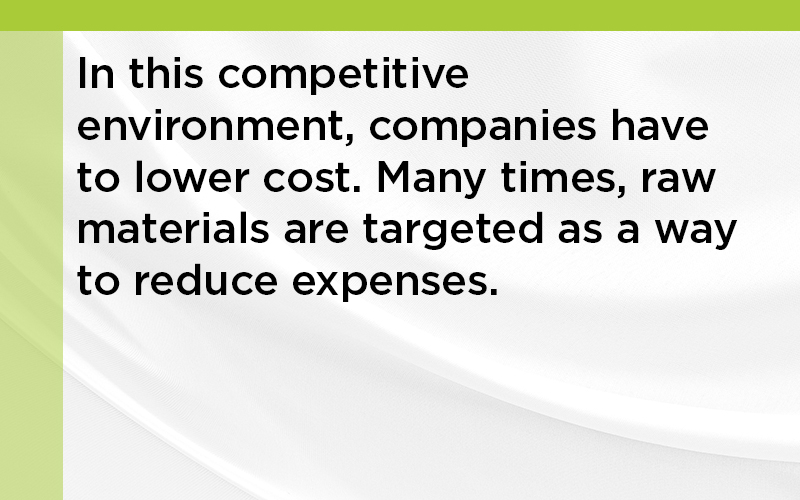
by Dave Senter, Eska Graphic Board USA B.V.
One of the most popular questions I get now that I’m in the graphic board industry – and it’s a question I often received when I was in the adhesive industry, too – is, “What’s the proper amount of adhesive to use?” The answer is that it depends on a lot of factors.
Factors Affecting the Adhesive/Board Bond
There are different applications in the book industry, and adhesive requirements vary based on the application. During my time as a glue guy, my job was to sell glue; but my bigger job was to make sure my customers weren’t creating problems for themselves with the wrong adhesive or inadequate application. It’s best to follow the mantra “less is more,” and then adjust as needed.
There is a fine line between what enough is and what is too much. In both casemaking and casing-in, operators will start out at a level that they believe is sufficient coverage for that substrate on a particular board, but they often don’t see or know the bigger picture. What issues are happening farther down the process? I always stress to operators the “less is better” rule.
Another common adhesion issue actually is caused by the speed of the machine. An operator may have an adhesive that isn’t properly matched to the speed being run on the machine, which inhibits the application of the proper amount of adhesive.
In addition, environmental factors can complicate the adhesion bond. When the weather is cold and the relative humidity is low, paper products and wood fibers react. As a result, the fibers in a particular board, when exposed to low humidity, become very dry; just as a piece of wood would react. In the summer, when the humidity is high, the fibers swell as they take on moisture. The amount of adhesive that is required varies based on the condition of the fibers.
At the casing-in process, when applying a case to a book block using a casing-in paste, less is always better in the summer because there should be equilibrium on both sides of the board from the adhesive. So, if the casemaking process applies
Solving Adhesion Issues
If adhesion issues are experienced, what is the issue? Why is the glue not sticking? Is it setting up too fast? Is it setting up too slow? Is the glue on too thick? Is it on too thin? Is it the proper adhesive for the substrate? Not every adhesive works on every substrate.
In the 35 years I have been in the industry, working with both adhesive and board, one thing has been consistently true. When there is a problem, it never seems to be recognized soon enough. Operators will work through a problem to get to the next operation; and then, further down the line, something happens. When the issue is back-tracked through production, the problem often is found to have started much earlier in the process. If theres a problem, when should an adhesive or board supplier be consulted? The timing is easy: once all basics have been checked (temperatures, solids content, coverage and machine speed) and the problem still exist, then it’s time to make the call.
The adhesion issue could be caused by a number of factors, such as incompatibility between adhesives and substrates. It could be caused by using a substrate that has been modified rather than the one typically used in a particular operation. It could be a change in a process or material that wasn’t adequately communicated.
In this competitive environment, companies have to lower cost. Many times, raw materials are targeted as a way to reduce expenses. Once a vendor has supplied a solution to an operation, adequate testing must be performed. Results need to be documented and reviewed, and possible fail points should be identified before changes should be made. If this is not performed and different components are introduced to an operation, the possibility of an adhesion problem occurring is greater. At that moment, it’s time to raise a red flag and say, “Something has changed, and we’re not sure what.” Testing a new product before bringing it in can help to avoid potential adhesion problems.
Dave Senter is sales account manager at Eska Graphic Board USA B.V. Eska Graphic Board is a producer and supplier of top quality graphic board for hardcover books, files, ring binders, diaries, albums, games, puzzles, displays, show cards and luxury packaging. The board is marketed under the brand name Eska and is well-known for its excellent and consistent lay-flat, stay-flat quality. All Eska products are made of recovered paper, and FSC certification has been acquired for all products. For more information, visit www.eskagraphicboard.com.