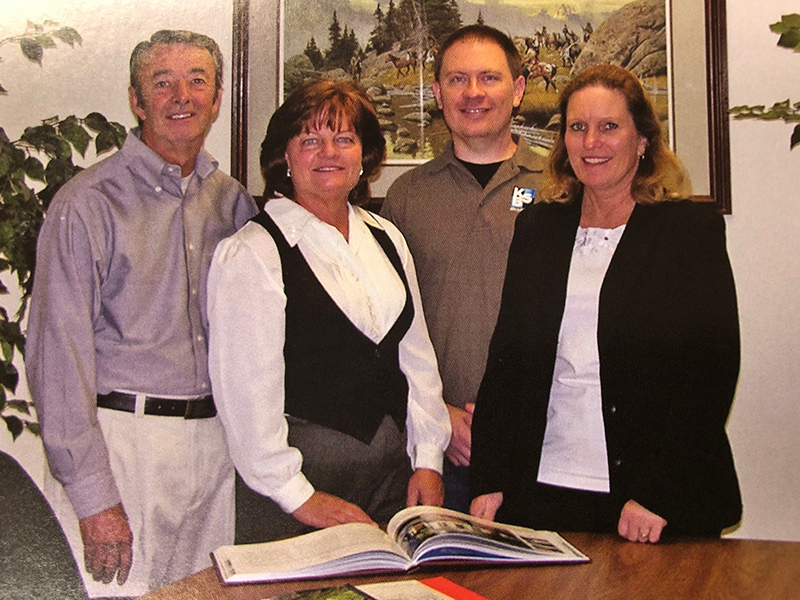
by Melissa DeDonder, The Binding Edge
Your Bindery Finishing was created from humble beginnings, inside the two-car garage of Luann and Curtis Wood, in Denver, Colorado. Luann, president of the company, had spent the previous 10 years working in prepress and operating a small press, and then she went to work for her grandfather’s family business, which sold presses and bindery equipment. “I enjoyed finishing the final product rather than running a press, and I liked the idea of running my own company, so my husband and I started Your Bindery Finishing in 1986,” she said.
The company began with minimal equipment [- a friction collator/bookletmaker, three-head spindle drill, table top folder and a small 25″ cutter. “In those early years, my mother worked as our outside sales representative, and our son helped out by working after school,” Wood said. In 1992, Wood’s youngest sister, Kirsten Hunt, joined the team.
By working many long hours and providing the local printers with a top-quality product and quick turnaround, in three short years Your Bindery Finishing outgrew its 400 sq. ft. of garage space and moved into a small industrial complex. This was the second of three moves that the company would make in its 26-year history.
Comprehensive service offerings under one roof
Today, Your Bindery Finishing occupies 13,000 sq. ft. of space and offers more finishing services in one location than any other trade bindery in Colorado, according to Luann Wood. The company accomplishes it all with just 11 employees, including three family partners – Luann, Curtis (company vice president) and Luann’s sister, Kirsten, who manages the staff and schedules production. The company also offers PUR and EVA perfect binding, three-knife trimming, collating flat sheets and folded signatures, multi-head drilling, folding and mechanical binding – double loop wire and plastic spiral coil.
The letterpress and diecutting services are offered by KSB Die Cutting, LLC, owned and operated onsite by Wood’s son, Aaron Williams. Williams officially began working in the bindery at age 12. As an adult, he managed Your Bindery Finishing’s letterpress operations until 2006, when he branched out to create his own company. KSB began with one Kluge and then expanded to eight old-style letterpresses and a Scott Ten Thousand tab cutter, which allows for a wide range of letterpress services including diecutting, foil stamping, embossing, index tab cutting and more. “Together, the two companies are capable of performing multiple trade services ‘all under one roof.’ We excel by providing high-end, professionally finished products. Our customers are assured of that,” Wood said.
Having all of these finishing services under one roof offers many advantages. “The biggest advantage for our customers is that we are saving them time and money by providing everything right here,” she explained. “For the printers, we provide peace of mind. They know that if their project is here and if there’s a question or problem, we’re going to call them.” In addition to the company’s printer-based customers, which include small commercial printers and large print houses both in and out of state, Your Bindery Finishing’s typical customers include self-publishers, schools, photographers and government agencies.
Wood said that customers are more than welcome to visit the company at any point during the production process. “We want our customers to feel comfortable at every step in the process, and we want them to look good. That’s our goal.” One of the ways that Your Bindery Finishing accomplishes this goal is by encouraging its employees to constantly ask themselves if they are producing a piece that they are proud of – a piece that they would be willing to pay for out of their own pocket.
Quality control rules the day
Quality is king at Your Bindery Finishing, and the company has many internal controls in place to help ensure top quality products. “Quality control begins with customer service. When an order is received, the customer service team works to ensure that all details have been included before the job moves into production, which saves time and money,” Wood said. Once a job is in production, quality control measures include procedures such as fanning the stock before a machine is loaded with paper to ensure that all stock is going the same direction; making sure the cut marks are in the right place prior to running the job; proofing all of the steps before cutting and measuring at least three times before cutting.
“We even proofread, and our employees have found many typos on materials. We’ve saved the customer money by catching these types of issues before the bindery process is complete – allowing the customer to decide how he/she wants to proceed,” Wood said. The company also encourages accurate counts. “If we’re short, then we need to call the customer. If we’re over, then we need to package it up and send it to the customer. Wood said that Your Bindery Finishing’s employees are trained to understand how their work is reflecting the customer’s professional image.
In addition to quality control measures, Your Bindery Finishing tries to incorporate lean manufacturing strategies as well. “We are constantly asking ourselves, ‘How can we handle this piece less? How can we move it through more efficiently?’ That’s something we’re always assessing,” Wood said. For the company’s print customers, fewer hands represent a savings on time and delivery costs – the printer’s drivers don’t have to go to so many locations, and the outside coordinators don’t have to make so many phone calls. “Essentially, several different services are handled by our company under one roof, rather than our customers having to deal with up to five different companies, which may be the case when using other trade binderies,” Wood said.
Managed growth
Another avenue of success for Your Bindery Finishing has been managed growth at a slow, steady pace. “In the beginning, we owned a few pieces of equipment and our niche was small runs, but as our reputation grew, our customers began pushing us to expand our services. With each service that we’ve added, we’d start small to perfect the new services from the inside out,” Wood said. “Since we started small, the 24- or 12-hour – and sometimes same day turnaround – that is demanded from today’s customers is nothing new for us. Our employees are excellent people, and I feed them a lot of oranges and coffee.”
Once the company got comfortable with its expansion of services, then it would seek to invest in more automated machinery to enhance these services. Over time, Your Bindery Finishing has added two large-format folders and has improved on its collators – they are all now vacuum-fed, high-speed and computer-run. Then, the company moved into mechanical binding – spiral and wire-o, investing in a few small table top machines to work with, as well as a high-speed punch and automatic wire inserters.
Through it all, perfect binding has continued to be the lion’s share of Your Bindery Finishing’s business for more than 20 years, currently representing 40 percent of the work load. The company can accommodate test books and press runs as small as one or two books, all the way up to large runs. Five years ago, Your Bindery Finishing made a conscious decision to begin using PUR polyurethane glue, and today the company believes it is still the only trade bindery in Colorado to offer this service.
Making the leap to PUR
Your Bindery Finishing ventured into PUR binding after working with a client who had produced some books on mountain climbing. After the books had been stored in sub-zero Colorado temperatures, they began to crack. “We rebound the books, but once again they were frozen in storage, and I felt horrible,” Wood said. She began researching PUR glue, which was supposed to hold up in a variety of conditions including extreme cold or hot weather, in addition to PUR’s attractive capabilities for use with enamel stocks and digitally produced work. Wood researched further by touring a bindery in London that was installing a PUR system at that time, and by talking to the company about why they were making the move to PUR binding.
When Wood returned, she completed additional research on US companies that were using PUR binding. “During the process, I discovered that when our customers used digital print stock it sometimes repelled our glue and, consequently, we were spending too much time wiping fuser oil off the books.” As the next step in the research process, Your Bindery Finishing sent test books to Standard Horizon, “which was very helpful, and then we toured a facility in Salt Lake City that was using PUR,” Wood said. “That helped us to make our final decision, and I’m very happy that we made the leap.”
Wood said that the cost of the PUR glue product itself is cost-prohibitive, which is what she believes has kept other companies from making the leap to PUR. “For our company, PUR is three times the cost of our other glue, and it does require more maintenance for the machines – the glue pot has to be drained daily. Some companies just don’t want to make these investments, but we have found that the outcome of the product – hands-down – outweighs the additional cost of glue and maintenance,” Wood said. In addition, by using PUR adhesive, Your Bindery Finishing has been able to push its binder to 1/16th of an inch, where most companies stop at 1/8th of an inch. “Having that PUR binder really has given us a lot of flexibility in our perfect binding services,” Wood said.
After perfect binding, collating for mechanical or perfect binding represents 25 percent of Your Bindery Finishing’s work, followed by mechanical binding of calendars, catalogs and training manuals, as well as folding brochures, direct mail pieces, flyers and promotional pieces. Both mechanical binding and folding represent 10 percent of the work, and booklets, finished cutting and drilling each represent five percent of the company’s current work load.
Awards and favorite projects
Although Your Bindery Finishing’s work speaks for itself, the company has entered PUR-bound books that it has produced into local printing awards competitions and has won many accolades in the last few years. A black and white photobook featuring breast cancer survivors called Cup Half Full won the 2010 Print Excellence Gold Award for superior craftsmanship in the Printing Industries of America Mountain States competition.
“Initially the book had been printed and perfect bound by one of our competitors, but the photographer rejected their work and came to us. It’s a wonderful piece – the photos in this book are just fantastic!” Wood said. The book features quotes from and photos of breast cancer survivors in their daily lives, with their families and sometimes even bravely sharing their scars or bald head for the world to see.
Another award-winning piece was a CD booklet project for an eclectic local band, Devotchka. The booklet features a soft-touch aqueous coating, with sheets that were ½-folded to give a double thickness. The printer who produced the piece also produced a companion hardcover box, and it won a Best of Show award from PIA Mountain States as well.
Looking to the future
Your Bindery Finishing is always looking to the future, and the company recently added short-run casebinding to its range of services, which will enable the company to produce yearbooks, family history projects and more. As far as its customer markets are concerned, the company plans to keep working primarily with the Denver market. In addition to her role as president, Wood serves as the company’s sales person and she maximizes her time by networking through many local organizations, including the Printing Industries of America (PIA) Mountain States chapter.
Other marketing initiatives include a quarterly postcard that is sent to both current and past customers, as well as a St. Patrick’s Day celebration for employees and customers. Approximately 100 people attend the event that is co-sponsored by the PIA Mountain States chapter, along with several other local vendors. It’s a chance for Your Bindery Finishing’s employees to mingle with customers and share their knowledge about their work. “The staff serves the food and really enjoys socializing with our customers. They are outfitted in dark green T-shirts to help advertise our services,” Wood said.
Wood also is involved with the Binding Industries Association (BIA) and participates in many workshops, conferences and continuing education opportunities. She believes that the knowledge that she brings back to her company about prepress and printing helps the company overall with the finishing side of the business. “This cross-over knowledge will allow us to keep the quality of our work high,” Wood said.
Above all these activities, Wood credits the company’s website as its greatest sales tool. She said that the goal for the website was to create a tool to educate customers and potential customers – especially the printers – about Your Bindery Finishing’s services and to save some time from having to make a lot of phone calls. “Our website and our reputation for top-quality work have helped us to reach new avenues of business. Printers and customers from across the country have found us online, especially because of our PUR services, and we’ve been able to get work that wasn’t available to us before, all because of our website.”
Wood sees this trend continuing well into the future. With its comprehensive finishing services, including PUR perfect binding, rigorous quality control measures, managed growth and creative marketing strategies, the future looks bright for Your Bindery Finishing.